Vacuum lamination is a specialized manufacturing process that involves bonding multiple layers of materials together under vacuum pressure to enhance properties such as strength, stability, and appearance. This technique is widely used across various industries, including electronics, automotive, construction, and decorative arts. By applying vacuum pressure, the process ensures uniform adhesion and eliminates air bubbles, resulting in high-quality, durable laminated products. Vacuum lamination is particularly effective for creating complex shapes, curved surfaces, and intricate designs, making it a versatile solution for applications ranging from printed circuit boards and carbon fiber work to furniture production and musical instrument manufacturing.
Key Points Explained:
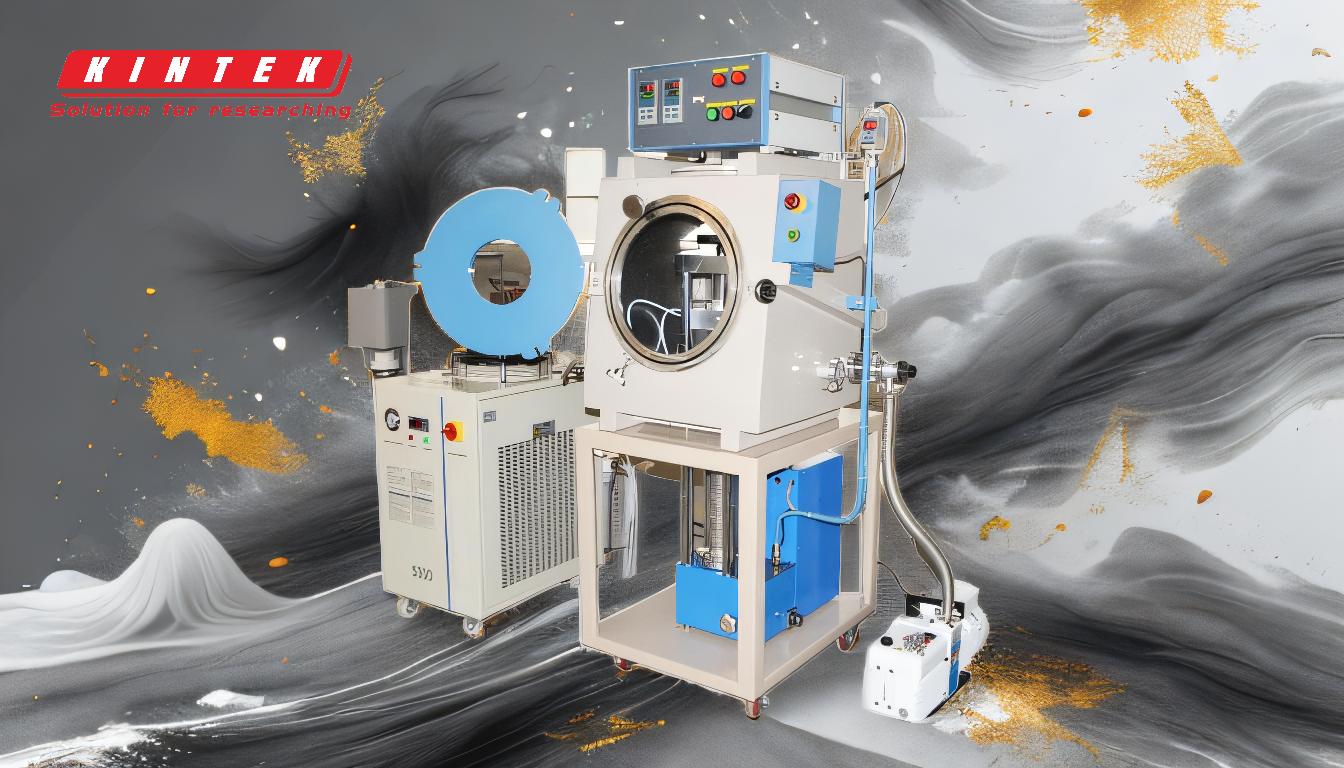
-
Definition and Purpose of Vacuum Lamination:
- Vacuum lamination is a process that bonds multiple layers of materials under vacuum pressure to create a composite material with enhanced properties.
- The primary purpose is to improve strength, stability, and aesthetic appeal while ensuring uniform adhesion and eliminating defects like air bubbles.
-
Applications Across Industries:
- Electronics: Used in the production of printed circuit boards (PCBs), multilayer ceramic capacitors (MLCCs), and hybrid chips.
- Automotive: Applied in carbon fiber work, auto dashboards, and brake line manufacturing.
- Construction and Furniture: Utilized for laminating decorative surfaces, fireproof doors, and curved stairway stringers.
- Decorative Arts and Crafts: Employed in photo and art mountings, musical instrument construction, and clay pottery forming.
- Specialized Manufacturing: Includes surfboard construction, radio-controlled airplane/glider production, and flooring medallions.
-
Materials and Techniques:
- Materials used in vacuum lamination range from wood veneers and carbon fiber to ceramics and leather.
- The process involves placing materials in a vacuum bag or chamber, applying heat and pressure, and allowing the adhesive to cure uniformly.
-
Advantages of Vacuum Lamination:
- Uniform Pressure Distribution: Ensures consistent bonding across the entire surface.
- Complex Shapes and Curves: Allows for the creation of intricate designs and curved surfaces.
- High-Quality Finish: Produces smooth, bubble-free laminates with enhanced durability and aesthetics.
-
Equipment and Tools:
- Specialized vacuum presses and laminating machines are used to achieve precise control over pressure, temperature, and vacuum levels.
- These machines are adaptable for both flat and curved surfaces, making them versatile for various applications.
-
Process Steps:
- Preparation: Arrange layers of materials with adhesive in between.
- Vacuum Sealing: Place the assembly in a vacuum bag or chamber.
- Application of Heat and Pressure: Activate the vacuum press to remove air and apply uniform pressure.
- Curing: Allow the adhesive to cure under controlled conditions.
- Finishing: Remove the laminated product and perform any necessary post-processing.
-
Industries Benefiting from Vacuum Lamination:
- Electronics: Enhances the performance and reliability of components.
- Automotive: Improves the strength and aesthetics of parts.
- Construction: Provides durable and visually appealing surfaces.
- Arts and Crafts: Enables the creation of high-quality, intricate designs.
-
Future Trends and Innovations:
- Advancements in vacuum lamination technology are focusing on automation, energy efficiency, and the use of eco-friendly materials.
- New applications are emerging in fields like renewable energy (e.g., solar panel manufacturing) and aerospace (e.g., lightweight composite materials).
By understanding the principles and applications of vacuum lamination, manufacturers and purchasers can make informed decisions about its use in various industries, ensuring high-quality, cost-effective, and innovative solutions.
Summary Table:
Aspect | Details |
---|---|
Purpose | Bonds materials under vacuum pressure to enhance strength, stability, and aesthetics. |
Applications | Electronics, automotive, construction, decorative arts, and specialized manufacturing. |
Materials | Wood veneers, carbon fiber, ceramics, leather, and more. |
Advantages | Uniform pressure, complex shapes, high-quality finish, and bubble-free results. |
Equipment | Vacuum presses and laminating machines for precise control. |
Process Steps | Preparation, vacuum sealing, heat/pressure application, curing, finishing. |
Future Trends | Automation, energy efficiency, eco-friendly materials, and new applications in renewable energy and aerospace. |
Unlock the potential of vacuum lamination for your projects—contact us today for expert guidance!