Vacuum thermal evaporation deposition is a widely used technique in thin-film fabrication, where a solid material is heated in a high vacuum environment until it evaporates. The resulting vapor stream then travels through the vacuum chamber and deposits onto a substrate, forming a thin, uniform coating. This process relies on thermal energy to break atomic bonds in the material, creating a vapor cloud that adheres to the substrate due to molecular potential differences. It is a type of Physical Vapor Deposition (PVD) and is valued for its reliability and consistency in producing high-quality thin films.
Key Points Explained:
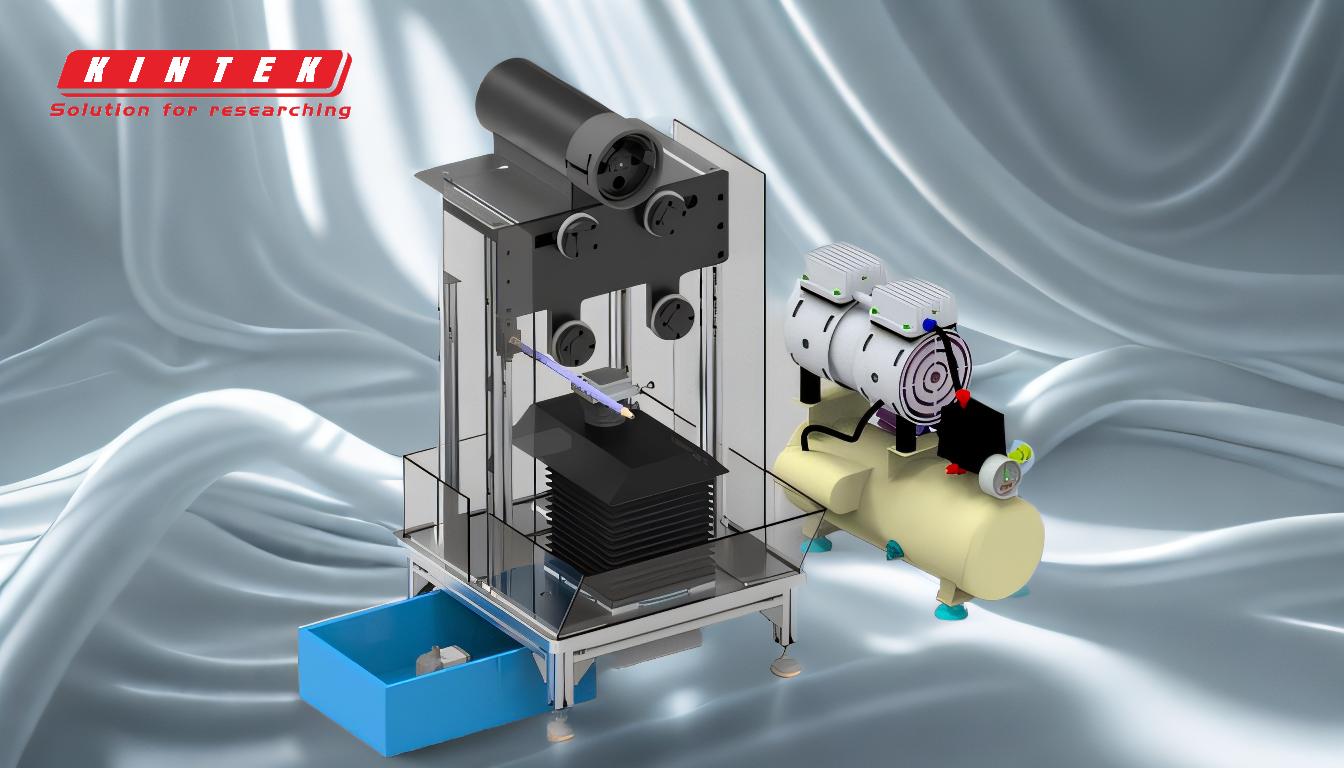
-
Definition and Purpose of Vacuum Thermal Evaporation Deposition:
- Vacuum thermal evaporation deposition is a Physical Vapor Deposition (PVD) technique used to create thin films on substrates.
- It involves heating a solid material in a high vacuum chamber until it evaporates, forming a vapor stream that deposits onto the substrate.
-
The Role of Vacuum in the Process:
- The vacuum environment is crucial because it minimizes interactions between vaporized particles and air molecules, ensuring a clean and efficient deposition process.
- A high vacuum reduces the pressure, allowing even low vapor pressures to create a sufficient vapor cloud for deposition.
-
Heating Mechanism:
- The material is heated using a filament, boat, or basket, often through resistive heating with high electric currents.
- The temperature must reach the material's melting point or beyond to produce sufficient vapor pressure for evaporation.
-
Vaporization and Deposition:
- When the material is heated, thermal energy breaks the atomic bonds, freeing individual atoms or molecules from the solid matrix.
- These vaporized particles form a vapor stream that travels through the vacuum chamber and adheres to the substrate.
-
Substrate Coating:
- The vapor stream condenses on the substrate, forming a thin, uniform film.
- The adhesion of the film is driven by molecular potential differences between the vaporized material and the substrate.
-
Advantages of the Technique:
- High Purity: The vacuum environment prevents contamination, ensuring high-quality thin films.
- Uniformity: The process produces consistent and reliable coatings.
- Versatility: It can be used with a wide range of materials, including metals, semiconductors, and dielectrics.
-
Applications:
- Used in the fabrication of optical coatings, semiconductor devices, and solar cells.
- Commonly employed in the production of thin-film transistors, sensors, and protective coatings.
-
Comparison with Other PVD Techniques:
- Unlike sputtering or pulsed laser deposition, thermal evaporation relies solely on thermal energy for vaporization.
- It is simpler and more cost-effective for many applications but may have limitations with materials requiring extremely high melting points.
-
Key Considerations for Equipment and Consumables:
- Vacuum Chamber: Must maintain a high vacuum level to ensure efficient vaporization and deposition.
- Heating Elements: Filaments, boats, or baskets must withstand high temperatures and be compatible with the material being evaporated.
- Substrate Holders: Should allow for uniform exposure to the vapor stream.
- Material Purity: High-purity source materials are essential to avoid contamination and ensure film quality.
-
Challenges and Limitations:
- Material Limitations: Some materials may decompose or require excessively high temperatures for evaporation.
- Thickness Control: Achieving precise film thickness can be challenging without advanced monitoring systems.
- Scalability: While effective for small-scale applications, scaling up for large-area coatings may require significant equipment modifications.
By understanding these key points, equipment and consumable purchasers can make informed decisions about the components and materials needed for vacuum thermal evaporation deposition systems, ensuring optimal performance and high-quality thin-film production.
Summary Table:
Aspect | Details |
---|---|
Definition | A PVD technique for creating thin films by heating materials in a vacuum. |
Key Role of Vacuum | Minimizes interactions, ensures clean deposition, and supports vaporization. |
Heating Mechanism | Uses filaments, boats, or baskets with resistive heating. |
Advantages | High purity, uniformity, and versatility for various materials. |
Applications | Optical coatings, semiconductors, solar cells, and protective coatings. |
Challenges | Material limitations, thickness control, and scalability issues. |
Ready to enhance your thin-film fabrication process? Contact our experts today for tailored solutions!