The process of soaking during heat treatment is a critical step that ensures uniform temperature distribution throughout the material being treated. It involves holding the material at a specific temperature for a predetermined period, allowing the heat to penetrate evenly and achieve the desired microstructural changes. This step is essential for achieving consistent mechanical properties, such as hardness, strength, and ductility, across the entire workpiece. The duration and temperature of soaking depend on factors like material type, size, and the desired outcome of the heat treatment process.
Key Points Explained:
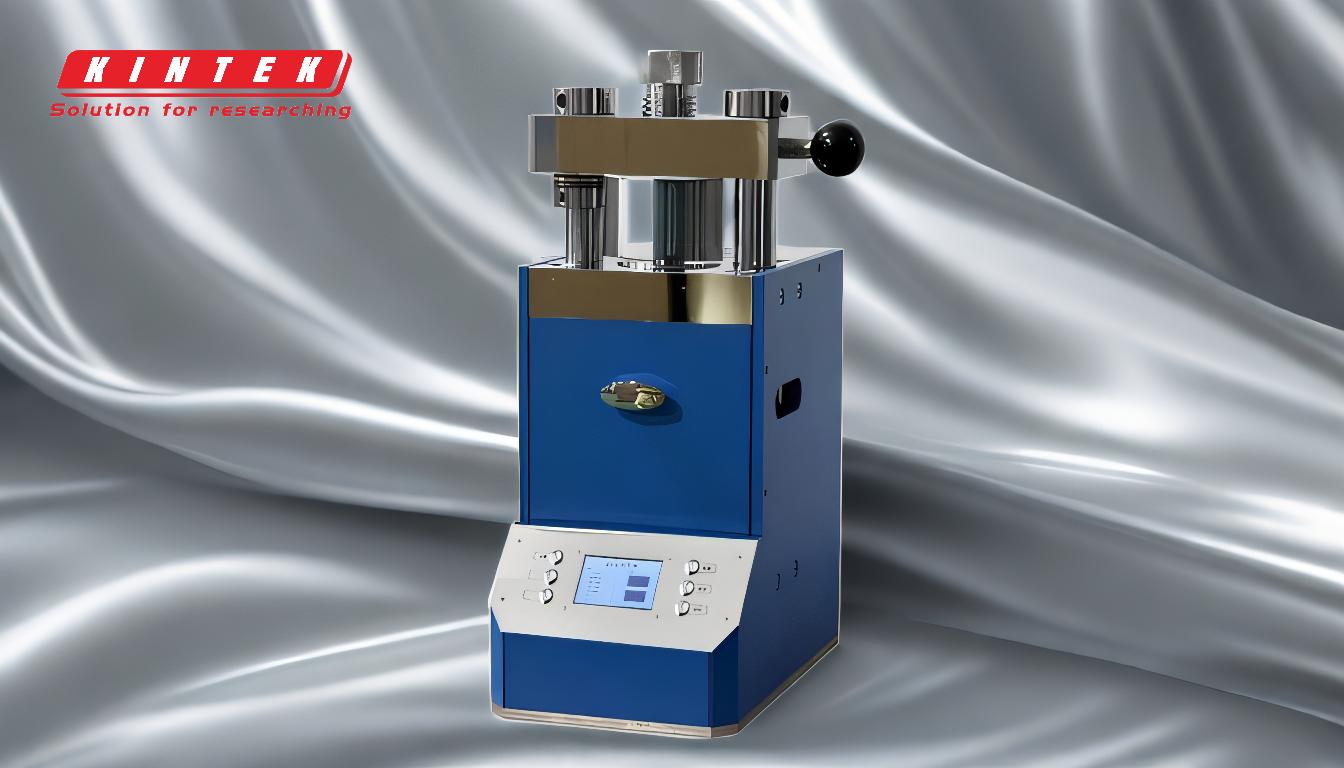
-
Definition of Soaking in Heat Treatment:
- Soaking refers to the phase in heat treatment where the material is held at a specific temperature for a set period. This ensures that the entire workpiece reaches a uniform temperature, which is critical for achieving consistent material properties.
- It allows the material to undergo the necessary phase transformations or diffusion processes required for the desired mechanical or chemical properties.
-
Purpose of Soaking:
- Uniform Temperature Distribution: Ensures that heat penetrates evenly throughout the material, preventing uneven heating or cooling that could lead to defects like warping or cracking.
- Achieving Desired Microstructure: Facilitates phase transformations (e.g., austenitization in steel) or diffusion processes that improve material properties.
- Stress Relief: Helps in reducing internal stresses that may have developed during previous manufacturing processes.
-
Factors Influencing Soaking:
- Material Type: Different materials (e.g., steel, aluminum, titanium) require different soaking temperatures and durations based on their thermal and chemical properties.
- Workpiece Size and Shape: Larger or thicker components require longer soaking times to ensure heat penetrates to the core.
- Desired Outcome: The specific mechanical or chemical properties required (e.g., hardness, toughness) dictate the soaking parameters.
-
Steps in the Soaking Process:
- Heating Phase: The material is gradually heated to the target temperature to avoid thermal shock.
- Soaking Phase: The material is held at the target temperature for the required duration. This duration is calculated based on the material's thickness and thermal conductivity.
- Cooling Phase: After soaking, the material is cooled at a controlled rate, which may involve quenching, air cooling, or furnace cooling, depending on the desired outcome.
-
Practical Considerations:
- Furnace Design: The furnace must maintain a stable temperature throughout the soaking process to avoid fluctuations that could affect the material's properties.
- Monitoring and Control: Advanced heat treatment furnaces use thermocouples and controllers to ensure precise temperature regulation during soaking.
- Safety Measures: Proper ventilation and handling procedures are essential to prevent accidents due to high temperatures or chemical reactions.
-
Applications of Soaking in Heat Treatment:
- Annealing: Soaking is used to soften materials, improve machinability, and relieve internal stresses.
- Hardening: In processes like quenching, soaking ensures uniform austenitization before rapid cooling to achieve high hardness.
- Tempering: Soaking at lower temperatures after hardening helps achieve the desired balance of hardness and toughness.
By understanding and optimizing the soaking process, manufacturers can ensure that heat-treated materials meet the required specifications for strength, durability, and performance.
Summary Table:
Aspect | Details |
---|---|
Definition | Holding material at a specific temperature for uniform heat penetration. |
Purpose | Ensures uniform temperature, stress relief, and desired microstructure. |
Key Factors | Material type, workpiece size, and desired outcome. |
Process Steps | Heating, soaking, and controlled cooling. |
Applications | Annealing, hardening, and tempering. |
Optimize your heat treatment process with expert guidance—contact us today!