The two-step sintering (TSS) method is an advanced sintering technique used to produce fine-grained ceramic materials with high densification and excellent mechanical properties. Unlike traditional sintering, which involves a single heating cycle, TSS employs two distinct temperature stages to control grain growth while achieving full densification. This method is particularly effective for ceramics, including structural ceramics, bioceramics, ferrites, piezoelectric ceramics, and electrolyte ceramics. TSS allows for the production of materials with uniform grain size distribution, enhanced high-temperature strength, and improved mechanical properties, such as Vickers hardness, while maintaining cost-effectiveness and energy efficiency.
Key Points Explained:
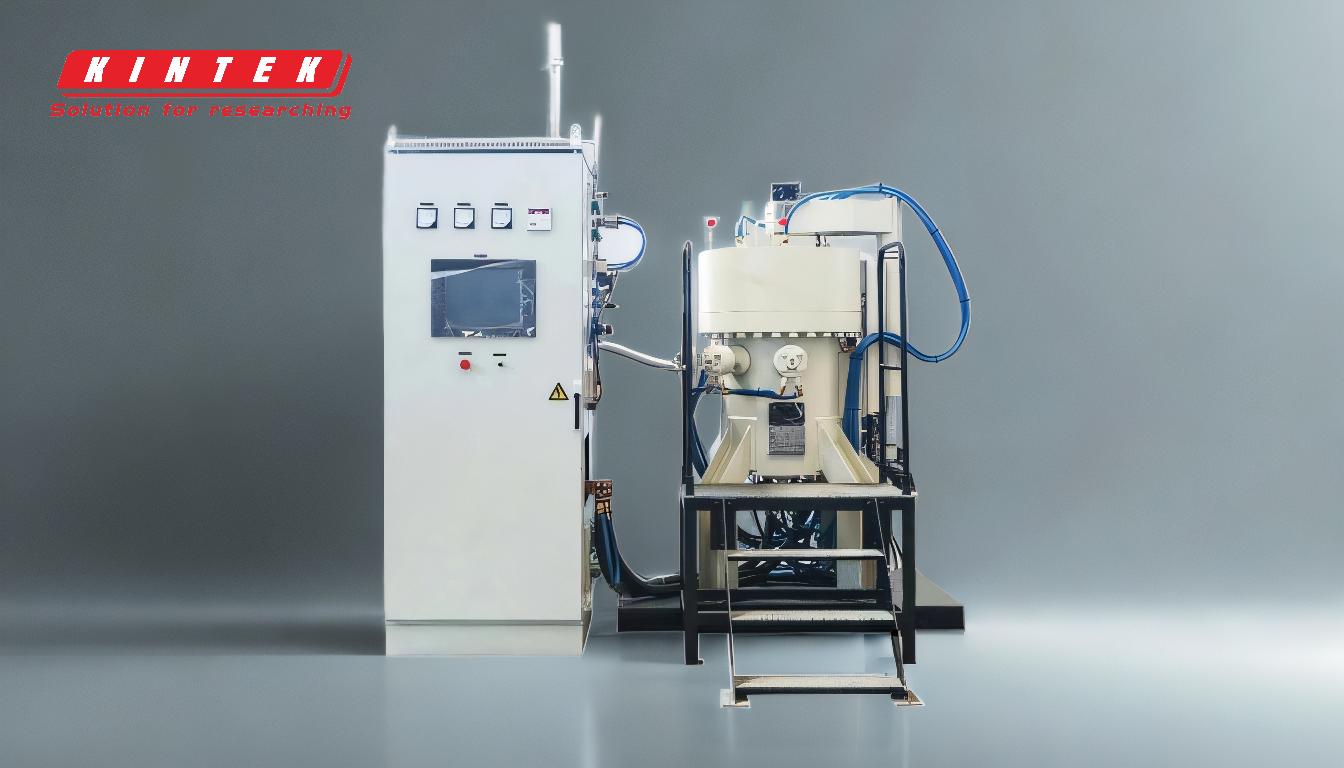
-
Definition and Process of Two-Step Sintering:
- Two-step sintering (TSS) is a sintering method that involves two distinct temperature stages. The first stage involves heating the material to a higher temperature to initiate densification, while the second stage involves holding the material at a lower temperature to complete densification without allowing excessive grain growth.
- This process contrasts with traditional sintering, which typically involves a single heating cycle. TSS is designed to achieve high densification while minimizing grain growth, resulting in fine-grained microstructures.
-
Applications of Two-Step Sintering:
- TSS is widely used in the production of various ceramics, including:
- Structural ceramics: For high-strength and wear-resistant applications.
- Bioceramics: For medical implants and prosthetics.
- Ferrites: For magnetic applications.
- Piezoelectric ceramics: For sensors and actuators.
- Electrolyte ceramics: For fuel cells and batteries.
- The method is versatile and can be applied to a wide range of ceramic materials, making it a valuable technique in materials science and engineering.
- TSS is widely used in the production of various ceramics, including:
-
Advantages of Two-Step Sintering:
- Fine-Grained Microstructure: TSS allows for the production of ceramics with uniform and fine grain sizes, which are critical for achieving high mechanical strength and durability.
- High Densification: The two-stage process ensures that the material reaches near-theoretical density, resulting in improved mechanical and electrical properties.
- Cost-Effectiveness: TSS can achieve similar or better results compared to traditional sintering methods, but at lower temperatures and with reduced energy consumption.
- Improved High-Temperature Strength: The presence of a glass phase and uniform grain size distribution in the grain gaps enhances the material's high-temperature bending strength, delaying the decline of strength under high-temperature conditions.
-
Comparison with Traditional Sintering:
- Traditional sintering often involves a single heating cycle, which can lead to excessive grain growth and reduced mechanical properties.
- In contrast, TSS controls grain growth by separating the densification process into two stages, resulting in finer grains and better overall material properties.
- For example, silicon nitride samples prepared using TSS have similar grain size, phase composition, and Vickers hardness (HV 1478) as samples sintered at 1800°C for 8 hours, but with potentially lower energy consumption and cost.
-
Mechanical Properties and Performance:
- The fine-grained microstructure achieved through TSS leads to improved mechanical properties, such as higher Vickers hardness and enhanced high-temperature strength.
- The uniform grain size distribution and the presence of a glass phase in the grain gaps contribute to the material's ability to maintain strength under high-temperature conditions.
- These properties make TSS-produced ceramics suitable for demanding applications, such as turbine blades, where high strength and durability are essential.
-
Energy Efficiency and Cost Considerations:
- TSS is more energy-efficient than traditional sintering methods because it operates at lower temperatures during the second stage, reducing overall energy consumption.
- The method also allows for better control of the densification process, leading to higher-quality materials with fewer defects.
- These factors contribute to the cost-effectiveness of TSS, making it an attractive option for large-scale production of high-performance ceramics.
-
Comparison with Other Sintering Techniques:
- Hot Pressing Sintering: While hot pressing sintering also produces high-density materials with fine grain structures, it requires specialized equipment and higher pressures. TSS, on the other hand, achieves similar results with simpler equipment and lower pressure requirements.
- High-Temperature Sintering: High-temperature sintering can significantly improve material properties, but it is more costly due to the need for specialized furnaces. TSS offers a more cost-effective alternative while still achieving excellent material properties.
-
Future Prospects and Research Directions:
- Ongoing research is focused on optimizing the TSS process for different types of ceramics and exploring its potential for new applications.
- Advances in process control and automation, such as the use of IT technology, are expected to further enhance the efficiency and reproducibility of TSS.
- The development of new ceramic materials and composites using TSS could lead to breakthroughs in fields such as energy storage, electronics, and biomedical engineering.
In summary, the two-step sintering method is a highly effective technique for producing fine-grained ceramics with high densification and excellent mechanical properties. Its ability to control grain growth, reduce energy consumption, and lower production costs makes it a valuable tool in the field of materials science. As research and technology continue to advance, TSS is likely to play an increasingly important role in the development of next-generation ceramic materials.
Summary Table:
Aspect | Details |
---|---|
Process | Two distinct temperature stages: high temp for densification, low temp for grain control. |
Applications | Structural ceramics, bioceramics, ferrites, piezoelectric ceramics, electrolyte ceramics. |
Advantages | Fine-grained microstructure, high densification, cost-effectiveness, improved high-temperature strength. |
Comparison with Traditional Sintering | Controls grain growth, finer grains, lower energy consumption. |
Mechanical Properties | High Vickers hardness, uniform grain size, enhanced high-temperature strength. |
Energy Efficiency | Lower temperatures in the second stage reduce energy consumption. |
Future Prospects | Optimizing TSS for new materials, advancements in process control, and automation. |
Learn how the two-step sintering method can revolutionize your ceramic production—contact our experts today!