The working capacity of a ball mill is influenced by several factors, including the drum diameter, the ratio of drum diameter to length, physical-chemical properties of the feed material, ball filling and sizes, armor surface shape, rotation speed, milling fineness, and timely removal of ground product. Additionally, the grinding performance is affected by the speed of rotation, the size and type of grinding medium, the size and type of material to be ground, and the filling ratio of the mill. The degree of milling is also influenced by the residence time of material in the mill chamber, the size, density, and number of balls, the hardness of the grinding material, the feed rate and level in the vessel, and the rotation speed of the cylinder. Understanding these factors is crucial for optimizing the working capacity of a ball mill.
Key Points Explained:
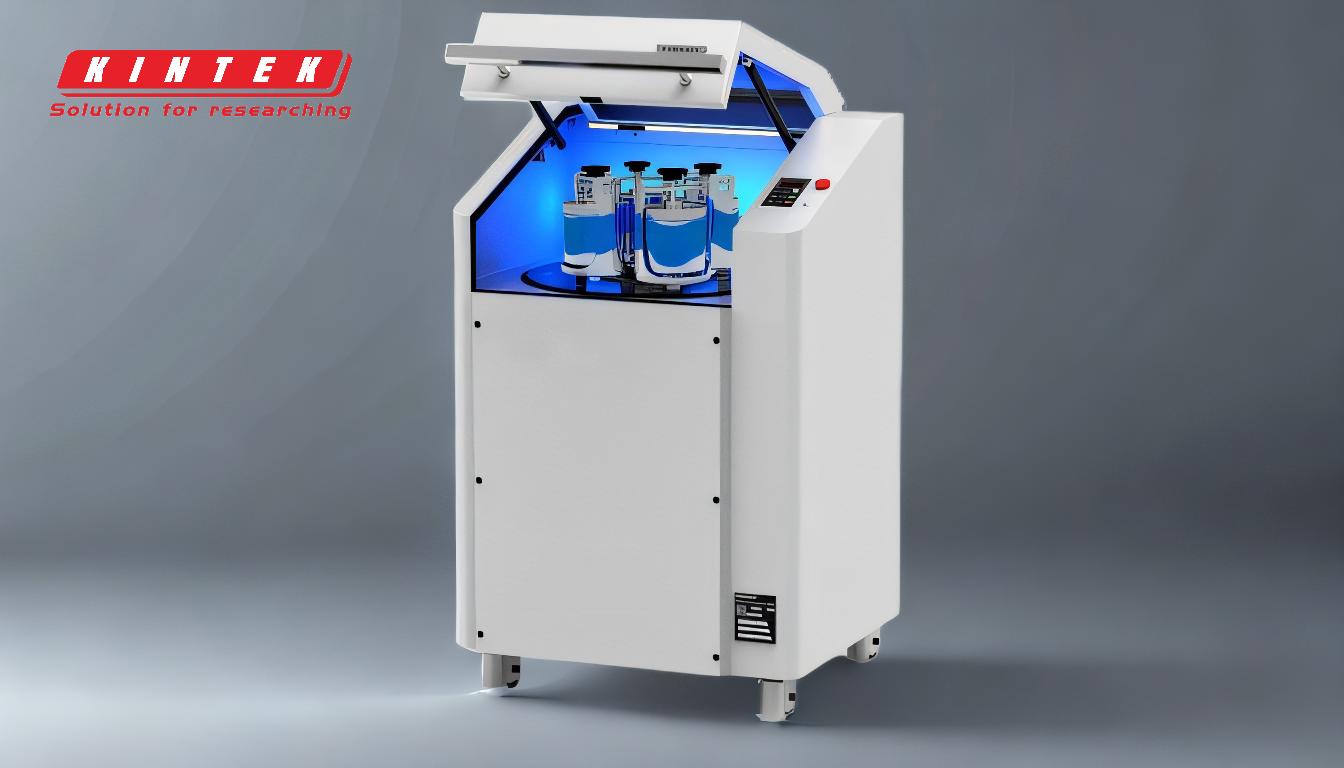
-
Drum Diameter and Length Ratio:
- The productivity of ball mills is significantly affected by the drum diameter and the ratio of drum diameter to length (L:D ratio). The optimal L:D ratio is typically between 1.56 and 1.64. This ratio ensures efficient grinding by providing the right balance between the surface area and the volume of the mill, which affects the grinding efficiency and the residence time of the material inside the mill.
-
Physical-Chemical Properties of Feed Material:
- The nature of the feed material, including its hardness, density, and chemical composition, plays a crucial role in determining the working capacity of the ball mill. Harder materials require more energy to grind, which can reduce the overall efficiency of the mill. Additionally, the chemical properties of the material can affect the wear and tear on the grinding media and the mill lining.
-
Ball Filling and Sizes:
- The amount and size of the grinding balls used in the mill are critical factors. The filling ratio, which is the percentage of the mill volume filled with grinding medium, affects the grinding efficiency. An optimal filling ratio ensures that there is enough contact between the balls and the material to be ground, without causing excessive wear or energy consumption. The size of the balls also matters; larger balls are more effective for coarse grinding, while smaller balls are better for fine grinding.
-
Armor Surface Shape:
- The shape and condition of the mill's internal lining (armor surface) can influence the grinding process. A smooth surface may reduce the grinding efficiency, while a more textured surface can enhance the grinding action by increasing the friction between the balls and the material. The design of the armor surface can also affect the movement of the balls and the material within the mill.
-
Rotation Speed:
- The speed at which the mill rotates is a critical factor in determining its working capacity. The rotation speed affects the centrifugal force acting on the grinding balls, which in turn influences the grinding action. If the speed is too low, the balls may not be lifted high enough to create effective impact and grinding. Conversely, if the speed is too high, the balls may be pinned to the mill wall, reducing the grinding efficiency. The optimal rotation speed is typically around 65-75% of the critical speed, where the critical speed is the speed at which the balls begin to centrifuge.
-
Milling Fineness and Timely Removal of Ground Product:
- The desired fineness of the ground product and the efficiency of removing the ground material from the mill also affect the working capacity. If the material is not removed promptly, it can lead to over-grinding, which consumes more energy and reduces the overall efficiency of the mill. The fineness of the grind is influenced by the residence time of the material in the mill, which is the time the material spends inside the mill chamber before being discharged.
-
Residence Time and Feed Rate:
- The residence time of the material in the mill chamber is influenced by the feed rate and the level of material in the vessel. A higher feed rate can reduce the residence time, leading to coarser grinding, while a lower feed rate increases the residence time, resulting in finer grinding. The level of material in the vessel also affects the grinding efficiency; an optimal level ensures that the material is evenly distributed and properly ground.
-
Size, Density, and Number of Balls:
- The size, density, and number of grinding balls used in the mill are important factors that influence the grinding performance. Larger and denser balls are more effective for grinding harder materials, while smaller and less dense balls are better for softer materials. The number of balls also affects the grinding efficiency; too few balls may not provide enough grinding action, while too many balls can lead to excessive energy consumption and wear.
-
Nature of the Grinding Material:
- The nature of the material being ground, including its hardness, abrasiveness, and moisture content, can significantly affect the grinding performance. Harder and more abrasive materials require more energy to grind and can cause more wear on the grinding media and mill lining. Moisture content can also affect the grinding efficiency, as wet materials may stick to the balls and mill lining, reducing the grinding action.
-
Rotation Speed of the Cylinder:
- The rotation speed of the mill cylinder is a key factor in determining the grinding efficiency. The speed affects the movement of the grinding balls and the material within the mill. An optimal rotation speed ensures that the balls are lifted to the right height and then cascade down, creating effective impact and grinding. The rotation speed should be adjusted based on the size and type of material being ground, as well as the desired fineness of the product.
By carefully considering and optimizing these factors, the working capacity of a ball mill can be maximized, leading to more efficient and effective grinding operations.
Summary Table:
Factor | Impact on Ball Mill Performance |
---|---|
Drum Diameter and Length Ratio | Optimal L:D ratio (1.56-1.64) ensures efficient grinding and proper residence time. |
Feed Material Properties | Hardness, density, and chemical composition affect grinding efficiency and wear. |
Ball Filling and Sizes | Filling ratio and ball size influence grinding efficiency—larger balls for coarse, smaller for fine. |
Armor Surface Shape | Textured surfaces enhance grinding by increasing friction between balls and material. |
Rotation Speed | Optimal speed (65-75% of critical speed) ensures effective grinding without energy waste. |
Milling Fineness | Timely removal of ground product prevents over-grinding and improves efficiency. |
Residence Time and Feed Rate | Higher feed rate reduces residence time for coarser grinding; lower rate for finer grinding. |
Size, Density, and Number of Balls | Larger, denser balls for hard materials; smaller, less dense balls for softer materials. |
Nature of Grinding Material | Hardness, abrasiveness, and moisture content affect grinding efficiency and wear. |
Rotation Speed of Cylinder | Adjusting speed based on material type and desired fineness optimizes grinding performance. |
Maximize your ball mill's efficiency—contact our experts today for tailored solutions!