The specific heat of pyrolysis refers to the amount of energy required to raise the temperature of a unit mass of biomass during the pyrolysis process. This value varies depending on the type of biomass, the temperature range, and the specific conditions of the pyrolysis process. For example, the specific heat of pyrolysis on a dry basis has been measured between 207-434 kJ/kg at lower temperatures and 800-1600 kJ/kg at higher temperatures (e.g., 500°C). The process is endothermic, meaning it requires external heat input to proceed, and factors such as heating rate, temperature, and residence time significantly influence the energy requirements and the resulting products. Understanding these parameters is crucial for optimizing pyrolysis processes and selecting appropriate equipment.
Key Points Explained:
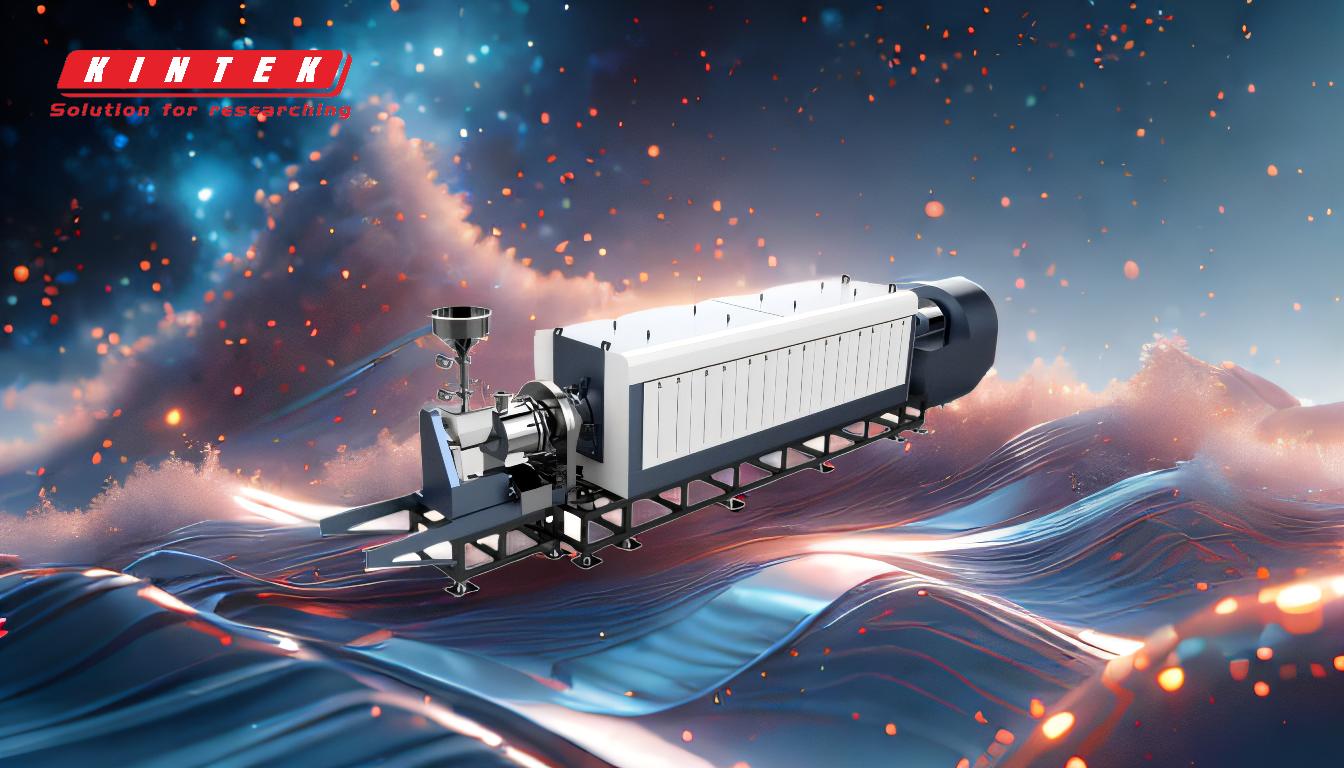
-
Definition of Specific Heat of Pyrolysis:
- The specific heat of pyrolysis is the energy required to raise the temperature of a unit mass of biomass during pyrolysis. It is influenced by the type of biomass, temperature, and process conditions.
- For example, the specific heat of pyrolysis on a dry basis ranges from 207-434 kJ/kg at lower temperatures and 800-1600 kJ/kg at higher temperatures (e.g., 500°C).
-
Endothermic Nature of Pyrolysis:
- Pyrolysis is an endothermic process, meaning it requires external heat to proceed. This heat is necessary to break down the biomass into its constituent components, such as bio-oil, char, and gases.
- Efficient heat transfer is critical to ensure the reaction occurs effectively. Sufficient heat transfer surfaces must be provided to meet the process heat needs.
-
Factors Influencing Specific Heat and Pyrolysis Process:
- Temperature: Higher temperatures generally increase the specific heat of pyrolysis and influence the types of products formed. For instance, at 400°C, the specific heat ranges from 385-646 kJ/kg, while at 500°C, it can reach 800-1600 kJ/kg.
- Heating Rate: The rate of heating directly affects the reaction pathway and the substances produced. Slow pyrolysis involves heating rates of 5 to 7°C/min, while flash pyrolysis involves much higher heating rates, resulting in higher bio-oil yields.
- Residence Time: Longer residence times in slow pyrolysis maximize char production, while shorter residence times in fast or flash pyrolysis favor bio-oil and gas production.
- Atmosphere and Pressure: The absence of oxygen and the pressure conditions also play a role in determining the specific heat and the efficiency of the pyrolysis process.
-
Types of Pyrolysis and Their Specific Heat Requirements:
- Slow Pyrolysis: Characterized by low heating rates (5 to 7°C/min), long residence times, and temperatures around 500°C. The specific heat requirements are generally lower compared to fast or flash pyrolysis, and the main products are char and tar.
- Fast Pyrolysis: Involves higher heating rates and shorter residence times, leading to higher bio-oil yields. The specific heat requirements are higher due to the rapid heating and energy input needed.
- Flash Pyrolysis: Similar to fast pyrolysis but conducted at even higher heating rates, resulting in bio-oil yields of up to 75–80 wt%. The specific heat requirements are the highest among the three types due to the intense energy input required.
-
Practical Implications for Equipment and Consumables:
- Heat Transfer Surfaces: Equipment must be designed with sufficient heat transfer surfaces to meet the energy demands of the pyrolysis process. This is particularly important for fast and flash pyrolysis, where rapid heating is required.
- Material Selection: The corrosive nature of pyrolysis oil and the high temperatures involved necessitate the use of durable, heat-resistant materials for reactors and other equipment.
- Energy Efficiency: Understanding the specific heat of pyrolysis helps in optimizing energy consumption and improving the overall efficiency of the process, which is crucial for large-scale industrial applications.
-
Product Characteristics and Their Impact:
- Pyrolysis oil, one of the main products, has a high oxygen content, making it corrosive, thermally unstable, and prone to polymerization. These properties require specialized handling and storage equipment.
- Char and gases produced during pyrolysis also have specific heat requirements and applications, influencing the design and operation of pyrolysis systems.
By considering these key points, purchasers and engineers can make informed decisions about the equipment and consumables needed for efficient and effective pyrolysis processes.
Summary Table:
Parameter | Details |
---|---|
Specific Heat Range | 207-434 kJ/kg (low temps) to 800-1600 kJ/kg (high temps, e.g., 500°C) |
Process Type | Endothermic (requires external heat input) |
Key Influencing Factors | Temperature, heating rate, residence time, atmosphere, and pressure |
Pyrolysis Types | Slow, Fast, Flash (varying heat requirements and product yields) |
Equipment Needs | Heat transfer surfaces, durable materials, energy-efficient designs |
Ready to optimize your pyrolysis process? Contact our experts today for tailored solutions!