Vacuum thermoforming is a manufacturing process used to shape plastic sheets into specific forms using heat, pressure, and a mold. It involves heating a plastic sheet until it becomes pliable, then using vacuum pressure to draw the sheet onto a mold, where it cools and solidifies into the desired shape. This process is particularly useful for creating parts that require precise shaping on one side, such as packaging for food or electronics. Vacuum thermoforming is cost-effective, versatile, and allows for rapid prototyping and production of lightweight, durable products.
Key Points Explained:
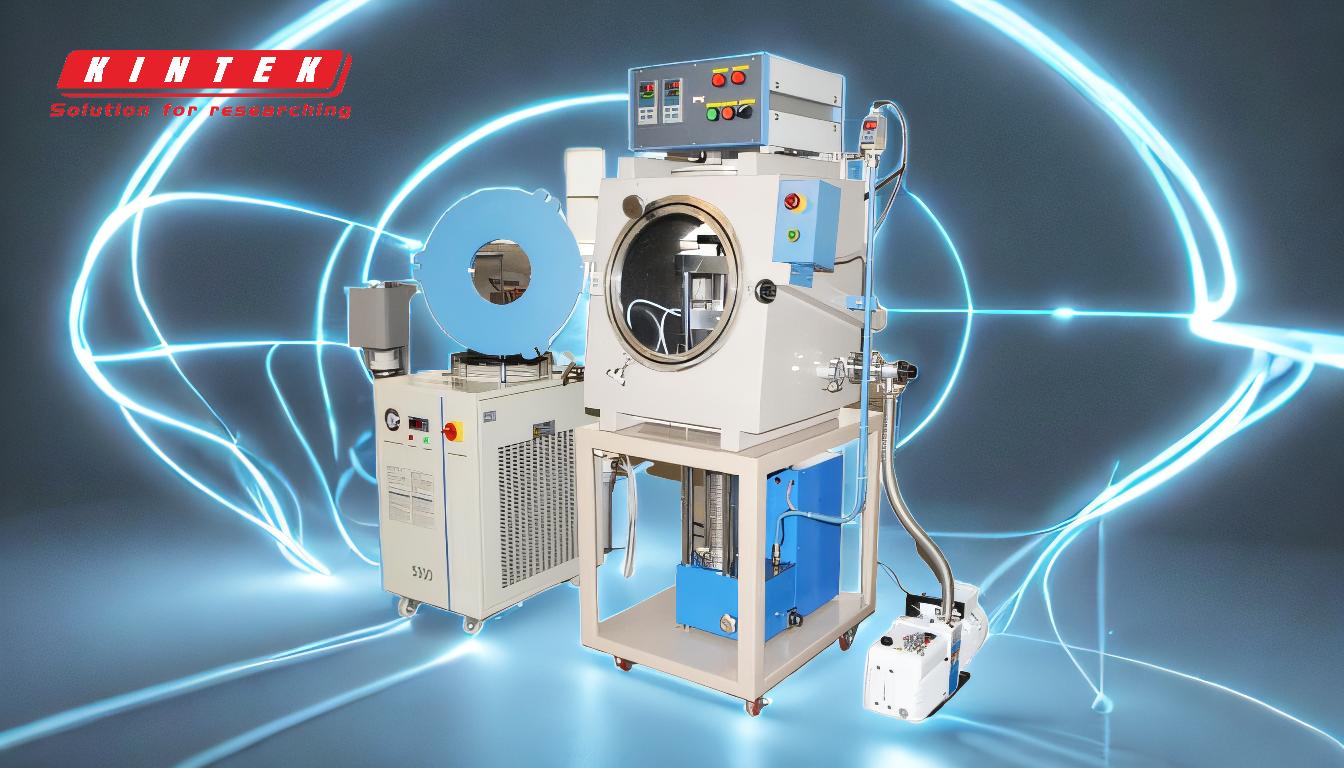
-
Definition of Vacuum Thermoforming:
- Vacuum thermoforming is a subset of plastic thermoforming, where a heated plastic sheet is shaped using a mold and vacuum pressure.
- It is the simplest form of thermoforming, ideal for parts requiring precise shaping on one side.
-
How the Process Works:
- Heating: A plastic sheet is heated until it becomes soft and pliable.
- Molding: The heated sheet is placed over a mold, and vacuum pressure is applied to draw the sheet onto the mold's surface.
- Cooling and Solidification: The plastic cools and hardens, retaining the shape of the mold.
- Trimming: Excess material is removed to achieve the final product.
-
Advantages of Vacuum Thermoforming:
- Cost-Effective: Lower tooling costs compared to other molding processes.
- Versatility: Suitable for a wide range of applications, including packaging, automotive parts, and medical devices.
- Rapid Prototyping: Allows for quick design iterations and production of prototypes.
- Lightweight and Durable: Produces lightweight yet strong products.
-
Applications:
- Packaging: Commonly used for contoured packaging for food, electronics, and consumer goods.
- Automotive: Used for interior components like dashboards and door panels.
- Medical: Produces trays, enclosures, and other medical device components.
- Retail Displays: Creates attractive and functional displays for products.
-
Materials Used:
- Common materials include ABS, PVC, PET, and polycarbonate, chosen for their flexibility, durability, and ease of forming.
-
Limitations:
- Limited to parts that require precise shaping on one side.
- Thicker materials may require more advanced techniques or machinery.
-
Comparison to Other Thermoforming Methods:
- Unlike pressure forming or twin-sheet forming, vacuum thermoforming uses only vacuum pressure, making it simpler and more economical for certain applications.
By understanding these key points, a purchaser can evaluate whether vacuum thermoforming is the right process for their specific needs, considering factors like cost, material, and application requirements.
Summary Table:
Aspect | Details |
---|---|
Definition | A process using heat, vacuum pressure, and molds to shape plastic sheets. |
Process Steps | Heating → Molding → Cooling → Trimming |
Advantages | Cost-effective, versatile, rapid prototyping, lightweight, and durable. |
Applications | Packaging, automotive, medical, retail displays. |
Materials | ABS, PVC, PET, polycarbonate. |
Limitations | Limited to one-sided shaping; thicker materials may require advanced tools. |
Ready to explore vacuum thermoforming for your project? Contact us today to learn more!