Vacuum casting is a versatile manufacturing process used to create high-quality prototypes and small production runs. It is particularly suitable for materials that can be cured or solidified under vacuum conditions. The process involves creating a silicone mold from a master model, then pouring a liquid material into the mold and curing it under vacuum to eliminate air bubbles and ensure precise replication. Commonly used materials for vacuum casting include polyurethanes, silicones, epoxies, and certain thermoplastics. Each material offers unique properties, such as flexibility, durability, or heat resistance, making vacuum casting ideal for applications in industries like automotive, aerospace, consumer goods, and medical devices.
Key Points Explained:
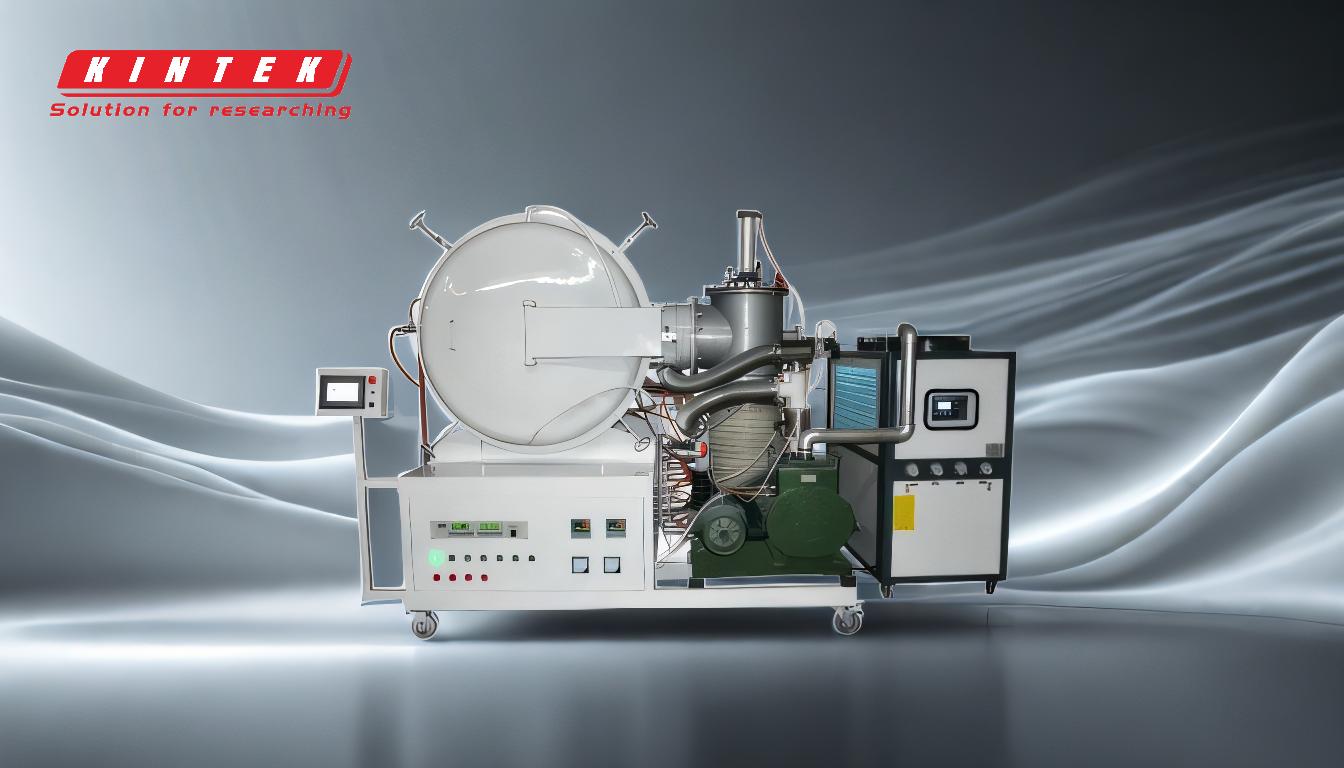
-
Polyurethanes (PU)
- Polyurethanes are the most commonly used materials in vacuum casting due to their versatility and wide range of properties.
- They can mimic the characteristics of engineering plastics like ABS, PP, or PC, making them suitable for functional prototypes.
- Key properties include high strength, flexibility, and resistance to wear and tear.
- Available in various grades, such as rigid, semi-rigid, and flexible, to meet specific application requirements.
-
Silicones
- Silicones are used for creating flexible and elastic parts, such as gaskets, seals, or soft-touch components.
- They are ideal for applications requiring high temperature resistance and biocompatibility, making them suitable for medical devices.
- Silicones can replicate fine details and textures, ensuring high-quality surface finishes.
-
Epoxies
- Epoxy resins are known for their excellent mechanical properties, including high strength, stiffness, and chemical resistance.
- They are often used for structural components or parts requiring dimensional stability.
- Epoxies can be modified to achieve specific properties, such as increased thermal conductivity or electrical insulation.
-
Thermoplastics
- Certain thermoplastics, such as ABS-like or PP-like resins, can be used in vacuum casting to simulate injection-molded parts.
- These materials are ideal for functional testing and end-use applications.
- They offer good impact resistance, durability, and ease of post-processing (e.g., painting or machining).
-
Specialty Materials
- Vacuum casting can also accommodate specialty materials, such as flame-retardant resins, transparent resins, or rubber-like compounds.
- These materials are tailored for specific applications, such as automotive interiors, transparent housings, or soft-touch grips.
-
Material Selection Considerations
- When choosing a material for vacuum casting, consider factors like mechanical properties, thermal resistance, chemical compatibility, and surface finish requirements.
- The material must be compatible with the vacuum casting process, ensuring proper flow, curing, and demolding.
- Post-processing options, such as painting, plating, or assembly, should also be considered to meet end-use requirements.
-
Advantages of Vacuum Casting Materials
- Vacuum casting materials offer excellent surface finish and detail replication, making them ideal for high-quality prototypes.
- The process allows for quick turnaround times and cost-effective production of small batches.
- Materials can be customized to meet specific performance criteria, providing flexibility for diverse applications.
By understanding the range of materials available for vacuum casting and their respective properties, manufacturers and designers can select the most suitable option for their specific needs, ensuring optimal performance and functionality in the final product.
Summary Table:
Material Type | Key Properties | Common Applications |
---|---|---|
Polyurethanes (PU) | High strength, flexibility, wear resistance | Functional prototypes, automotive |
Silicones | Elastic, high temp resistance, biocompatible | Medical devices, gaskets, seals |
Epoxies | High strength, stiffness, chemical resistance | Structural components, electronics |
Thermoplastics | Impact resistance, durability, easy post-processing | End-use parts, consumer goods |
Specialty Materials | Flame-retardant, transparent, rubber-like | Automotive interiors, transparent housings |
Need help selecting the right material for your vacuum casting project? Contact our experts today for personalized advice!