Case hardening is a specialized heat treatment process used to increase the hardness of the outer surface of a metal part while maintaining a softer, more ductile core. This process is particularly useful for components that require high wear resistance on the surface but need to retain toughness and flexibility in the core, such as gears, shafts, and bearings. The step-by-step process of case hardening involves several stages, each critical to achieving the desired properties in the metal.
Key Points Explained:
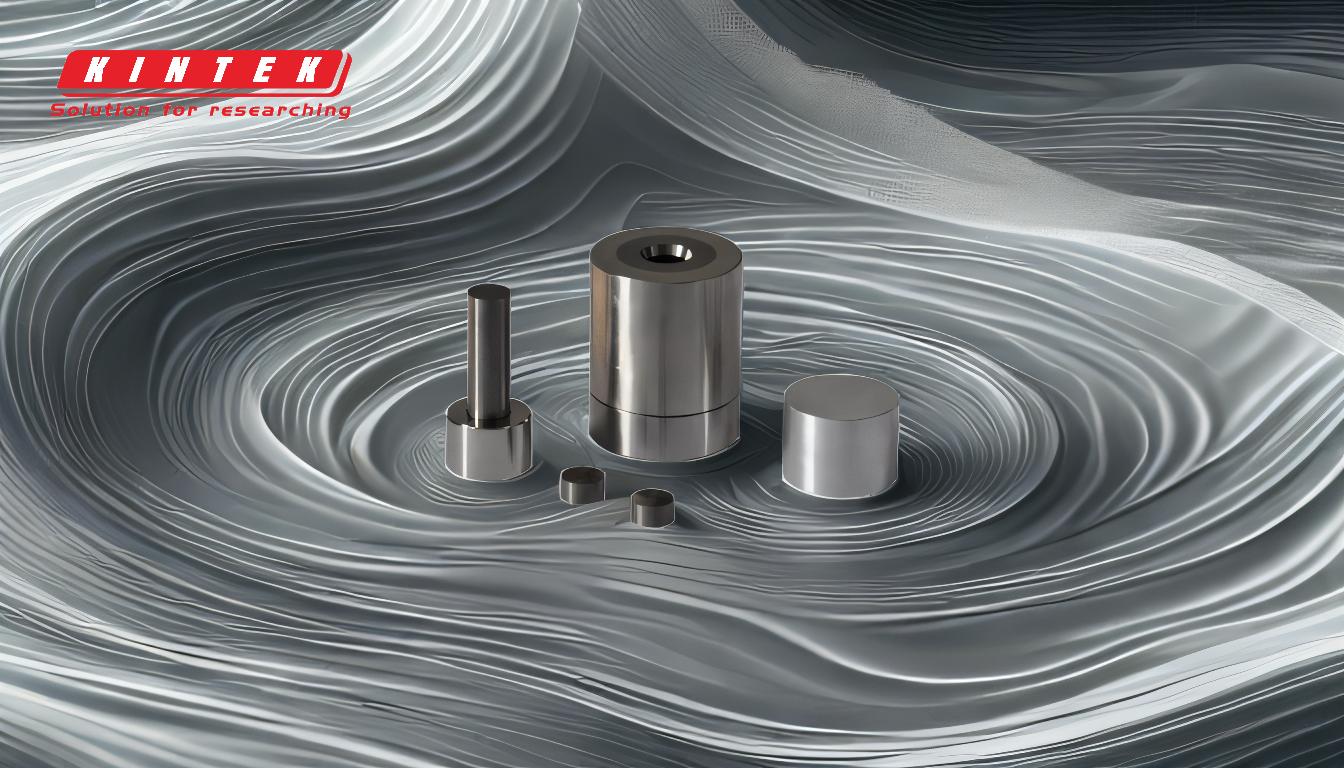
-
Selection of Material:
- The first step in case hardening is selecting the appropriate material. Typically, low-carbon steels or iron alloys are chosen because they can effectively absorb carbon or nitrogen during the hardening process. These materials allow for a significant difference in hardness between the surface and the core.
-
Cleaning and Preparing the Surface:
- Before the actual hardening process begins, the metal part must be thoroughly cleaned to remove any dirt, oil, or oxides. This ensures that the hardening agents (carbon or nitrogen) can penetrate the surface evenly. Surface preparation may involve mechanical cleaning (e.g., sandblasting) or chemical cleaning (e.g., using solvents or acids).
-
Heating the Metal:
- The metal is heated to a specific temperature, typically between 850°C and 950°C (1562°F and 1742°F), depending on the material and the desired hardness. This step is crucial because it allows the metal to reach a state where it can absorb carbon or nitrogen effectively. The heating process is usually carried out in a controlled environment, such as a furnace, to ensure uniform temperature distribution.
-
Introduction of Hardening Agents (Carburizing or Nitriding):
- Once the metal reaches the desired temperature, it is exposed to a carbon-rich or nitrogen-rich environment. This step is known as carburizing or nitriding, respectively.
- Carburizing: In this process, the metal is placed in a carbon-rich atmosphere, such as a gas or liquid containing carbon compounds. The carbon diffuses into the surface of the metal, increasing its carbon content and, consequently, its hardness.
- Nitriding: In this process, the metal is exposed to a nitrogen-rich environment, often in the form of ammonia gas. Nitrogen atoms diffuse into the surface, forming hard nitrides that increase surface hardness.
- Once the metal reaches the desired temperature, it is exposed to a carbon-rich or nitrogen-rich environment. This step is known as carburizing or nitriding, respectively.
-
Soaking:
- After the introduction of hardening agents, the metal is held at the high temperature for a specific period, known as the soaking time. This allows the carbon or nitrogen to diffuse deeper into the metal, creating a hardened case of the desired thickness. The soaking time can vary from a few minutes to several hours, depending on the material and the required case depth.
-
Quenching:
- Once the soaking period is complete, the metal is rapidly cooled, or quenched, to lock in the hardened surface. Quenching is typically done by immersing the metal in a cooling medium such as water, oil, or air. The rapid cooling causes the surface to harden significantly while the core remains relatively soft and ductile.
-
Tempering:
- After quenching, the metal may undergo tempering to reduce brittleness and improve toughness. Tempering involves reheating the metal to a lower temperature (typically between 150°C and 650°C or 302°F and 1202°F) and then allowing it to cool slowly. This step helps to relieve internal stresses and achieve a balance between hardness and toughness.
-
Final Finishing:
- The final step in the case hardening process is finishing the metal part. This may involve grinding, polishing, or coating to achieve the desired surface finish and dimensional accuracy. Finishing also ensures that the part meets the required specifications for its intended application.
By following these steps, case hardening can significantly enhance the durability and wear resistance of metal components while maintaining their structural integrity. This makes it an essential process in industries where high-performance materials are required.
Summary Table:
Step | Description |
---|---|
1. Selection of Material | Choose low-carbon steels or iron alloys for effective carbon/nitrogen absorption. |
2. Cleaning and Preparing | Remove dirt, oil, or oxides to ensure even penetration of hardening agents. |
3. Heating the Metal | Heat to 850°C–950°C (1562°F–1742°F) for optimal carbon/nitrogen absorption. |
4. Hardening Agents | Introduce carbon (carburizing) or nitrogen (nitriding) to increase surface hardness. |
5. Soaking | Hold at high temperature to allow diffusion of hardening agents into the metal. |
6. Quenching | Rapidly cool to lock in the hardened surface while keeping the core ductile. |
7. Tempering | Reheat to reduce brittleness and improve toughness. |
8. Final Finishing | Grind, polish, or coat to achieve desired surface finish and accuracy. |
Need help with case hardening for your metal components? Contact our experts today for tailored solutions!