Ceramic sintering is a high-temperature process used to densify ceramic materials, reducing porosity and enhancing their mechanical and physical properties. The process typically occurs at temperatures ranging from 900°C (1650°F) to 1250°C (2300°F), depending on the specific ceramic material and desired outcomes. During sintering, solid particles bond, grain boundaries decrease, and material transfer occurs, leading to increased density and the formation of a hard, durable polycrystalline structure. Temperature control is crucial, as it influences grain boundary diffusion, bulk diffusion, and overall densification. This process is widely used in manufacturing ceramic objects, such as pottery and advanced materials like zirconia, which transforms from a monoclinic to a polytetragonal structure, significantly improving its hardness and density.
Key Points Explained:
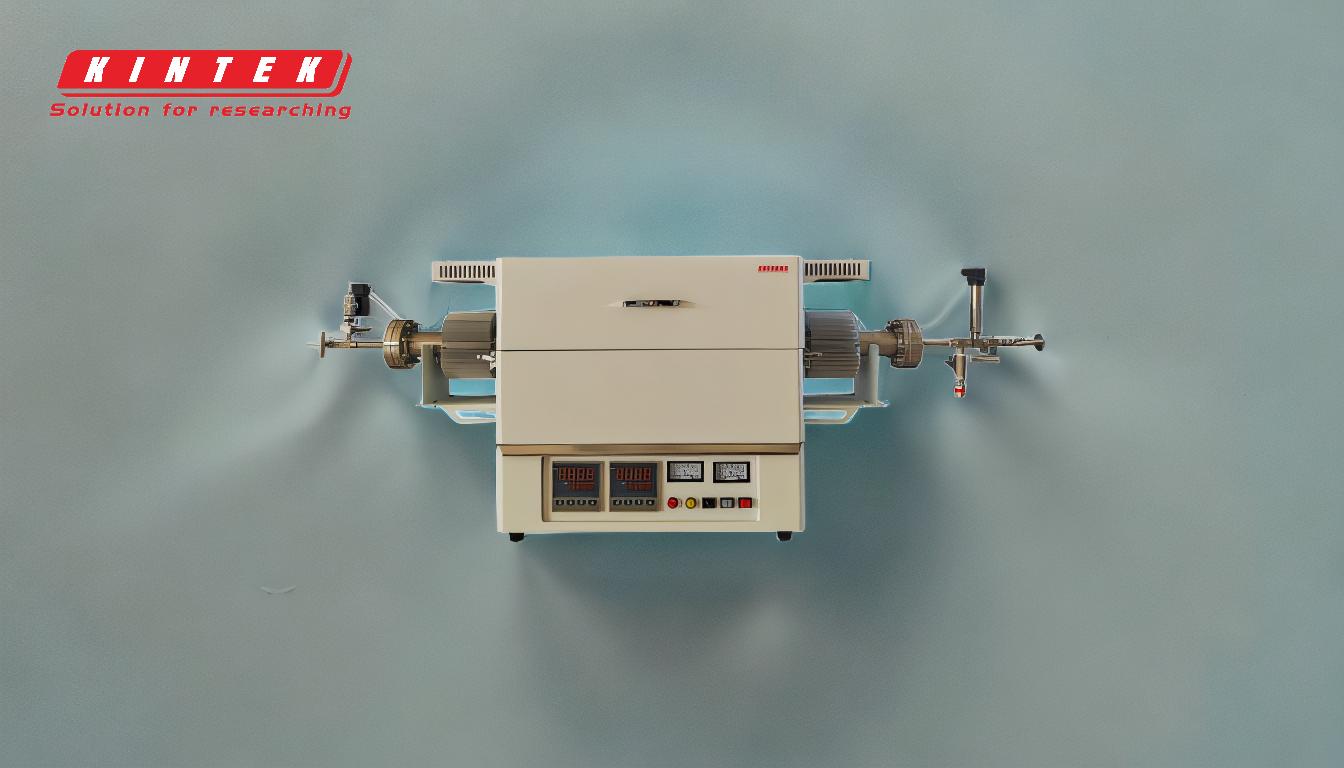
-
Definition and Purpose of Ceramic Sintering:
- Ceramic sintering is a process that involves heating ceramic materials, often under pressure, to reduce porosity and increase particle density. This results in improved mechanical properties such as strength, hardness, and translucency. For example, zirconia undergoes a structural transformation during sintering, becoming significantly harder and denser.
-
Temperature Range for Ceramic Sintering:
- The sintering process typically occurs at temperatures between 900°C (1650°F) and 1250°C (2300°F). This range varies depending on the type of ceramic material and the desired properties. Higher temperatures facilitate better particle bonding and densification.
-
Mechanisms of Sintering:
- During sintering, powder particles undergo material migration and grain boundary movement under high temperatures. This leads to:
- Bonding of solid particles.
- Growth of grains.
- Reduction of voids and grain boundaries.
- Formation of a dense, hard polycrystalline structure.
- During sintering, powder particles undergo material migration and grain boundary movement under high temperatures. This leads to:
-
Importance of Temperature Control:
- Temperature is a critical factor in sintering because it directly affects:
- Grain boundary diffusion.
- Bulk diffusion.
- Material transfer and densification.
- Proper temperature control ensures the formation of a uniform microstructure and optimal mechanical properties.
- Temperature is a critical factor in sintering because it directly affects:
-
Applications of Ceramic Sintering:
- Sintering is widely used in the manufacture of ceramic objects, including:
- Pottery and traditional ceramics.
- Advanced ceramics like zirconia, which are used in dental and industrial applications due to their hardness and durability.
- Sintering is widely used in the manufacture of ceramic objects, including:
-
Role of Pressure and Atmosphere:
- In some cases, sintering is combined with pressure or conducted in a controlled atmosphere to enhance densification and achieve specific material properties. For example, pressure-assisted sintering can reduce the required temperature and time.
-
Material Transformation During Sintering:
- Ceramic materials, such as zirconia, undergo significant structural changes during sintering. For instance, zirconia transforms from a monoclinic to a polytetragonal crystalline structure, resulting in a material that is extremely hard and dense.
-
Shrinkage and Densification:
- Sintering often involves material shrinkage as glass phases flow at the transition temperature. This consolidates the powdery structure, reduces porosity, and increases density, ultimately forming a durable ceramic body.
By understanding these key points, purchasers of equipment and consumables can make informed decisions about the sintering process, ensuring they select the right materials and conditions for their specific applications.
Summary Table:
Aspect | Details |
---|---|
Temperature Range | 900°C (1650°F) to 1250°C (2300°F) |
Purpose | Reduces porosity, enhances mechanical and physical properties |
Key Mechanisms | Particle bonding, grain boundary reduction, material transfer |
Critical Factors | Temperature control, grain boundary diffusion, bulk diffusion |
Applications | Pottery, advanced ceramics (e.g., zirconia) |
Material Transformation | Monoclinic to polytetragonal structure (e.g., zirconia) |
Need help optimizing your ceramic sintering process? Contact our experts today for tailored solutions!