Sintering is a fundamental process in materials science where particles are fused together through heat and pressure, without reaching the material's melting point. This process involves several stages, including powder compaction, controlled heating, particle diffusion, and cooling, resulting in a dense, cohesive structure. Sintering can occur naturally or be facilitated by specialized equipment like sintering furnaces, which create controlled environments to optimize the process. The science behind sintering revolves around atomic diffusion, particle bonding, and the elimination of voids, making it essential for producing high-performance materials such as ceramics, metals, and polymers.
Key Points Explained:
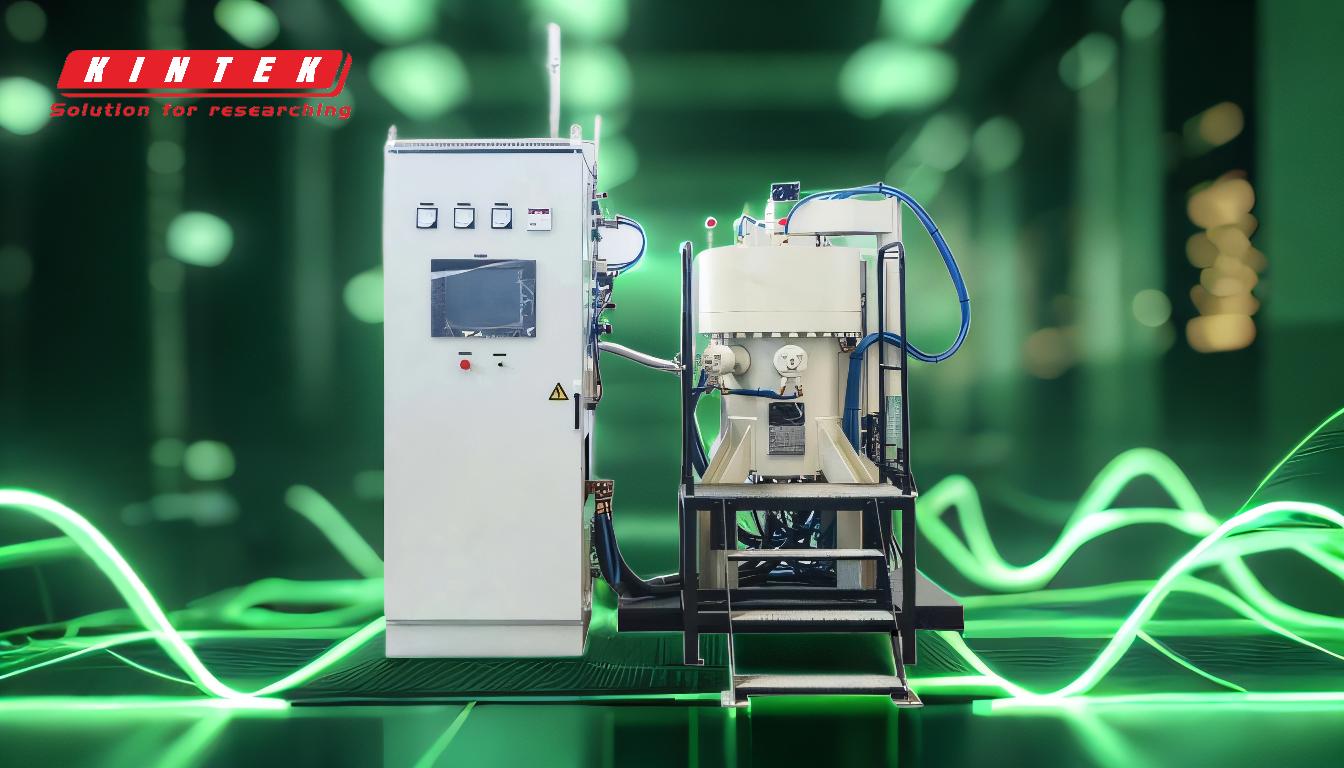
-
Atomic Diffusion and Particle Bonding:
- Sintering relies on the movement of atoms across particle boundaries, driven by heat and pressure. This movement, known as diffusion, allows particles to bond and form a solid structure.
- In the initial stages, particles develop necks at contact points, which grow as atoms migrate. This reduces porosity and increases material density.
- The process is governed by solid-state diffusion, where particles weld together without melting, preserving the material's properties.
-
Stages of the Sintering Process:
- Powder Compaction: Raw materials, often in powder form, are compacted under pressure to create a uniform shape and eliminate voids.
- Controlled Heating: The compacted material is heated in a sintering furnace to a temperature below the melting point, facilitating particle bonding.
- Diffusion and Densification: During heating, particles undergo diffusion, leading to neck formation and densification. This stage is critical for achieving the desired material properties.
- Cooling: The sintered product is cooled, allowing it to solidify into a rigid and cohesive structure.
-
Role of Equipment in Sintering:
- Sintering furnaces are essential for creating controlled environments that optimize the sintering process. These furnaces can operate under various conditions, such as vacuum, hydrogen, or high pressure, depending on the material being processed.
- For example, a vacuum sintering furnace prevents oxidation and contamination, improving the quality of the final product. Hot press sintering furnaces combine heat and pressure to achieve denser materials.
-
Applications of Sintering:
- Sintering is widely used in manufacturing ceramics, metals, and polymers. It is particularly important for producing refractory alloys like tungsten and molybdenum, which require high temperatures and controlled environments.
- The process is also used in powder metallurgy to create complex shapes with minimal material waste.
-
Environmental and Operational Considerations:
- Water and other agents play a role in cooling and removing harmful by-products during sintering. For instance, water vapor combines with pressing agents to form harmless gases like CO or CO2.
- Cold sintering, an emerging technique, uses transient solvents and pressure to consolidate polymer powders, offering a more energy-efficient alternative to traditional methods.
By understanding the science behind sintering, manufacturers can optimize the process to produce high-quality materials with tailored properties. The use of advanced equipment like sintering furnaces further enhances the precision and efficiency of this critical manufacturing technique.
Summary Table:
Key Aspect | Description |
---|---|
Atomic Diffusion | Movement of atoms across particle boundaries, driven by heat and pressure. |
Stages of Sintering | Powder compaction, controlled heating, diffusion and densification, and cooling. |
Role of Equipment | Sintering furnaces create controlled environments for optimized results. |
Applications | Used in ceramics, metals, polymers, and refractory alloys like tungsten. |
Environmental Considerations | Water and solvents aid in cooling and removing harmful by-products. |
Discover how sintering can revolutionize your material production—contact our experts today!