Vacuum vapor deposition is a technique used to create thin films by depositing materials onto a substrate in a vacuum environment. This method falls under the broader category of Physical Vapor Deposition (PVD), which involves the condensation of evaporated or sputtered materials from a source onto a substrate. The process typically includes creating a vacuum to remove interfering gases, preparing the substrate, evaporating or sputtering the coating material, depositing it onto the substrate, and cooling the chamber. Vacuum vapor deposition is valued for producing thin films with strong adhesion and is suitable for materials with high melting points. It is widely used in industries such as electronics, optics, and coatings.
Key Points Explained:
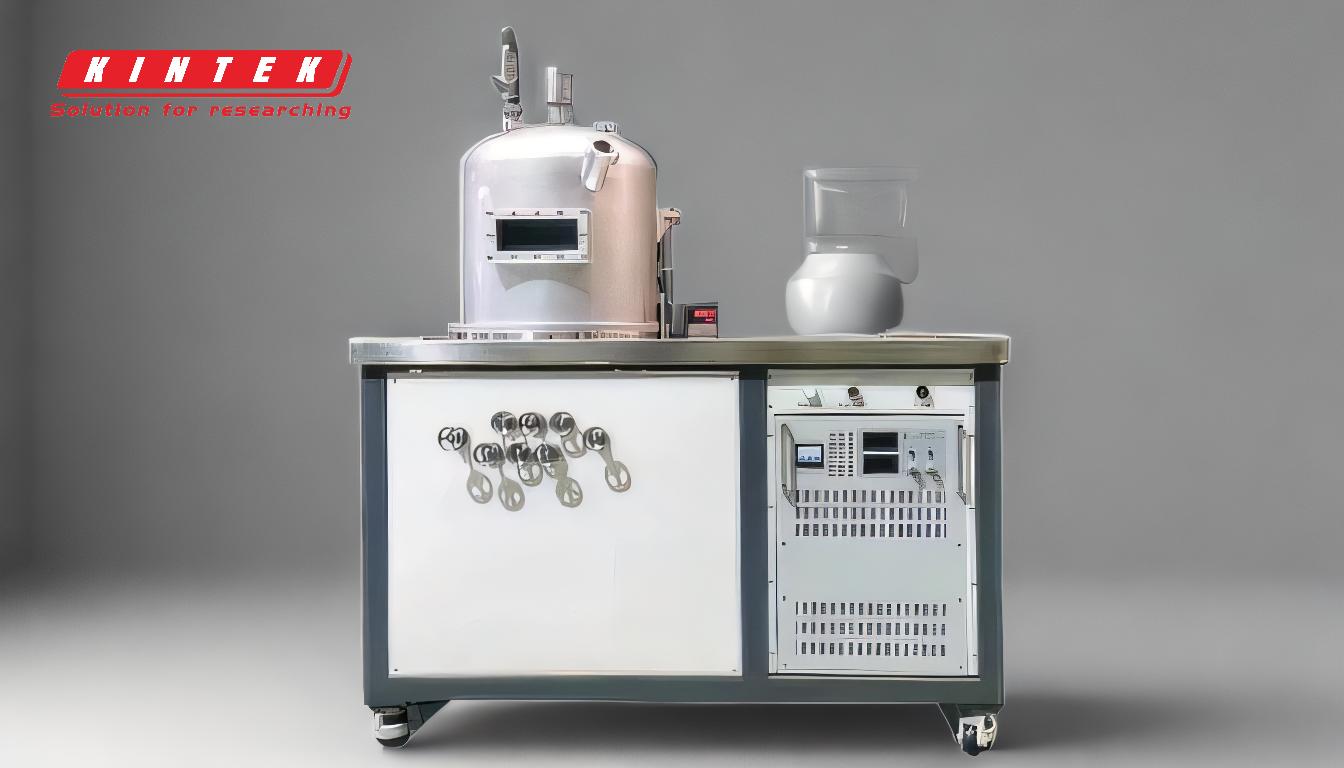
-
Definition and Overview of Vacuum Vapor Deposition:
- Vacuum vapor deposition is a subset of Physical Vapor Deposition (PVD), where materials are deposited onto a substrate in a vacuum environment.
- The process involves evaporating or sputtering a source material, which then condenses onto the substrate to form a thin film.
- This method is distinct from Chemical Vapor Deposition (CVD), which relies on chemical reactions to produce the vapor phase.
-
Key Steps in the Vacuum Vapor Deposition Process:
- Creating a Vacuum: The chamber is evacuated to remove air and gases that could interfere with the deposition process. This ensures a clean environment for high-quality film formation.
- Substrate Preparation: The substrate is cleaned or treated to ensure proper adhesion of the deposited material. This step is critical for achieving uniform and durable coatings.
- Evaporation or Sputtering: The coating material is either heated to produce vapor (evaporation) or knocked off a target material using ions (sputtering).
- Deposition: The vaporized or sputtered material condenses onto the substrate, forming a thin film.
- Cooling and Venting: After deposition, the chamber is cooled, and the vacuum is released to allow removal of the coated substrate.
-
Advantages of Vacuum Vapor Deposition:
- Strong Adhesion: The films produced have excellent adhesion to the substrate, making them durable and long-lasting.
- High Melting Point Materials: This method can handle materials with high melting points, which are difficult to process using other techniques.
- Precision and Uniformity: The vacuum environment allows for precise control over the deposition process, resulting in uniform and high-quality films.
-
Applications of Vacuum Vapor Deposition:
- Electronics: Used for depositing conductive and insulating layers in semiconductor devices.
- Optics: Applied in the production of anti-reflective coatings, mirrors, and optical filters.
- Coatings: Utilized for wear-resistant and decorative coatings on tools, jewelry, and other products.
-
Comparison with Other Vapor Deposition Methods:
- Physical Vapor Deposition (PVD): Includes vacuum vapor deposition, spraying, and evaporation. PVD is generally simpler and more cost-effective than CVD.
- Chemical Vapor Deposition (CVD): Involves chemical reactions to produce the vapor phase. CVD can produce more complex films but often requires higher temperatures and more complex equipment.
-
Sub-Methods of Physical Vapor Deposition:
- Spraying: Involves removing surface atoms from a target and depositing them on the substrate. This method is less common in vacuum vapor deposition but is used in other PVD techniques.
- Evaporation: The most common method in vacuum vapor deposition, where the material is heated to produce vapor, which then condenses on the substrate.
-
Technical Considerations:
- Vacuum Level: The degree of vacuum required depends on the material and the desired film properties. Higher vacuums are needed for materials that are highly reactive or require very clean environments.
- Substrate Temperature: The temperature of the substrate can affect the adhesion and quality of the deposited film. Some materials require heated substrates to achieve optimal results.
- Deposition Rate: The rate at which material is deposited can influence the film's microstructure and properties. Controlled deposition rates are essential for achieving the desired film characteristics.
By understanding these key points, a purchaser of equipment or consumables can make informed decisions about the suitability of vacuum vapor deposition for their specific applications, ensuring they select the right method and materials for their needs.
Summary Table:
Aspect | Details |
---|---|
Process | Evaporation or sputtering of materials in a vacuum environment. |
Key Steps | 1. Create vacuum 2. Prepare substrate 3. Evaporate/sputter 4. Deposit 5. Cool |
Advantages | Strong adhesion, handles high melting points, precise and uniform films. |
Applications | Electronics, optics, wear-resistant and decorative coatings. |
Comparison with CVD | Simpler, cost-effective, no chemical reactions required. |
Discover how vacuum vapor deposition can elevate your projects—contact our experts today for tailored solutions!