Brazing is a process that involves joining two or more metal components using a filler metal (brazing alloy) that melts at a temperature above 450°C (842°F) but below the melting point of the base metals being joined. The temperature of brazing alloys varies depending on the specific alloy composition and the materials being joined. Generally, brazing temperatures range from 450°C to 1200°C (842°F to 2192°F). The choice of temperature depends on factors such as the type of base metals, the melting point of the filler metal, and the desired properties of the joint. Understanding the appropriate temperature for brazing is crucial for achieving strong, durable, and reliable joints.
Key Points Explained:
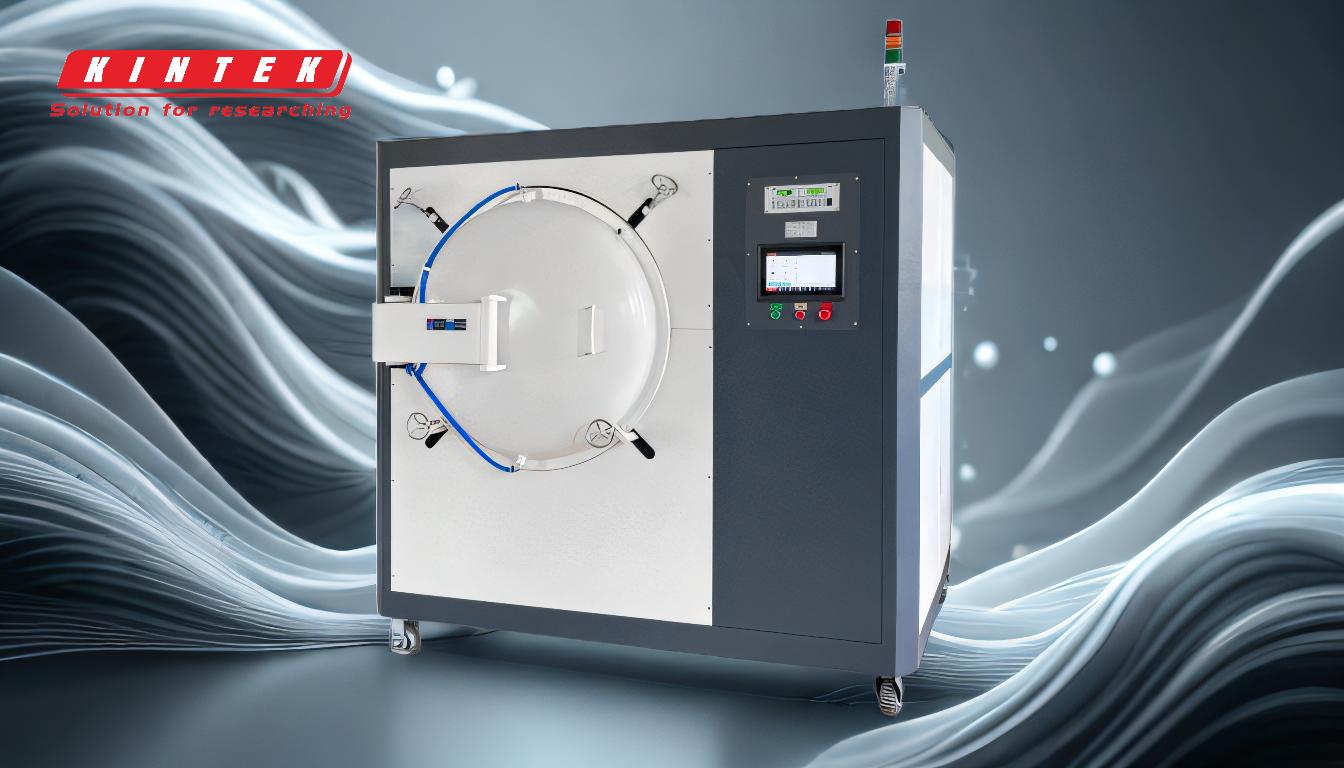
-
Definition of Brazing and Brazing Alloys:
- Brazing is a metal-joining process where a filler metal is heated above its melting point and distributed between two or more close-fitting parts by capillary action.
- Brazing alloys are the filler metals used in this process, and they are specifically chosen based on their melting points, which are lower than those of the base metals being joined.
-
Temperature Range for Brazing Alloys:
- The temperature of brazing alloys typically ranges from 450°C to 1200°C (842°F to 2192°F).
- This range ensures that the filler metal melts and flows into the joint without melting the base metals.
-
Factors Influencing Brazing Temperature:
- Base Metal Properties: The melting point of the base metals being joined plays a significant role in determining the brazing temperature. The filler metal must melt at a temperature lower than the base metals.
- Filler Metal Composition: Different brazing alloys have different melting points. For example, silver-based alloys melt at lower temperatures (around 600°C to 800°C), while nickel-based alloys require higher temperatures (around 1000°C to 1200°C).
- Joint Design and Application: The design of the joint and the specific application can influence the required brazing temperature. For instance, joints with tight clearances may require lower temperatures to ensure proper capillary flow.
-
Common Brazing Alloys and Their Melting Temperatures:
- Silver-Based Alloys: These alloys are commonly used for brazing copper, brass, and stainless steel. They typically melt between 600°C and 800°C (1112°F to 1472°F).
- Copper-Based Alloys: Copper-phosphorus alloys are often used for brazing copper and brass. They melt at around 700°C to 800°C (1292°F to 1472°F).
- Nickel-Based Alloys: These alloys are used for high-temperature applications and can withstand temperatures up to 1200°C (2192°F). They are often used for brazing stainless steel and superalloys.
- Aluminum-Based Alloys: Used for brazing aluminum and its alloys, these filler metals melt at around 580°C to 620°C (1076°F to 1148°F).
-
Importance of Temperature Control in Brazing:
- Precise temperature control is essential in brazing to ensure that the filler metal melts and flows properly without overheating the base metals.
- Overheating can lead to base metal distortion, oxidation, and weakened joints, while insufficient heating can result in incomplete melting and poor joint formation.
-
Brazing Methods and Their Temperature Requirements:
- Torch Brazing: This method uses a gas flame to heat the joint and filler metal. The temperature is controlled by adjusting the flame intensity and the distance between the flame and the joint.
- Furnace Brazing: In this method, the entire assembly is heated in a furnace to the required brazing temperature. This method is suitable for large-scale production and provides uniform heating.
- Induction Brazing: This method uses electromagnetic induction to heat the joint and filler metal. It allows for precise temperature control and is often used for small, intricate parts.
- Dip Brazing: The assembly is immersed in a molten salt bath or a bath of molten filler metal. The temperature is controlled by the bath temperature.
-
Post-Brazing Considerations:
- After brazing, the joint should be allowed to cool slowly to avoid thermal stress and cracking.
- In some cases, post-brazing heat treatment may be required to improve the mechanical properties of the joint.
In summary, the temperature of brazing alloys is a critical factor in the brazing process, and it varies depending on the type of alloy and the materials being joined. Proper temperature control ensures the formation of strong, durable joints, and understanding the specific requirements for each brazing application is essential for achieving optimal results.
Summary Table:
Brazing Alloy Type | Melting Temperature Range | Common Applications |
---|---|---|
Silver-Based Alloys | 600°C to 800°C (1112°F to 1472°F) | Copper, Brass, Stainless Steel |
Copper-Based Alloys | 700°C to 800°C (1292°F to 1472°F) | Copper, Brass |
Nickel-Based Alloys | 1000°C to 1200°C (1832°F to 2192°F) | Stainless Steel, Superalloys |
Aluminum-Based Alloys | 580°C to 620°C (1076°F to 1148°F) | Aluminum and its Alloys |
Need help selecting the right brazing alloy for your project? Contact our experts today for personalized guidance!