The sintering process is a manufacturing technique that fuses powdered materials into a solid mass using heat and pressure, without reaching the material's melting point. This process is widely used in industries such as metallurgy, ceramics, and plastics to create dense, durable products. The key steps include preparing the powdered material, compressing it into the desired shape, and heating it to facilitate atomic diffusion, which bonds the particles together. Sintering enhances material properties like strength, density, and structural integrity, making it essential for producing components ranging from steel to advanced ceramics.
Key Points Explained:
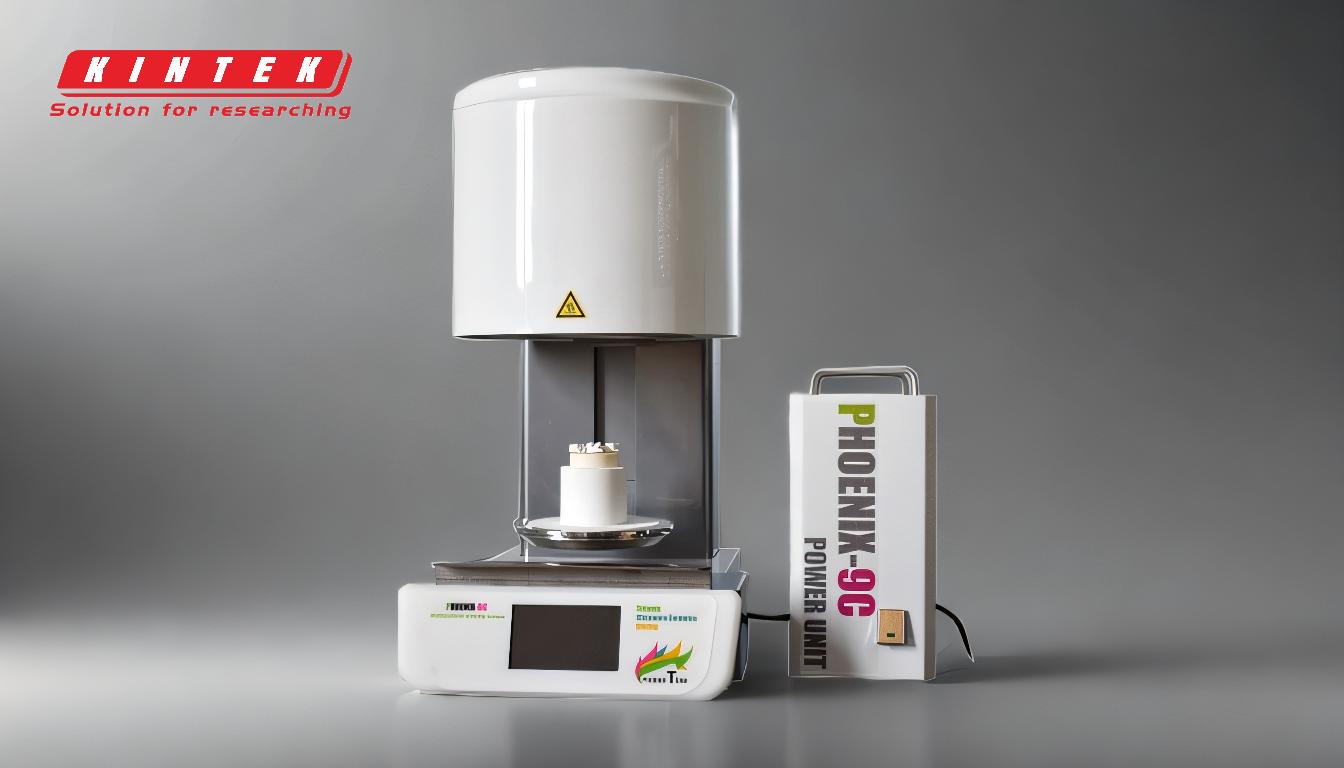
-
Definition and Purpose of Sintering
- Sintering is a process that bonds powdered materials into a solid mass through heat and pressure, without melting the material.
- It is used to create dense, strong, and durable products in industries like metallurgy, ceramics, and plastics.
- The primary goal is to reduce porosity and increase structural integrity by fusing particles at the atomic level.
-
Key Steps in the Sintering Process
-
Preparation of Powdered Material:
- The raw material is ground into a fine powder and mixed with coupling agents or binders if necessary.
- This step ensures uniformity and consistency in the final product.
-
Compression:
- The powder is pressed into the desired shape using molds or high-pressure tools.
- This step creates a "green compact," which is a loosely bonded structure ready for sintering.
-
Heating and Consolidation:
- The green compact is heated in a furnace to a temperature below the material's melting point.
- Heat facilitates atomic diffusion, allowing particles to bond and densify.
-
Cooling and Solidification:
- After sintering, the material is cooled to solidify into a unified, dense mass.
-
Preparation of Powdered Material:
-
Types of Sintering
-
Solid-State Sintering:
- Particles bond through atomic diffusion without any liquid phase.
- Commonly used for metals and ceramics.
-
Liquid-Phase Sintering (LPS):
- A small amount of liquid phase is introduced to accelerate particle bonding.
- Often used for materials with high melting points or complex shapes.
-
Solid-State Sintering:
-
Applications of Sintering
-
Metallurgy:
- Used to produce steel, iron, and other metal components for industrial use.
- Example: Sintered iron ore is used in blast furnaces to produce steel.
-
Ceramics:
- Creates strong, heat-resistant ceramic products like tiles, insulators, and cutting tools.
-
Plastics:
- Produces durable plastic components with enhanced mechanical properties.
-
Metallurgy:
-
Advantages of Sintering
-
Improved Material Properties:
- Increases density, strength, and durability of the final product.
-
Cost-Effective:
- Reduces material waste and energy consumption compared to melting processes.
-
Versatility:
- Can be used for a wide range of materials and complex shapes.
-
Improved Material Properties:
-
Challenges and Considerations
-
Temperature Control:
- Precise control of heating and cooling rates is critical to avoid defects.
-
Porosity Management:
- While sintering reduces porosity, some residual pores may remain, affecting material performance.
-
Material Selection:
- Not all materials are suitable for sintering; some may require additional binders or additives.
-
Temperature Control:
-
Industrial Implementation
-
Equipment:
- Furnaces, presses, and molds are essential for the sintering process.
-
Process Optimization:
- Parameters like temperature, pressure, and sintering time must be carefully controlled for optimal results.
-
Equipment:
By understanding the sintering process, manufacturers can produce high-quality materials and components tailored to specific industrial needs. This method offers a balance of efficiency, cost-effectiveness, and versatility, making it a cornerstone of modern manufacturing.
Summary Table:
Aspect | Details |
---|---|
Definition | Bonds powdered materials into a solid mass using heat and pressure. |
Key Steps | 1. Preparation of powdered material 2. Compression 3. Heating 4. Cooling |
Types of Sintering | Solid-State Sintering, Liquid-Phase Sintering (LPS) |
Applications | Metallurgy, ceramics, plastics |
Advantages | Improved strength, cost-effectiveness, versatility |
Challenges | Temperature control, porosity management, material selection |
Ready to optimize your material production? Contact us today to learn more about sintering solutions!