Thin film coating is a sophisticated process used to deposit thin layers of material onto a substrate, often to enhance its properties such as conductivity, reflectivity, or durability. The process typically involves several key steps, including material selection, deposition, and post-treatment. The most common techniques for thin film deposition are Physical Vapour Deposition (PVD) and Chemical Vapour Deposition (CVD), each with its own set of methods like evaporation, sputtering, and atomic layer deposition (ALD). The choice of method depends on factors such as the desired film thickness, the type of material being deposited, and the specific application requirements. The process is critical in industries ranging from electronics to optics, where precise control over film properties is essential.
Key Points Explained:
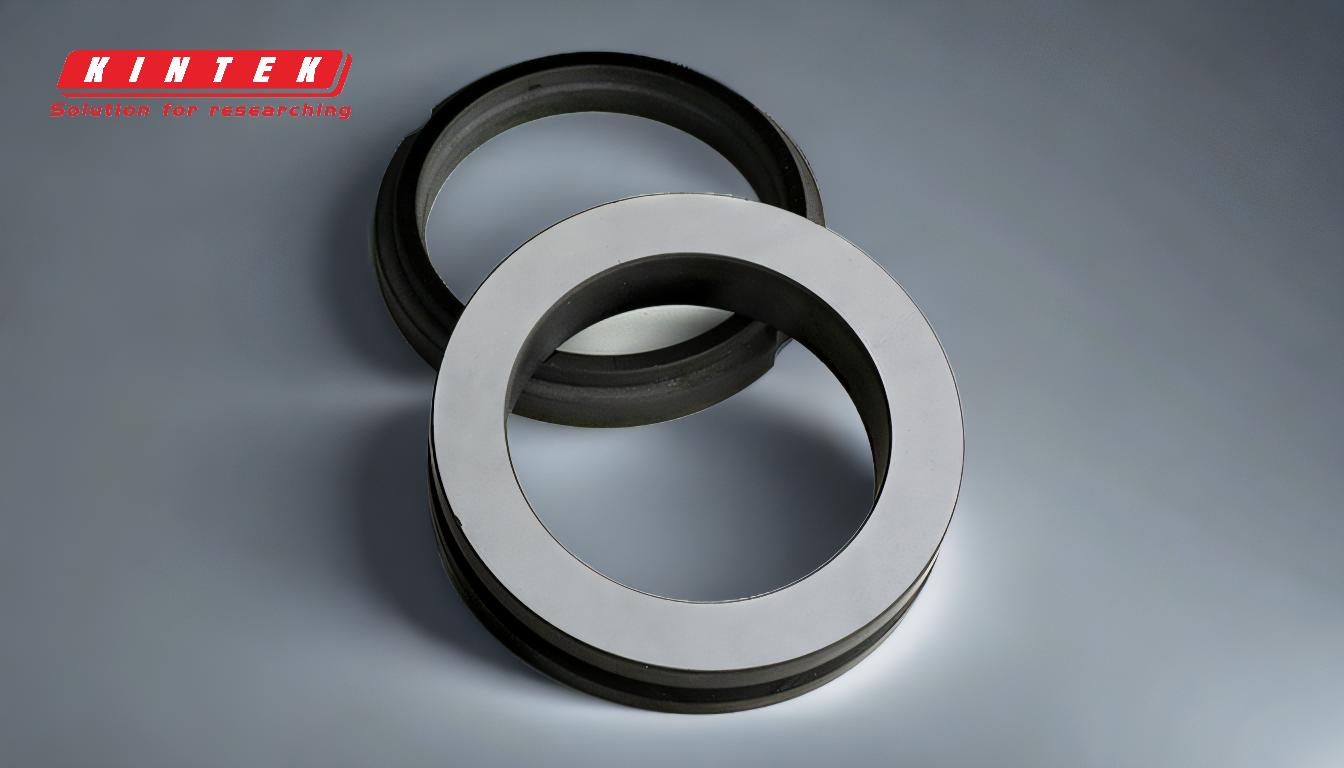
-
Material Selection:
- The first step in the thin film coating process is selecting the appropriate material (target) that will be deposited onto the substrate. This material must be pure and suitable for the desired application, whether it's for enhancing electrical conductivity, optical properties, or mechanical strength.
-
Substrate Preparation:
- Before deposition, the substrate must be prepared to ensure proper adhesion and uniformity of the thin film. This may involve cleaning, etching, or applying a primer layer to the substrate surface.
-
Deposition Techniques:
-
Physical Vapour Deposition (PVD): This technique involves physically transferring material from a source to the substrate. Common PVD methods include:
- Evaporation: The target material is heated until it evaporates, and the vapor condenses on the substrate.
- Sputtering: High-energy particles bombard the target material, causing atoms to be ejected and deposited onto the substrate.
- Chemical Vapour Deposition (CVD): In this method, chemical reactions are used to deposit a thin film onto the substrate. The process involves introducing a volatile precursor into a reaction chamber, where it decomposes or reacts to form the desired film.
- Atomic Layer Deposition (ALD): ALD is a more precise method where the film is deposited one atomic layer at a time, allowing for extremely thin and uniform coatings.
- Spray Pyrolysis: This technique involves spraying a solution containing the desired material onto the substrate, followed by thermal decomposition to form a thin film.
-
Physical Vapour Deposition (PVD): This technique involves physically transferring material from a source to the substrate. Common PVD methods include:
-
Transport Medium:
- The target material is transported to the substrate through a medium, which could be a vacuum (in PVD) or a fluid (in some CVD processes). The choice of medium affects the deposition rate and the quality of the film.
-
Deposition Process:
- The actual deposition of the thin film occurs when the target material reaches the substrate and adheres to its surface. The conditions during deposition, such as temperature, pressure, and deposition rate, are carefully controlled to achieve the desired film properties.
-
Post-Deposition Treatment:
- After deposition, the thin film may undergo additional treatments to improve its properties. This could include annealing (heat treatment) to enhance adhesion, reduce stress, or improve crystallinity.
-
Film Analysis:
- The final step involves analyzing the properties of the deposited film, such as thickness, uniformity, and adhesion. This analysis helps in determining whether the deposition process needs to be adjusted to meet the desired specifications.
-
Applications:
- Thin film coatings are used in a wide range of applications, including:
- Electronics: For creating conductive layers in semiconductors and microelectronics.
- Optics: For anti-reflective coatings on lenses and mirrors.
- Energy: In solar cells and batteries, where thin films can improve efficiency.
- Medical Devices: For coatings that enhance biocompatibility or reduce friction.
- Thin film coatings are used in a wide range of applications, including:
By understanding these key points, one can appreciate the complexity and precision required in the thin film coating process, as well as its critical role in modern technology and industry.
Summary Table:
Key Steps | Details |
---|---|
Material Selection | Choose pure, application-specific materials for conductivity or durability. |
Substrate Preparation | Clean, etch, or prime the substrate for better adhesion and uniformity. |
Deposition Techniques | PVD (evaporation, sputtering), CVD, ALD, or spray pyrolysis. |
Transport Medium | Vacuum (PVD) or fluid (CVD) for material transfer. |
Deposition Process | Controlled temperature, pressure, and rate for desired film properties. |
Post-Deposition Treatment | Annealing to enhance adhesion, reduce stress, or improve crystallinity. |
Film Analysis | Measure thickness, uniformity, and adhesion for quality assurance. |
Applications | Electronics, optics, energy, and medical devices. |
Discover how thin film coating can elevate your project—contact our experts today!