A calciner is a specialized furnace used in industrial processes to heat materials to high temperatures, typically below their melting points, to induce chemical or physical changes. This process, known as calcination, is essential in various industries for purposes such as removing water or volatile substances, decomposing materials, or oxidizing substances. Calcination is widely used in the production of inorganic materials like cement, lime, and ceramics, as well as in the synthesis of zeolites and the treatment of minerals. The calciner's ability to achieve precise temperature control and uniform heating makes it a critical tool in material processing and manufacturing.
Key Points Explained:
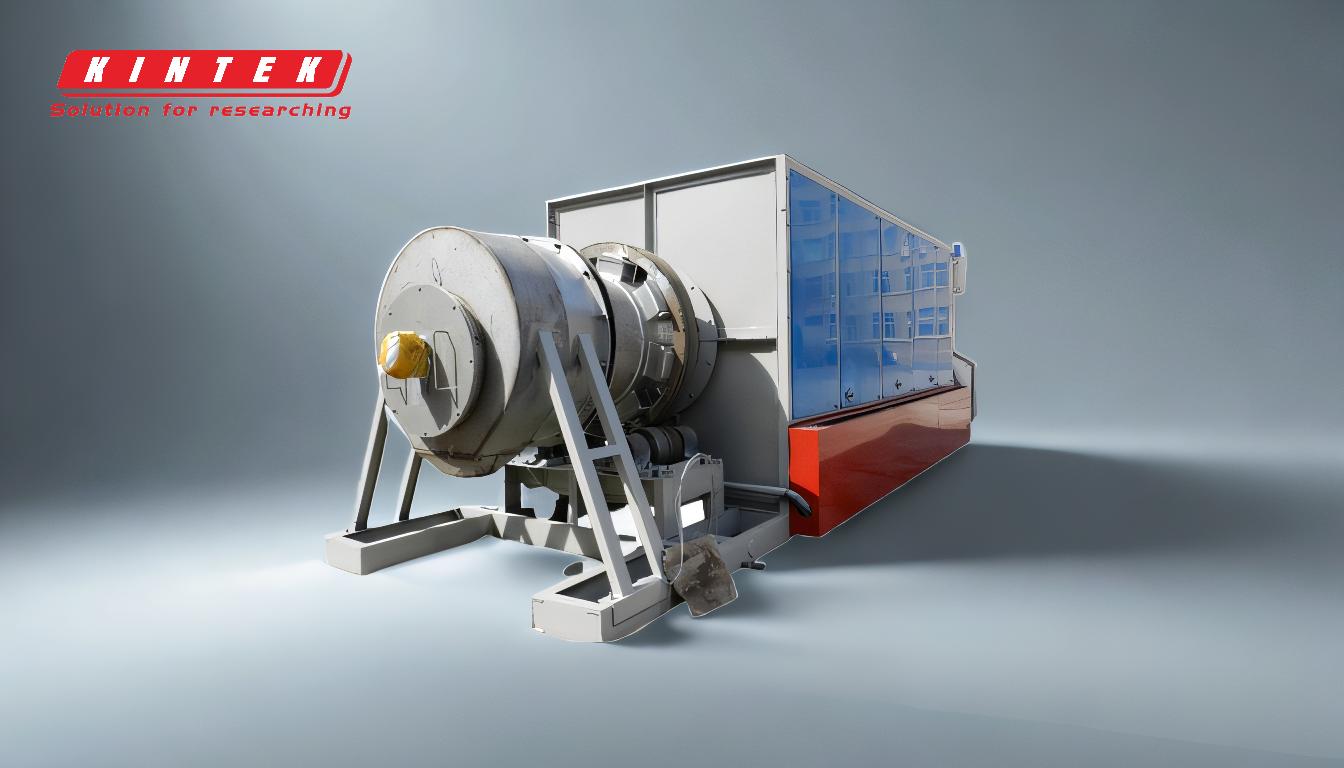
-
Definition and Purpose of Calcination:
- Calcination is a thermal treatment process that involves heating materials to high temperatures (typically below their melting points) to induce chemical or physical changes.
- The primary purposes of calcination include:
- Removing water or moisture from materials (e.g., dehydration of borax).
- Eliminating volatile components like carbon dioxide (CO₂) or sulfur dioxide (SO₂).
- Breaking down compounds into simpler substances (e.g., dissociation of calcium carbonate into calcium oxide and CO₂).
- Oxidizing materials to alter their chemical composition.
-
Applications of Calciners:
-
Production of Inorganic Materials:
- Calciners are widely used in the production of cement, lime, and ceramics. For example, limestone (CaCO₃) is calcined to produce lime (CaO), a key ingredient in cement.
-
Mineral Processing:
- In the mining industry, calciners are used to process ores and minerals, such as magnesite and dolomite, to remove impurities or alter their chemical structure.
-
Synthesis of Zeolites:
- Calciners play a role in the synthesis of zeolites, where they are used to remove ammonium ions and stabilize the material's structure.
-
Glass Manufacturing:
- In the glass industry, calcination is used to induce phase transformations in glass materials, a process known as devitrification.
-
Production of Inorganic Materials:
-
Types of Materials Processed in Calciners:
-
Limestone and Dolomite:
- These materials are calcined to produce lime and magnesia, respectively, which are essential in construction and industrial applications.
-
Borax:
- Calcination removes bound moisture from borax, making it suitable for use in detergents and glass production.
-
Gypsum:
- Calcination of gypsum produces plaster of Paris, used in construction and art.
-
Limestone and Dolomite:
-
Advantages of Using Calciners:
-
Uniform Heating:
- Calciners, especially rotary kilns, provide uniform heating, ensuring consistent product quality.
-
Efficiency:
- They are designed to handle large volumes of materials, making them efficient for industrial-scale operations.
-
Versatility:
- Calciners can process a wide range of materials, from fine powders to larger particles (up to 60 mm in size).
-
Uniform Heating:
-
Equipment Used for Calcination:
-
Rotary Kilns:
- Rotary kilns are the most common type of calciner, preferred for their ability to handle materials with particle sizes of 60 mm or less. They ensure uniform heating and high throughput.
-
Static Calciners:
- These are used for smaller-scale operations or when precise temperature control is required.
-
Rotary Kilns:
-
Industrial Significance:
- Calciners are indispensable in industries such as construction, mining, chemicals, and glass manufacturing. They enable the production of high-quality materials with specific properties, contributing to the efficiency and sustainability of industrial processes.
-
Environmental Considerations:
- The calcination process often releases gases like CO₂, which can have environmental implications. Modern calciners are designed with emission control systems to minimize their environmental impact.
By understanding the role of calciners and their applications, industries can optimize material processing, improve product quality, and reduce waste, making calcination a cornerstone of modern manufacturing and material science.
Summary Table:
Key Aspect | Details |
---|---|
Definition | A specialized furnace for heating materials below melting points. |
Primary Uses | Removing water, decomposing materials, oxidizing substances. |
Applications | Cement, lime, ceramics, zeolite synthesis, mineral processing. |
Materials Processed | Limestone, dolomite, borax, gypsum. |
Advantages | Uniform heating, high efficiency, versatility. |
Equipment Types | Rotary kilns (most common), static calciners. |
Environmental Impact | CO₂ emissions mitigated by modern emission control systems. |
Discover how calciners can optimize your industrial processes—contact us today for expert guidance!