Vacuum evaporation is a Physical Vapor Deposition (PVD) process used to deposit thin films of materials onto substrates. It involves heating a source material in a high vacuum environment until it evaporates or sublimes, forming a vapor that travels in a straight line (line-of-sight) to the substrate, where it condenses to form a thin, high-purity film. The process operates under extremely low gas pressures (10^-5 to 10^-9 Torr) to minimize collisions between gas molecules and the vaporized material, ensuring high-quality film deposition. Common heating methods include resistively heated wires, boats, crucibles, or electron beams, and the process is widely used in industries requiring precise and pure coatings, such as electronics, optics, and semiconductors.
Key Points Explained:
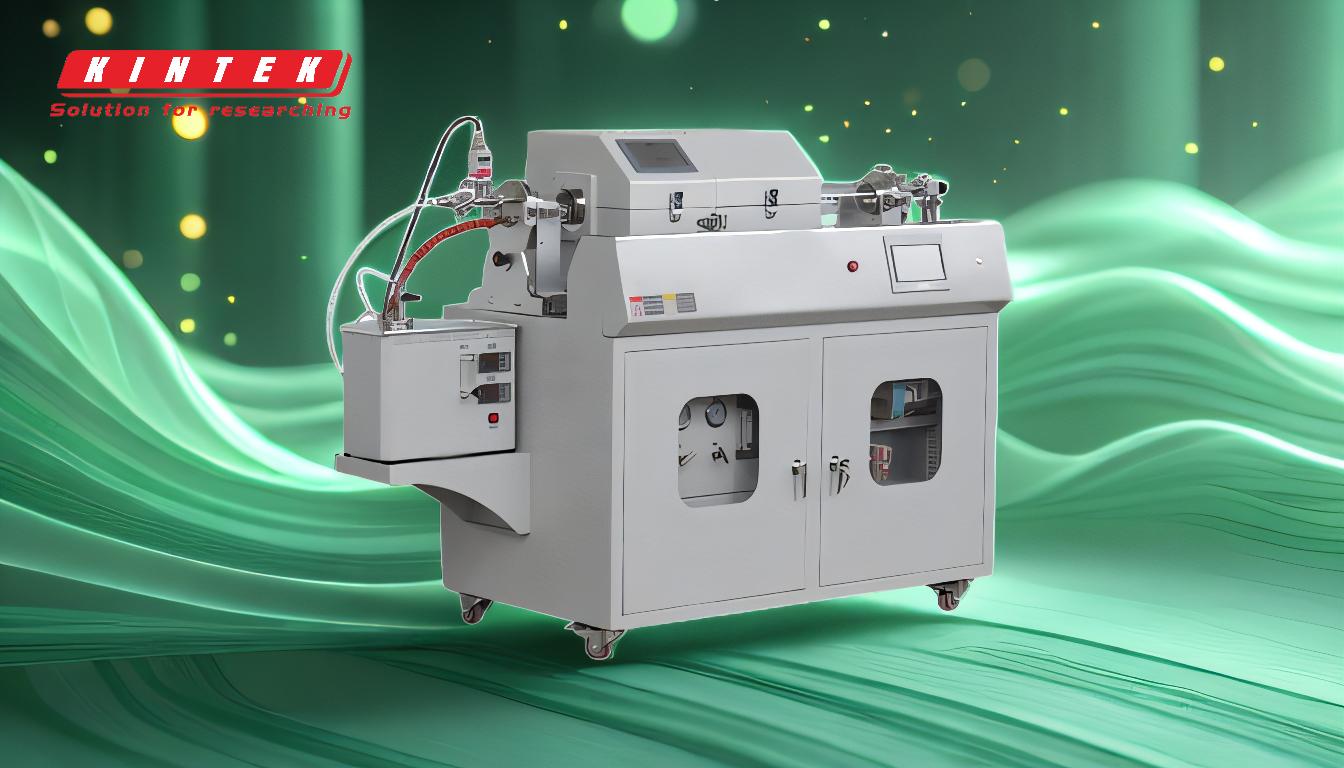
-
Definition and Overview of Vacuum Evaporation in PVD:
- Vacuum evaporation is a subset of PVD techniques.
- It involves the thermal vaporization of a source material in a high vacuum environment.
- The vaporized material travels in a straight line to the substrate, where it condenses to form a thin film.
- This process is known for producing high-purity films due to the absence of gas molecule collisions.
-
Operating Conditions:
- The process operates in a high vacuum range of 10^-5 to 10^-9 Torr.
- The low pressure minimizes interactions between gas molecules and the vaporized material.
- This ensures a clean and controlled environment for film deposition.
-
Vaporization Sources:
- Common heating methods include:
- Resistively heated wires or boats.
- Crucibles.
- Electron beams.
- These sources heat the material to its melting or sublimation point, causing it to evaporate.
- Common heating methods include:
-
Line-of-Sight Deposition:
- The process is line-of-sight, meaning the vaporized material travels directly from the source to the substrate.
- This limits deposition to surfaces directly exposed to the source, making it ideal for coating specific areas.
-
Material Evaporation and Condensation:
- The source material is heated until it evaporates or sublimes into a vapor.
- The vapor diffuses through the vacuum and condenses on the substrate, forming a thin film.
- The substrate temperature is critical for ensuring uniform film formation and strong adhesion.
-
Advantages of Vacuum Evaporation:
- High-purity films due to minimal contamination from gas molecules.
- Precise control over film thickness and composition.
- Suitable for depositing a wide range of materials, including metals, semiconductors, and dielectrics.
-
Applications:
- Widely used in industries such as:
- Electronics (e.g., thin-film transistors, solar cells).
- Optics (e.g., anti-reflective coatings, mirrors).
- Semiconductors (e.g., metallization, passivation layers).
- Also used in decorative coatings and barrier layers.
- Widely used in industries such as:
-
Challenges and Considerations:
- The line-of-sight nature can limit uniform coating on complex geometries.
- High vacuum requirements increase equipment and operational costs.
- Proper substrate heating is essential to avoid defects like poor adhesion or uneven film thickness.
By understanding these key points, equipment and consumable purchasers can better evaluate the suitability of vacuum evaporation for their specific applications, ensuring optimal performance and cost-effectiveness.
Summary Table:
Key Aspect | Details |
---|---|
Process Overview | Thermal vaporization of materials in a high vacuum environment. |
Operating Pressure | 10^-5 to 10^-9 Torr to minimize gas molecule collisions. |
Heating Methods | Resistive wires, boats, crucibles, or electron beams. |
Deposition Type | Line-of-sight, ideal for coating specific areas. |
Advantages | High-purity films, precise thickness control, versatile material deposition. |
Applications | Electronics, optics, semiconductors, decorative coatings, barrier layers. |
Challenges | Limited uniform coating on complex geometries, high equipment costs. |
Explore how vacuum evaporation can enhance your thin film applications—contact our experts today!