Steel is an alloy primarily composed of iron and carbon, and its melting point varies depending on its composition. Generally, the melting point of steel ranges between 1370°C (2500°F) and 1510°C (2750°F). The exact temperature depends on the carbon content and other alloying elements. For example, low-carbon steels melt at the lower end of this range, while high-carbon steels and alloy steels melt at higher temperatures. Molten steel is used in various industrial processes, such as casting and forging, and understanding its melting behavior is critical for manufacturing and metallurgical applications.
Key Points Explained:
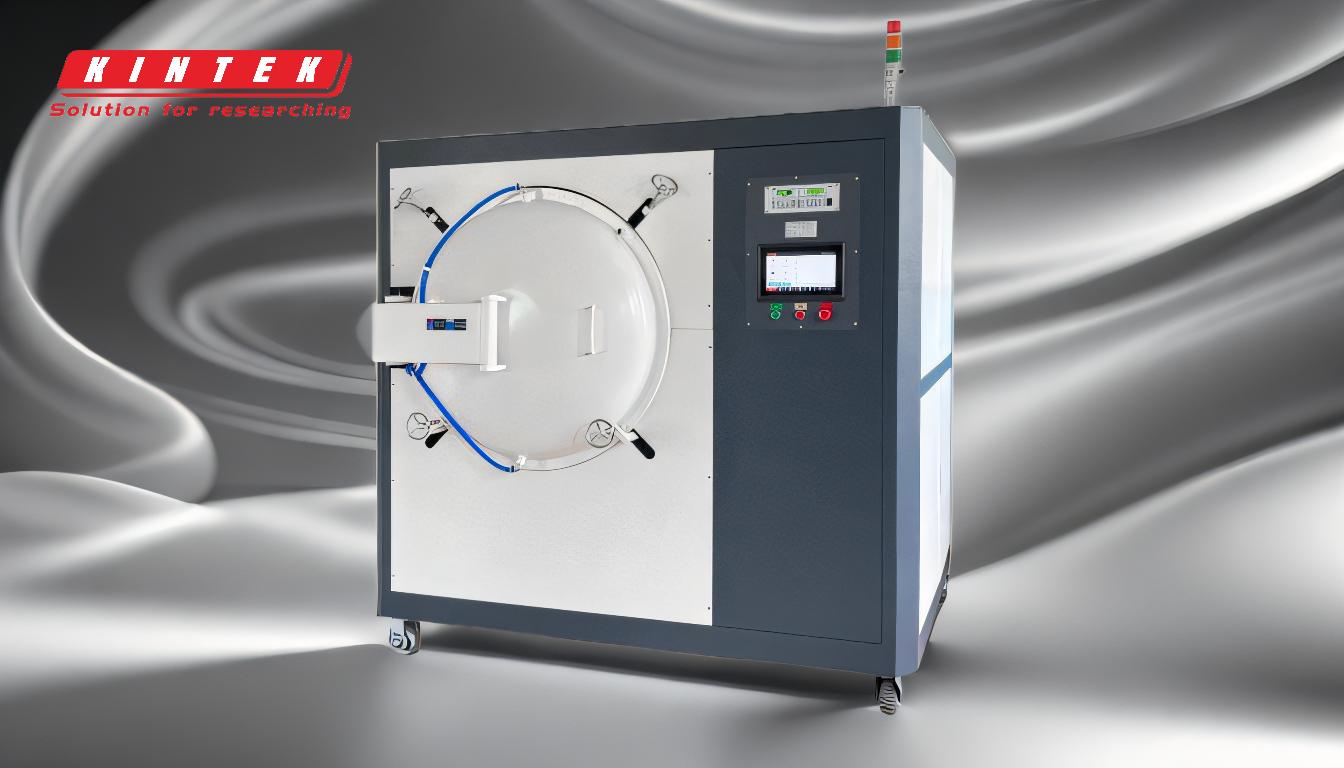
-
Composition of Steel and Its Impact on Melting Temperature
- Steel is primarily made of iron and carbon, but it can also contain other elements like manganese, silicon, and nickel.
- The carbon content significantly affects the melting point. Low-carbon steels (e.g., mild steel) melt at around 1370°C (2500°F), while high-carbon steels melt closer to 1510°C (2750°F).
- Alloying elements like chromium or tungsten can further increase the melting point, making the steel more heat-resistant.
-
Melting Range of Steel
- Unlike pure metals, steel does not have a single melting point but rather a melting range due to its alloy composition.
- The melting process begins at the solidus temperature (when the steel starts to melt) and completes at the liquidus temperature (when it is fully molten).
- For most steels, this range falls between 1370°C (2500°F) and 1510°C (2750°F).
-
Industrial Applications of Molten Steel
- Molten steel is used in processes like casting, where it is poured into molds to create complex shapes.
- It is also used in forging, where it is heated to a plastic state and shaped under pressure.
- Understanding the melting temperature is crucial for controlling these processes and ensuring the quality of the final product.
-
Factors Influencing Melting Temperature
- Carbon Content: Higher carbon content raises the melting point.
- Alloying Elements: Elements like chromium, nickel, and molybdenum can increase the melting temperature.
- Impurities: Impurities can lower the melting point and affect the steel's properties.
-
Practical Considerations for Equipment
- Furnaces used to melt steel, such as electric arc furnaces or induction furnaces, must withstand temperatures exceeding 1510°C (2750°F).
- Refractory materials lining the furnaces must be chosen carefully to handle the extreme heat and chemical reactions with molten steel.
By understanding the melting behavior of steel, manufacturers can optimize their processes and select the right materials and equipment for their applications.
Summary Table:
Aspect | Details |
---|---|
Melting Range | 1370°C (2500°F) to 1510°C (2750°F) |
Low-Carbon Steel | Melts at ~1370°C (2500°F) |
High-Carbon Steel | Melts closer to 1510°C (2750°F) |
Alloying Elements | Chromium, nickel, and molybdenum increase melting temperature |
Industrial Applications | Casting, forging, and metallurgical processes |
Equipment Requirements | Furnaces must withstand >1510°C (2750°F) |
Need help selecting the right furnace for melting steel? Contact our experts today!