Vacuum hardening is a specialized heat treatment process performed in a vacuum hardening furnace to enhance the mechanical and chemical properties of metals. The process involves heating materials to high temperatures in a vacuum environment, which eliminates oxidation and contamination, ensuring a clean and precise treatment. Vacuum hardening is particularly beneficial for improving hardness, wear resistance, and corrosion resistance in materials like tool steels, stainless steels, and high-performance alloys. The controlled environment also ensures consistent and repeatable results, making it ideal for industries with stringent quality standards, such as aerospace, automotive, and medical device manufacturing.
Key Points Explained:
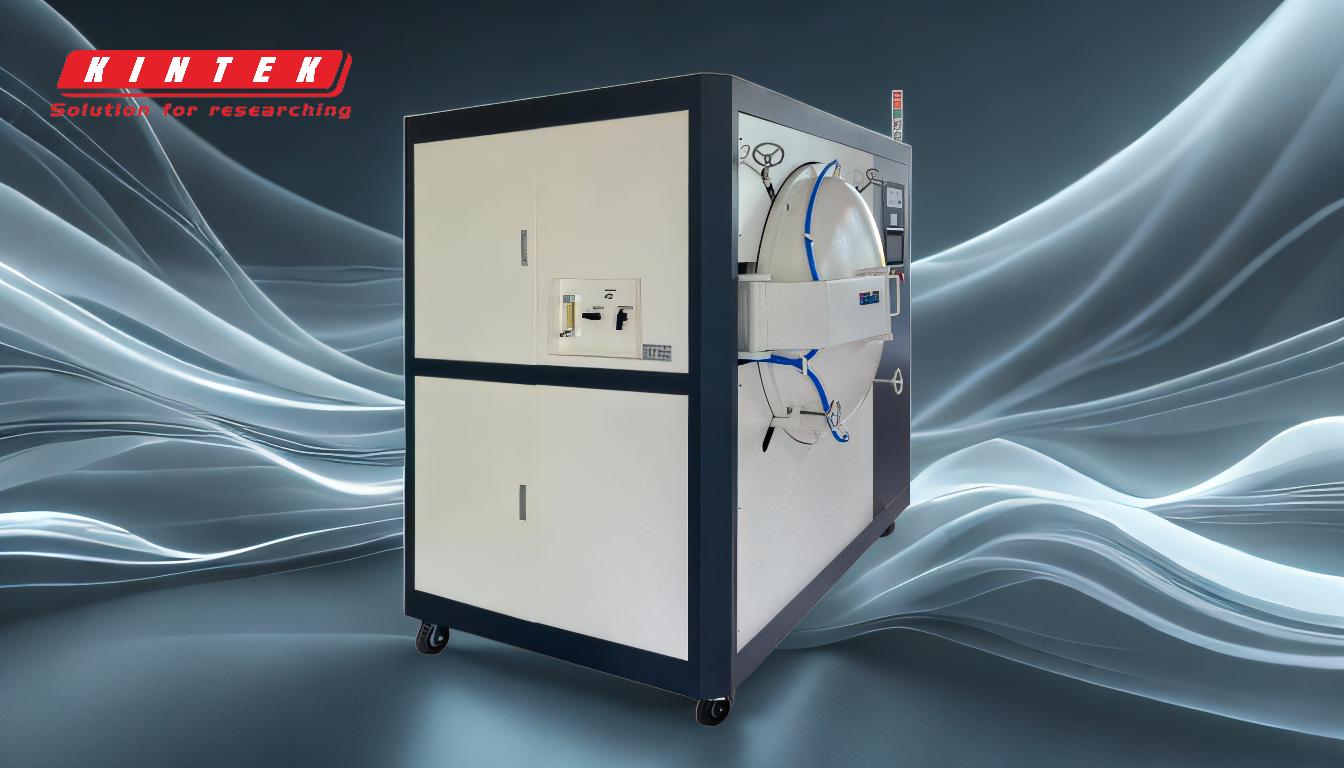
-
Elimination of Oxidation and Contamination:
- In a vacuum environment, the absence of oxygen prevents oxidation, which can degrade the surface quality of metals. This is particularly important for materials like stainless steel and titanium alloys, where surface integrity is critical.
- The vacuum also removes contaminants such as oils, greases, and other impurities that could otherwise affect the material's properties during the hardening process.
-
Enhanced Mechanical Properties:
- Vacuum hardening significantly improves hardness, wear resistance, and fatigue strength. For example, tool steels treated in a vacuum hardening furnace exhibit superior cutting performance and durability.
- The process also enhances elasticity and shear strength, making the materials more suitable for high-stress applications.
-
Improved Corrosion Resistance:
- By preventing oxidation and maintaining a clean surface, vacuum hardening enhances the material's resistance to corrosion. This is especially beneficial for components used in harsh environments, such as marine or chemical processing industries.
-
Consistency and Repeatability:
- The controlled environment of a vacuum hardening furnace ensures precise temperature and pressure conditions, leading to consistent and repeatable results. This predictability is crucial for industries with strict quality assurance standards, such as aerospace and medical device manufacturing.
-
Versatility in Material Applications:
- Vacuum hardening is suitable for a wide range of materials, including stainless steel, titanium alloys, cemented carbide, and bearing steel. This versatility makes it a preferred choice for industries requiring high-performance materials.
-
Integration with Other Processes:
- Vacuum hardening can be combined with other heat treatment processes, such as tempering or quenching, to achieve specific material properties. For instance, rapid cooling using inert gases like nitrogen or argon can further enhance the material's hardness and strength.
-
Environmental and Economic Benefits:
- The vacuum environment eliminates the need for protective atmospheres or chemical treatments, reducing waste and environmental impact.
- The process also minimizes material loss due to oxidation, leading to cost savings in the long run.
In summary, vacuum hardening in a vacuum hardening furnace is a highly effective method for improving the performance and durability of metals. Its ability to provide a clean, controlled environment ensures superior material properties, making it indispensable for industries demanding high-quality, reliable components.
Summary Table:
Key Benefits of Vacuum Hardening | Details |
---|---|
Eliminates Oxidation & Contamination | Prevents surface degradation and removes impurities. |
Enhances Mechanical Properties | Improves hardness, wear resistance, and fatigue strength. |
Boosts Corrosion Resistance | Ideal for harsh environments like marine and chemical industries. |
Ensures Consistency & Repeatability | Precise temperature control for reliable results. |
Versatile Material Applications | Suitable for stainless steel, titanium alloys, and more. |
Environmental & Economic Benefits | Reduces waste and material loss, saving costs. |
Upgrade your metal components with vacuum hardening—contact our experts today to learn more!