The vacuum annealing process is a specialized heat treatment method performed in a vacuum environment to enhance the properties of metals and alloys. It involves heating the material to a specific temperature, holding it there to allow for structural changes, and then cooling it slowly. This process is carried out in a vacuum annealing furnace, which ensures a contamination-free environment, precise temperature control, and uniform heating. The vacuum environment prevents oxidation and other chemical reactions, resulting in higher purity and improved mechanical properties of the treated material. Vacuum annealing is widely used in industries requiring high-quality materials, such as aerospace, electronics, and medical device manufacturing.
Key Points Explained:
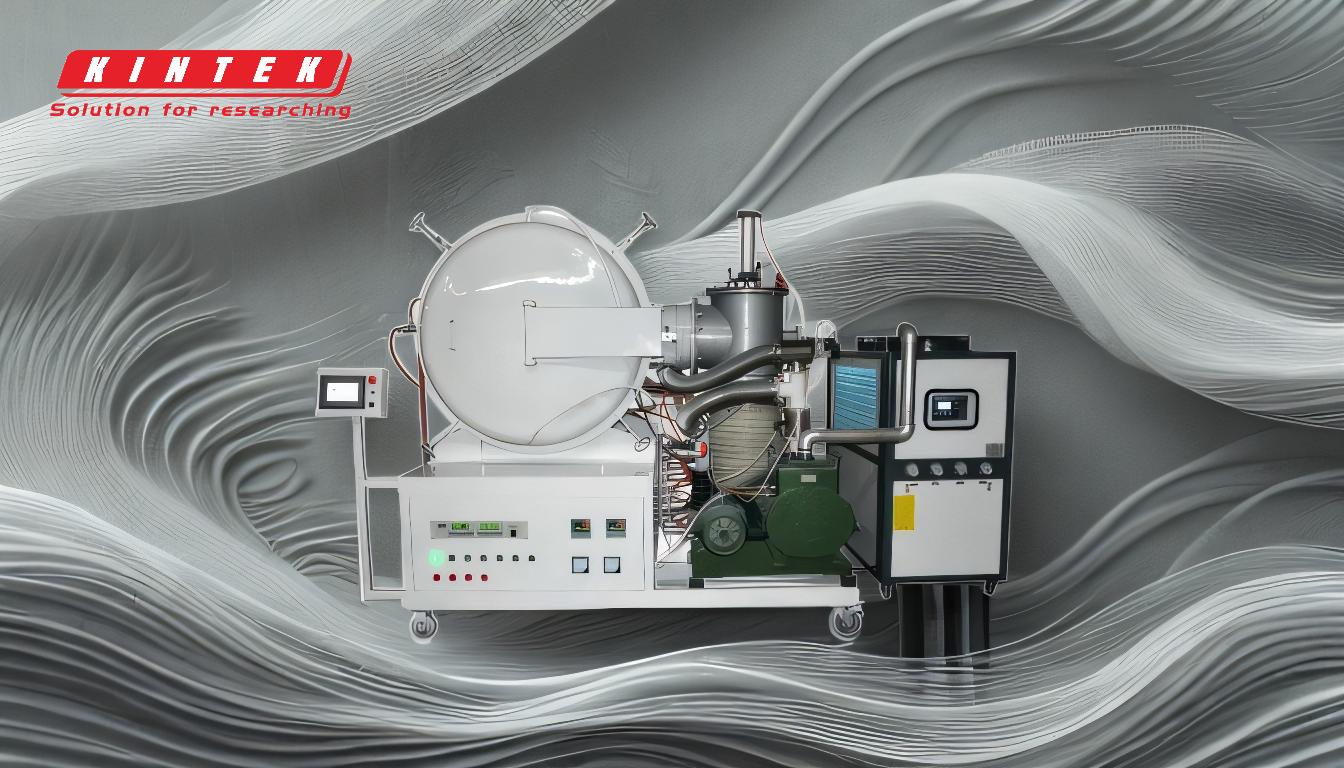
-
What is Vacuum Annealing?
- Vacuum annealing is a heat treatment process where materials are heated to a specific temperature in a vacuum environment, held at that temperature, and then slowly cooled. This process improves the material's ductility, relieves internal stresses, and enhances its mechanical or electrical properties. The vacuum environment prevents oxidation and contamination, ensuring a high-purity end product.
-
Role of the Vacuum Annealing Furnace:
- The vacuum annealing furnace is the core equipment used in this process. It provides a controlled environment with uniform heating and precise temperature regulation. The furnace typically includes a vacuum chamber, heating elements, and cooling systems. The vacuum environment eliminates the presence of oxygen and other reactive gases, preventing oxidation and ensuring a clean, contamination-free process.
-
Key Steps in the Vacuum Annealing Process:
- Heating: The material is heated to a temperature above its recrystallization point but below its melting point. This allows the crystalline structure to become fluid, enabling defects to repair themselves.
- Soaking: The material is held at the target temperature for a specific duration to ensure uniform heating and structural changes.
- Cooling: The material is cooled slowly, either within the furnace or using inert gas, to achieve the desired crystalline structure and properties.
-
Advantages of Vacuum Annealing:
- Contamination-Free Environment: The vacuum prevents oxidation and other chemical reactions, resulting in higher purity.
- Precise Temperature Control: Uniform heating ensures consistent material properties.
- Improved Material Properties: Enhanced ductility, reduced internal stresses, and better mechanical or electrical properties.
- Rapid Cooling Options: Inert gas quenching systems allow for faster cooling, reducing process cycle times.
-
Applications of Vacuum Annealing:
- Vacuum annealing is used in industries that require high-quality materials with precise properties, such as:
- Aerospace: For components requiring high strength and resistance to fatigue.
- Electronics: For semiconductor materials and conductive alloys.
- Medical Devices: For implants and surgical instruments requiring biocompatibility and corrosion resistance.
- Tooling: For improving the durability and performance of cutting tools and dies.
- Vacuum annealing is used in industries that require high-quality materials with precise properties, such as:
-
Comparison with Other Annealing Methods:
- Unlike conventional annealing methods performed in air or protective gas atmospheres, vacuum annealing offers superior control over the environment. This results in fewer impurities, better surface finishes, and more consistent material properties. The absence of oxygen and other reactive gases eliminates the risk of oxidation and decarburization.
-
Importance of Cooling in Vacuum Annealing:
- Cooling is a critical step in the vacuum annealing process. Slow cooling allows the material to develop a more ductile and uniform crystalline structure. In some cases, rapid cooling (quenching) using inert gases is employed to achieve specific material properties, such as increased hardness.
By leveraging the capabilities of a vacuum annealing furnace, manufacturers can achieve superior material properties, ensuring their products meet the stringent requirements of modern industries.
Summary Table:
Aspect | Details |
---|---|
Definition | Heat treatment in a vacuum to enhance material properties. |
Key Equipment | Vacuum annealing furnace for contamination-free, precise heating. |
Process Steps | Heating, soaking, and slow cooling in a vacuum environment. |
Advantages | Contamination-free, precise temperature control, improved material quality. |
Applications | Aerospace, electronics, medical devices, and tooling industries. |
Cooling Importance | Critical for achieving desired crystalline structure and properties. |
Learn how vacuum annealing can elevate your material quality—contact our experts today!