The temperature of PVD (Physical Vapor Deposition) plasma typically ranges from 70°C to 450°C (158°F to 842°F), depending on the specific process, substrate material, and application requirements. This relatively low temperature range is a key advantage of PVD, as it minimizes the risk of altering the mechanical properties or dimensions of the substrate. The temperature can be precisely controlled to ensure optimal adhesion and film quality, while also accommodating the thermal sensitivity of various substrates, such as plastics or metals like zinc, brass, and steel. The lower operating temperature of PVD, compared to processes like CVD (Chemical Vapor Deposition), makes it suitable for a wide range of applications where substrate integrity is critical.
Key Points Explained:
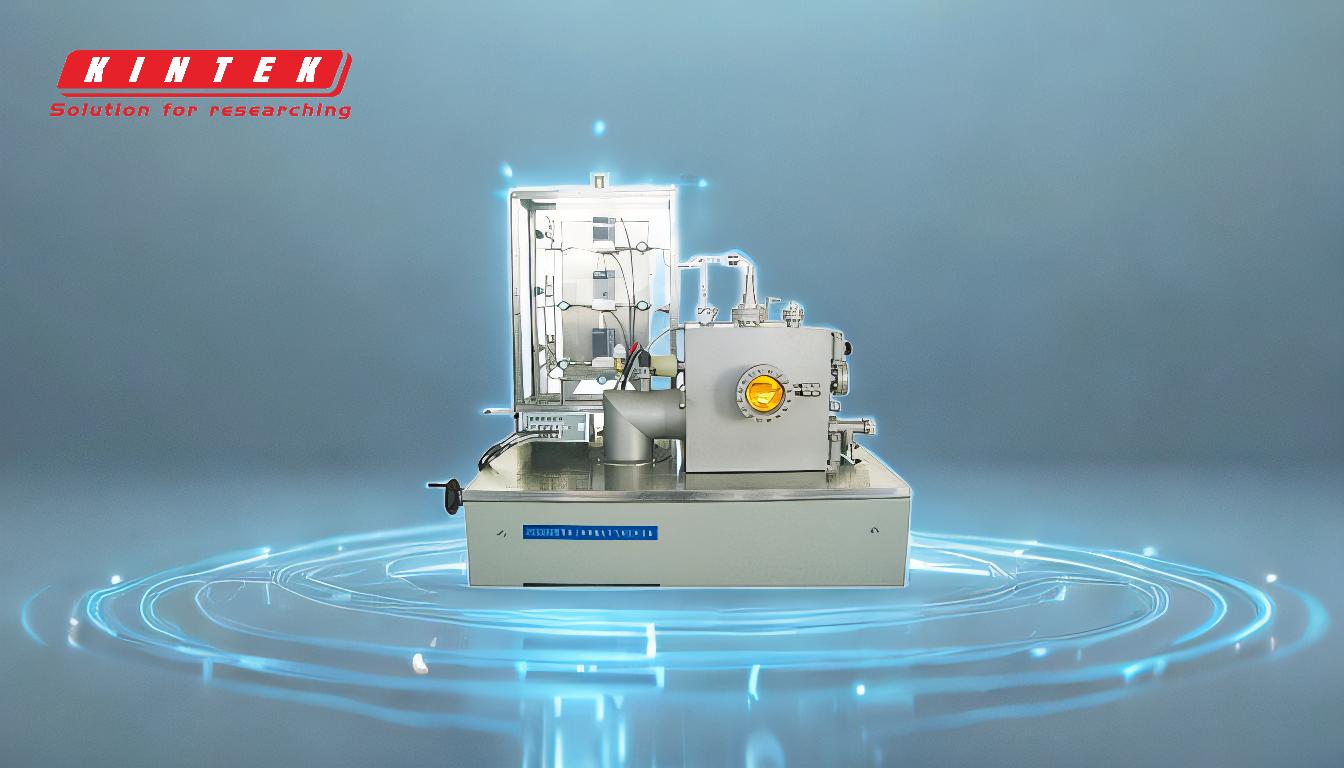
-
Typical Temperature Range of PVD Plasma:
- The temperature of PVD plasma generally ranges from 70°C to 450°C (158°F to 842°F). This range ensures that the substrate remains stable and does not undergo significant thermal deformation or degradation during the deposition process.
- The lower end of the range (70°C to 200°C) is often used for thermally sensitive materials, such as plastics or certain metals, while the higher end (up to 450°C) is suitable for more robust substrates like steel.
-
Substrate-Specific Temperature Control:
- The temperature during PVD can be adjusted based on the substrate material. For example:
- Zinc and Brass: Typically processed at lower temperatures (50°F to 400°F or 10°C to 204°C) to prevent melting or structural changes.
- Steel: Can withstand higher temperatures (up to 400°C or 750°F) without compromising its mechanical properties.
- Plastics: Require even lower temperatures (below 200°C or 392°F) to avoid warping or degradation.
- This adaptability makes PVD suitable for a wide variety of materials and applications.
- The temperature during PVD can be adjusted based on the substrate material. For example:
-
Impact of Temperature on Film Quality:
- The temperature of the substrate during PVD significantly influences the sticking coefficient, which determines how well the deposited material adheres to the substrate.
- Higher temperatures (within the PVD range) can improve film adhesion and crystallinity, but excessive heat may alter the substrate's properties or cause thermal stress.
- Thermal equilibrium on the substrate surface is crucial for achieving uniform film quality and good crystal structure.
-
Comparison with CVD:
- PVD operates at much lower temperatures compared to Chemical Vapor Deposition (CVD), which typically requires temperatures above 900°C (1652°F).
- The lower temperature range of PVD makes it more suitable for applications involving thermally sensitive substrates or where high-temperature processing is impractical.
-
Process Temperature Control:
- PVD systems are designed to maintain precise temperature control, often using advanced cooling and heating mechanisms to ensure consistent deposition conditions.
- The ability to operate at lower temperatures reduces the need for high plasma power, which can further minimize energy consumption and operational costs.
-
Applications and Limitations:
- The relatively low operating temperature of PVD makes it ideal for applications in industries such as electronics, optics, and medical devices, where substrate integrity is critical.
- However, the temperature must be carefully controlled to avoid altering the film's properties or causing defects, such as poor adhesion or uneven thickness.
By maintaining a controlled temperature range, PVD ensures high-quality coatings while preserving the structural and mechanical integrity of the substrate. This balance makes PVD a versatile and widely used deposition technique across various industries.
Summary Table:
Aspect | Details |
---|---|
Typical Temperature Range | 70°C to 450°C (158°F to 842°F) |
Substrate-Specific Control | - Zinc/Brass: 10°C to 204°C - Steel: Up to 400°C - Plastics: Below 200°C |
Impact on Film Quality | - Higher temps improve adhesion - Thermal equilibrium ensures uniformity |
Comparison with CVD | PVD: 70°C to 450°C CVD: Above 900°C |
Applications | Electronics, optics, medical devices, and more |
Learn how PVD plasma can enhance your substrate coatings—contact our experts today!