Spark Plasma Sintering (SPS) is a modern sintering technique that significantly reduces the time required for sintering compared to conventional methods. The process typically involves holding the material at the sintering temperature for just 5 to 10 minutes, whereas conventional sintering can take hours. This efficiency is achieved through the use of pulsed direct current (DC) that generates high temperatures and plasma between particles, facilitating rapid densification. The process also allows for lower sintering temperatures and results in materials with high density, often exceeding 99%. SPS is versatile, capable of sintering a wide range of materials including metals, ceramics, and composites, and is known for its energy efficiency and environmental benefits.
Key Points Explained:
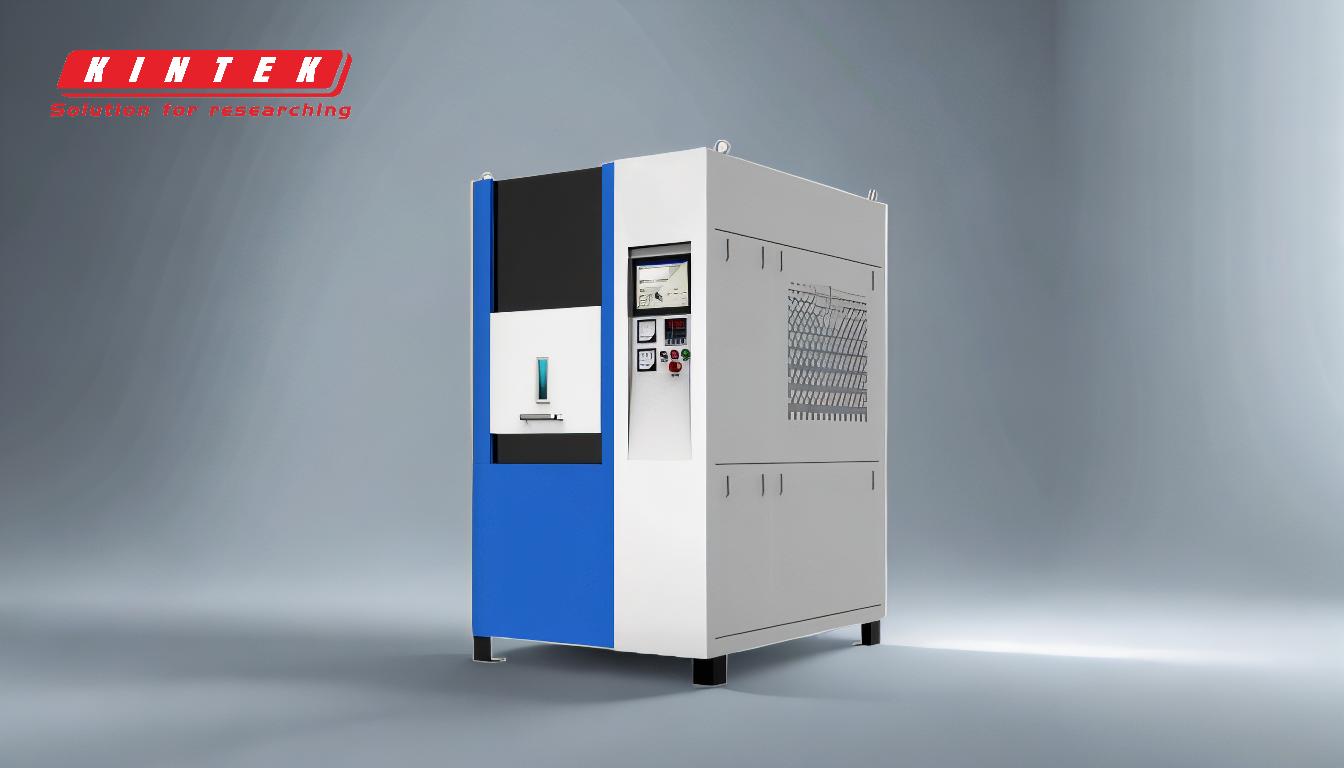
-
Reduced Sintering Time:
- Explanation: SPS drastically reduces the sintering time to just 5 to 10 minutes at the sintering temperature, compared to several hours in conventional sintering methods. This is primarily due to the rapid heating and cooling rates facilitated by the pulsed DC current.
- Implications: This reduction in time not only speeds up the production process but also minimizes the risk of material degradation that can occur during prolonged exposure to high temperatures.
-
Mechanism of Action:
- Explanation: The SPS process utilizes a pulsed DC current that creates a spark plasma between particles, reaching temperatures as high as 10,000°C. This high temperature causes the surface of the particles to melt and fuse together, forming dense structures known as "necks."
- Implications: The formation of these necks is crucial for achieving high-density materials, often exceeding 99% density, which is essential for applications requiring strong and durable materials.
-
Lower Sintering Temperatures:
- Explanation: SPS allows for sintering at temperatures several hundred degrees lower than those required in conventional methods. This is achieved through the combined effects of the electric field and hot pressing.
- Implications: Lower sintering temperatures reduce energy consumption and minimize thermal stress on the materials, leading to better quality and more consistent products.
-
Versatility in Material Processing:
- Explanation: SPS can be used to sinter a wide variety of materials including metals, ceramics, composites, nano-bulk materials, amorphous bulk materials, and gradient materials.
- Implications: This versatility makes SPS a valuable technique in various industries, from aerospace to biomedical engineering, where different material properties are required.
-
Energy Efficiency and Environmental Benefits:
- Explanation: The rapid heating and cooling rates, along with lower sintering temperatures, contribute to the energy efficiency of the SPS process. Additionally, the process is environmentally friendly as it reduces the overall energy consumption and minimizes waste.
- Implications: These benefits make SPS an attractive option for industries looking to reduce their environmental footprint while maintaining high production standards.
-
Controlled Microstructure:
- Explanation: SPS allows for precise control over the microstructure of the sintered material, which is crucial for achieving desired mechanical and physical properties.
- Implications: This control is particularly important in advanced applications where specific material characteristics are required, such as in the development of high-performance ceramics or advanced composites.
In summary, Spark Plasma Sintering offers a rapid, efficient, and versatile method for sintering a wide range of materials. Its ability to achieve high-density materials with controlled microstructures, while operating at lower temperatures and with reduced energy consumption, makes it a highly advantageous technique in modern material science and engineering.
Summary Table:
Key Feature | Description | Implications |
---|---|---|
Reduced Sintering Time | Sintering in 5-10 minutes vs. hours in conventional methods. | Faster production, reduced material degradation. |
Mechanism of Action | Pulsed DC current creates plasma, melting particle surfaces to form dense necks. | Achieves >99% density for strong, durable materials. |
Lower Sintering Temperatures | Operates at temperatures hundreds of degrees lower than conventional methods. | Reduces energy use, minimizes thermal stress, and improves product consistency. |
Versatility | Sinters metals, ceramics, composites, and more. | Ideal for aerospace, biomedical, and advanced material applications. |
Energy Efficiency | Rapid heating/cooling and lower temperatures reduce energy consumption. | Environmentally friendly with minimal waste. |
Controlled Microstructure | Precise control over material microstructure. | Enables tailored mechanical and physical properties for advanced applications. |
Ready to transform your material processing? Contact us today to learn how SPS can benefit your projects!