Chemical Vapor Deposition (CVD) is a process used to produce high-purity, high-performance solid materials, typically under vacuum. The working principle of CVD involves the chemical reaction of vapor-phase precursors to form a solid material on a substrate. This process is widely used in the semiconductor industry to create thin films and coatings. The key to CVD is the controlled chemical reactions that occur on the substrate surface, which are driven by temperature, pressure, and the flow of precursor gases. The process allows for precise control over the thickness, composition, and properties of the deposited material.
Key Points Explained:
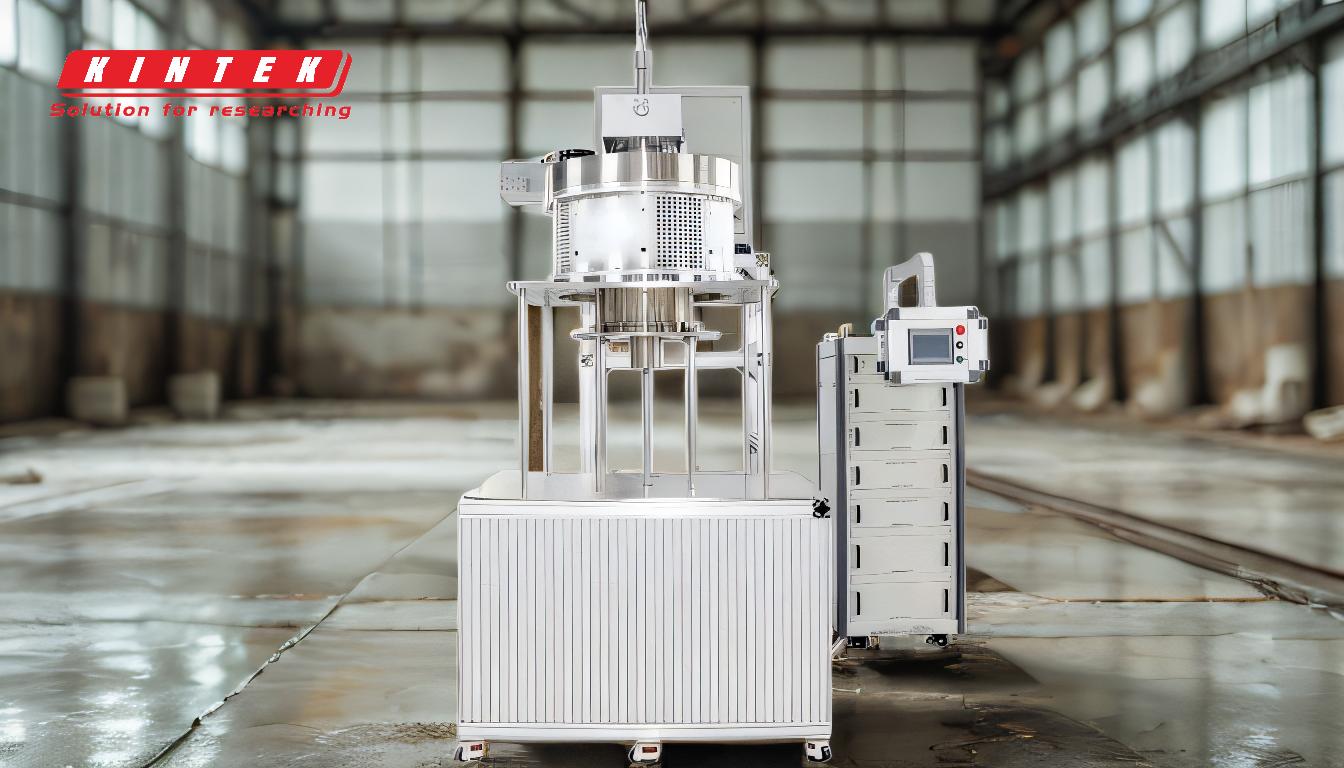
-
Chemical Reaction of Vapor-Phase Precursors:
- In CVD, gaseous reactants (precursors) are introduced into a reaction chamber where they undergo chemical reactions to form a solid material on a heated substrate. The reactions are typically thermally driven and can involve decomposition, reduction, or oxidation of the precursors.
- For example, in the deposition of silicon dioxide (SiO₂), a common precursor is silicon tetrachloride (SiCl₄), which reacts with oxygen (O₂) to form SiO₂ and chlorine gas (Cl₂) as a byproduct.
-
Role of Temperature and Pressure:
- The substrate is heated to a temperature that facilitates the chemical reactions necessary for deposition. The temperature must be carefully controlled to ensure the desired reaction kinetics and material properties.
- The pressure inside the reaction chamber is also critical. Lower pressures can reduce unwanted gas-phase reactions and improve the uniformity of the deposited film. For instance, in short path vacuum distillation, operating under reduced pressure lowers the boiling point of substances, allowing for gentle thermal treatment of heat-sensitive materials.
-
Flow of Precursor Gases:
- The flow rate and composition of the precursor gases are precisely controlled to ensure uniform deposition across the substrate. The gases are typically introduced into the chamber through a gas delivery system that includes mass flow controllers to regulate the flow rates.
- The flow dynamics within the chamber can affect the deposition rate and the quality of the film. Proper design of the gas delivery system is essential to achieve the desired film properties.
-
Deposition on the Substrate:
- The solid material formed by the chemical reactions deposits onto the substrate, forming a thin film. The deposition process can be influenced by the substrate's surface properties, such as roughness and chemical composition.
- The growth of the film is typically layer-by-layer, allowing for precise control over the film's thickness and structure. This is crucial in applications such as semiconductor manufacturing, where even nanometer-scale variations can affect device performance.
-
Applications of CVD:
- CVD is used in a wide range of applications, including the production of semiconductor devices, optical coatings, and protective coatings. For example, CVD is used to deposit silicon nitride (Si₃N₄) as an insulating layer in integrated circuits.
- The process is also used to create advanced materials such as graphene and carbon nanotubes, which have unique electrical, thermal, and mechanical properties.
-
Advantages of CVD:
- CVD allows for the deposition of high-purity materials with excellent control over film properties. The process can be scaled up for industrial production and is compatible with a wide range of materials.
- The ability to deposit films at relatively low temperatures compared to other deposition methods makes CVD suitable for use with temperature-sensitive substrates.
-
Challenges and Considerations:
- One of the main challenges in CVD is the need for precise control over process parameters, including temperature, pressure, and gas flow rates. Any deviation can lead to defects in the deposited film.
- The process can also generate hazardous byproducts, requiring effective exhaust and waste management systems to ensure safety and environmental compliance.
In summary, CVD is a versatile and powerful technique for depositing thin films and coatings with precise control over their properties. The process relies on the chemical reaction of vapor-phase precursors on a heated substrate, driven by carefully controlled temperature, pressure, and gas flow conditions. Despite its challenges, CVD is widely used in industries ranging from semiconductors to advanced materials, offering significant advantages in terms of material purity and process control.
Summary Table:
Key Aspect | Description |
---|---|
Chemical Reaction | Vapor-phase precursors react on a heated substrate to form solid materials. |
Temperature & Pressure | Controlled to ensure precise reaction kinetics and uniform film deposition. |
Precursor Gas Flow | Regulated to achieve uniform deposition and desired film properties. |
Substrate Deposition | Layer-by-layer growth for precise control over thickness and structure. |
Applications | Used in semiconductors, optical coatings, graphene, and carbon nanotubes. |
Advantages | High-purity materials, low-temperature deposition, and scalability. |
Challenges | Precise parameter control and hazardous byproduct management. |
Ready to explore how CVD can enhance your material production? Contact our experts today!