Sintering is a thermal process used to consolidate powdered materials into a solid structure by heating them to temperatures below their melting point. The specific temperature required for sintering varies depending on the material being processed, but it is typically around 0.6 times the material's melting temperature (Tm). For dental applications, sintering temperatures usually range from 1200°C to 1400°C. The process involves precise control of temperature, pressure, and atmosphere to ensure the quality and stability of the final product. Advanced sintering furnaces use AI-based controllers to maintain precise temperatures, enhancing efficiency and power savings.
Key Points Explained:
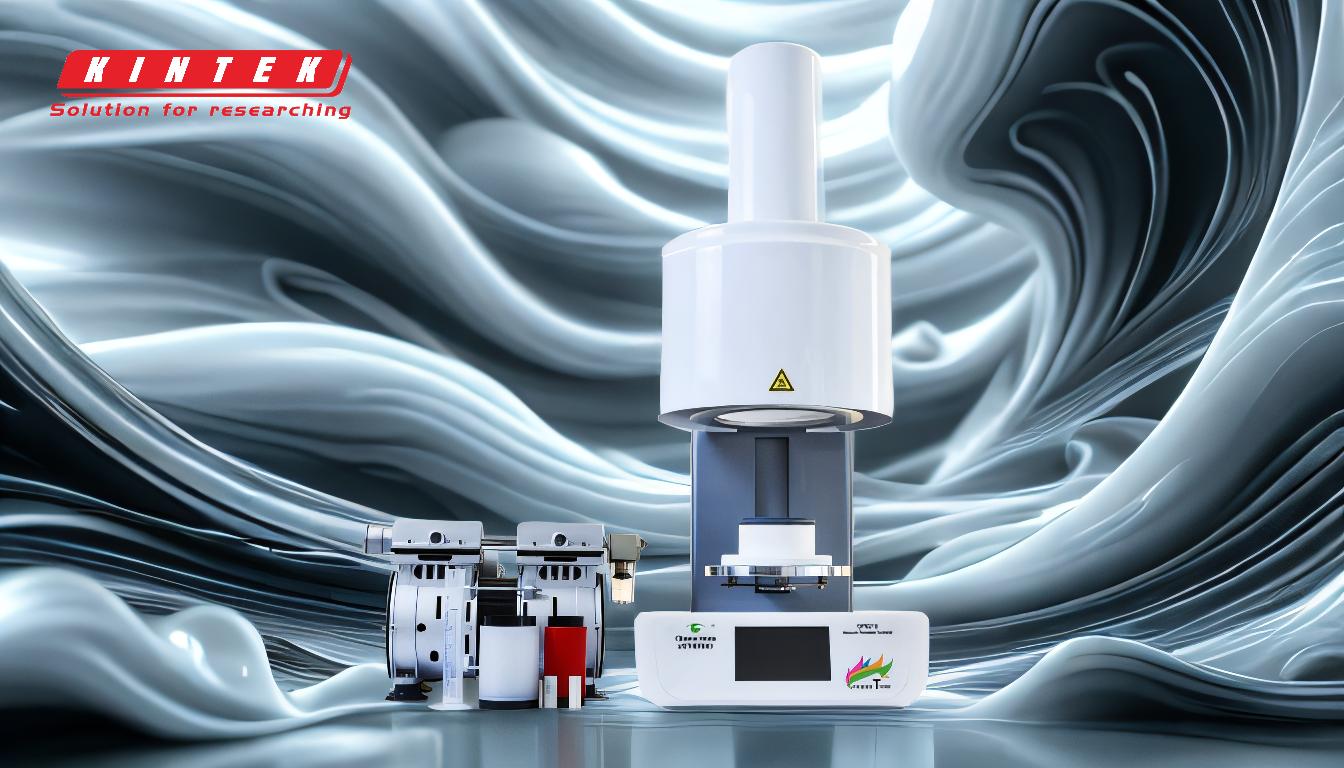
-
Sintering Temperature Range:
- Sintering typically requires temperatures greater than approximately 0.6 times the material's melting temperature (Tm). This ensures sufficient diffusion for particle bonding without causing complete melting.
- For dental applications, the sintering temperature usually ranges from 1200°C to 1400°C, which is suitable for materials like zirconia used in dental restorations.
-
Material-Specific Temperatures:
- The exact sintering temperature depends on the material being processed. For instance, metals, ceramics, and polymers each have different melting points and thus require different sintering temperatures.
- The process must maintain temperatures below the material's melting point to avoid liquefaction while still achieving the necessary particle bonding.
-
Stages of the Sintering Process:
- Preparation: The raw material is formed into a specific shape, usually as a powder, and then compacted to ensure uniformity and eliminate voids.
- Heating and Consolidation: The compacted material is heated in a sintering furnace to a controlled temperature, facilitating particle bonding through diffusion.
- Cooling: The sintered product is cooled to solidify into a rigid and cohesive structure.
-
Precision and Control:
- Sintering furnaces must maintain precise control over temperature, pressure, and atmosphere to ensure the quality and stability of the final product.
- Advanced sintering furnaces use AI-based controllers to maintain precise temperatures across all zones, resulting in increased efficiency and power savings.
-
Applications of Sintering:
- Sintering is widely used in various industries, including dentistry, where it is crucial for creating high-quality dental restorations.
- The process is also used in the production of metal and ceramic components, where precise temperature control is essential for achieving the desired material properties.
By understanding these key points, purchasers of sintering equipment can make informed decisions about the type of furnace and control systems needed for their specific applications. The precise control of temperature and other parameters is crucial for achieving high-quality results in sintering processes.
Summary Table:
Key Aspect | Details |
---|---|
Sintering Temperature Range | Typically 0.6 times the material's melting point (Tm). Dental: 1200°C–1400°C. |
Material-Specific Temperatures | Varies for metals, ceramics, and polymers. Must stay below melting point. |
Stages of Sintering | Preparation → Heating/Consolidation → Cooling. |
Precision and Control | AI-based controllers ensure precise temperature, pressure, and atmosphere. |
Applications | Dentistry, metal, and ceramic component production. |
Ready to optimize your sintering process? Contact us today for expert guidance and advanced furnace solutions!