Vacuum hardening is a specialized heat treatment process used to enhance the mechanical properties of metal workpieces, such as hardness, wear resistance, and strength, while minimizing surface oxidation and contamination. The process involves heating the workpiece in a vacuum environment to a specific temperature, holding it at that temperature to achieve uniform heating, and then cooling it rapidly using inert gases. The vacuum environment ensures a clean, oxidation-free surface, which is critical for achieving high-quality results. The process is highly controlled, leveraging advanced vacuum systems, heating mechanisms, and cooling techniques to ensure precision and consistency.
Key Points Explained:
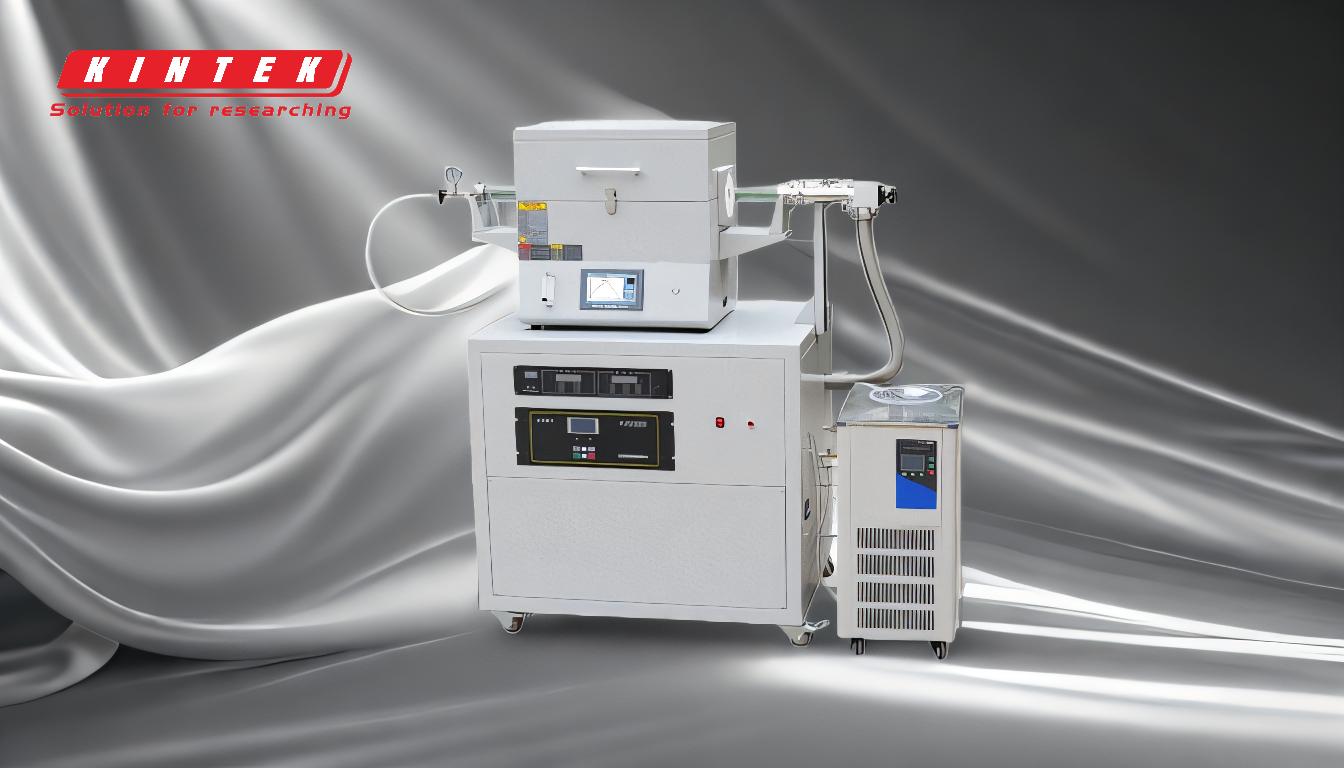
-
Vacuum Environment Creation:
- The process begins by creating a vacuum inside the vacuum hardening furnace. This is achieved using a combination of vacuum pumps, including mechanical pumps, booster pumps, and diffusion pumps.
- Mechanical pumps are used initially to reduce the pressure from atmospheric levels (around 105 torr) to about 10 torr. Below 20 torr, the efficiency of mechanical pumps declines, and booster pumps are activated to further reduce the pressure.
- Diffusion pumps are then employed to achieve the highest vacuum levels, typically around 7 × 10^-3 Pa, which is essential for preventing oxidation and contamination during the heating phase.
-
Heating Phase:
- Heating in a vacuum furnace is primarily achieved through radiation. The workpiece is heated uniformly by ensuring proper spacing within the furnace chamber. This prevents uneven heating and ensures consistent material properties.
- The temperature is carefully controlled using automated temperature control instruments. The workpiece is heated to a specific temperature, depending on the material and desired properties, and held at that temperature for a predetermined period to ensure uniform heat distribution.
-
Cooling Phase:
- After the heating phase, the workpiece is rapidly cooled to achieve the desired hardness. This is done by introducing an inert gas, such as argon, into the vacuum chamber. The gas is pumped in at a controlled rate to ensure precise cooling.
- The rapid cooling process, also known as quenching, is critical for achieving the desired microstructure and mechanical properties in the workpiece. The inert gas ensures that the cooling process is free from oxidation and contamination.
-
Leak Management and Maintenance:
- Maintaining the integrity of the vacuum environment is crucial for the success of the process. Any leaks in the furnace can compromise the vacuum and lead to oxidation or contamination.
- Temporary leaks can be addressed using high-temperature sealants while the furnace is in operation. However, once the furnace is stopped, a thorough inspection and repair process should be conducted. This includes welding cracked parts, replacing aged or damaged gaskets and snap rings, and tightening loose screws.
-
Process Automation and Control:
- The entire vacuum hardening process is highly automated, with precise control over temperature, vacuum levels, and cooling rates. This ensures repeatability and consistency in the heat treatment process.
- Automated systems monitor and adjust the parameters in real-time, ensuring that the workpiece undergoes the exact treatment required to achieve the desired properties.
-
Applications and Benefits:
- Vacuum hardening is widely used in industries that require high-performance components, such as aerospace, automotive, and tool manufacturing. The process is particularly beneficial for materials that are prone to oxidation or require a high degree of precision in heat treatment.
- The key benefits of vacuum hardening include improved surface quality, enhanced mechanical properties, and reduced distortion compared to traditional heat treatment methods.
By following these steps and leveraging the capabilities of a vacuum hardening furnace, manufacturers can achieve superior results in heat treatment, ensuring that their components meet the highest standards of quality and performance.
Summary Table:
Step | Description |
---|---|
Vacuum Creation | Use mechanical, booster, and diffusion pumps to achieve high vacuum levels. |
Heating Phase | Heat workpiece uniformly via radiation in a controlled vacuum environment. |
Cooling Phase | Rapidly cool with inert gases like argon to achieve desired hardness. |
Leak Management | Inspect and repair leaks to maintain vacuum integrity. |
Automation & Control | Use automated systems for precise temperature, vacuum, and cooling control. |
Applications | Ideal for aerospace, automotive, and tool manufacturing industries. |
Discover how vacuum hardening can elevate your metal components—contact us today for expert guidance!