Magnetron sputtering is a widely used technique in thin-film deposition, where a plasma is generated near a target material to eject atoms that then deposit onto a substrate. The temperature of the sputtering plasma in a magnetron system is a critical parameter, as it influences the efficiency and quality of the deposition process. The plasma temperature is typically measured in terms of electron temperature, which can range from a few electron volts (eV) to tens of eV, depending on the operating conditions. This temperature is relatively low compared to other plasma processes, making magnetron sputtering suitable for temperature-sensitive substrates. The plasma's low temperature is maintained by the magnetic fields that confine and control the plasma, ensuring efficient sputtering without excessive heating.
Key Points Explained:
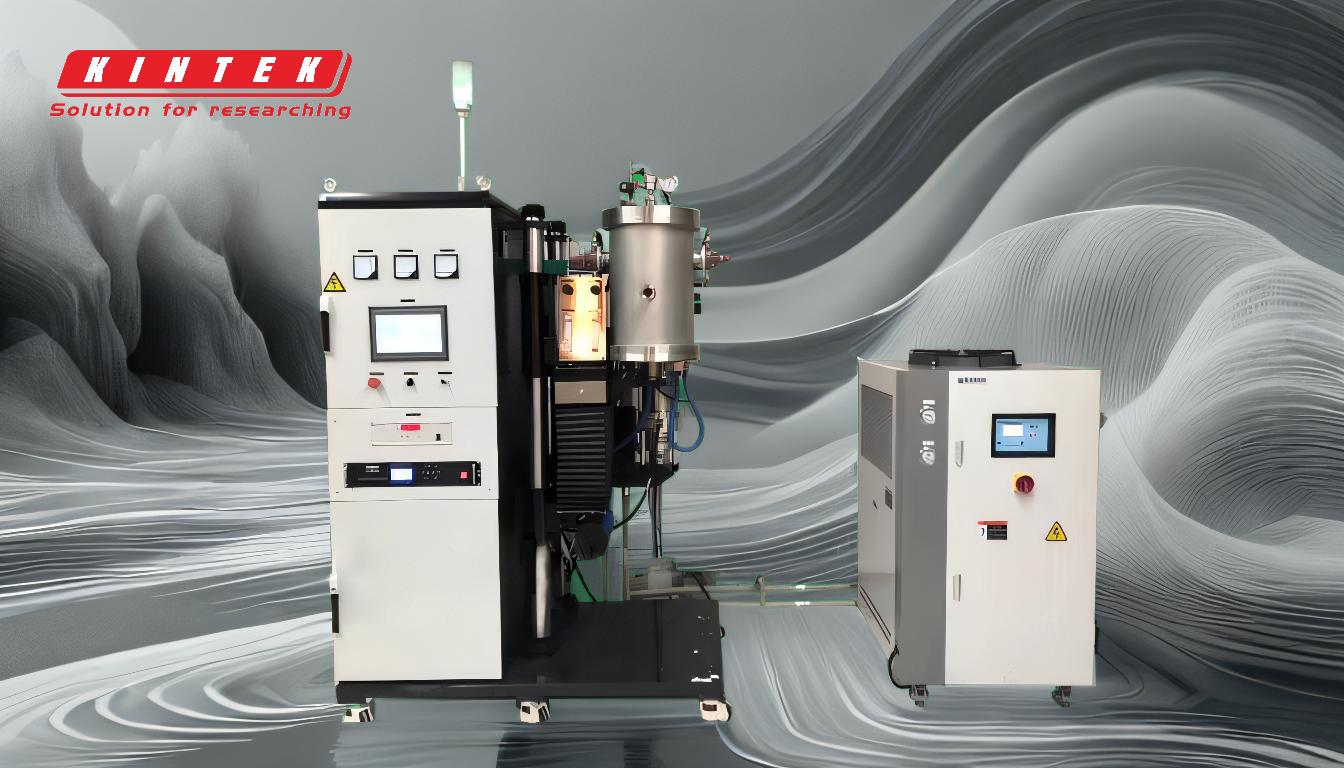
-
Plasma Generation in Magnetron Sputtering:
- In magnetron sputtering, a plasma is created near the target material using an inert gas, typically argon. High voltage is applied to ionize the argon gas, forming a plasma composed of argon ions, free electrons, and neutral atoms.
- The plasma is confined and intensified by magnetic fields generated by magnet arrays within the target. This magnetic confinement increases the density of the plasma near the target surface, enhancing the sputtering process.
-
Temperature of Sputtering Plasma:
- The temperature of the sputtering plasma is primarily characterized by the electron temperature, which typically ranges from 2 to 10 eV. This is relatively low compared to other plasma processes, such as arc discharges, where temperatures can reach hundreds of eV.
- The low temperature is advantageous because it minimizes thermal damage to the substrate and allows for the deposition of high-quality thin films on temperature-sensitive materials.
-
Role of Magnetic Fields in Plasma Temperature Control:
- The magnetic fields in a magnetron sputtering system play a crucial role in controlling the plasma temperature. By confining the plasma near the target surface, the magnetic fields increase the ionization efficiency and sputtering rate without significantly raising the plasma temperature.
- This magnetic confinement also reduces the need for high operating pressures, making the process more efficient and controllable.
-
Plasma Glow and Active Sputtering:
- The visible plasma glow during magnetron sputtering is a result of high-energy particle collisions near the target. This glow indicates that the plasma is active and that atoms are being ejected from the target and deposited onto the substrate.
- The intensity of the glow can provide insights into the plasma density and temperature, with brighter glows typically indicating higher plasma activity.
-
Impact of Plasma Temperature on Thin-Film Properties:
- The relatively low temperature of the sputtering plasma in magnetron systems allows for the deposition of films with uniform and tight patterns. This enhances the material properties of the deposited films, such as durability, corrosion resistance, and specific optical or electrical characteristics.
- The controlled plasma temperature also ensures that the substrate remains undamaged, which is particularly important for applications involving delicate or temperature-sensitive materials.
-
Comparison with Other Deposition Techniques:
- Compared to techniques like electron beam deposition, magnetron sputtering offers better control over plasma temperature and is more suitable for exotic material experimentation and novel coating applications.
- The ability to maintain a low plasma temperature while achieving high sputtering rates makes magnetron sputtering a preferred choice for many industrial and research applications.
In summary, the temperature of the sputtering plasma in a magnetron system is a key factor that influences the efficiency and quality of the thin-film deposition process. The low plasma temperature, controlled by magnetic fields, ensures high-quality film deposition while minimizing thermal damage to the substrate. This makes magnetron sputtering a versatile and effective technique for a wide range of applications.
Summary Table:
Aspect | Details |
---|---|
Plasma Temperature Range | 2 to 10 eV (electron volts) |
Key Advantage | Low temperature minimizes thermal damage to substrates |
Role of Magnetic Fields | Confines plasma, controls temperature, and enhances sputtering efficiency |
Impact on Thin Films | Ensures uniform, durable, and high-quality film deposition |
Comparison with Other Techniques | Better control over plasma temperature than electron beam deposition |
Discover how magnetron sputtering can optimize your thin-film processes—contact our experts today!