Chemical Vapor Deposition (CVD) is a versatile and widely used technique for depositing thin films and coatings onto substrates. It involves the chemical reaction of volatile precursors at high temperatures to form a solid material on the substrate. The temperature maintained during the CVD process is critical, as it influences the reaction kinetics, film quality, and substrate compatibility. CVD processes typically operate at temperatures ranging from 200°C to 1200°C, depending on the specific materials, precursors, and desired film properties. Higher temperatures are often required for high-quality crystalline films, while lower temperatures are used for substrates that cannot withstand extreme heat. The choice of temperature is a balance between achieving the desired material properties and ensuring substrate integrity.
Key Points Explained:
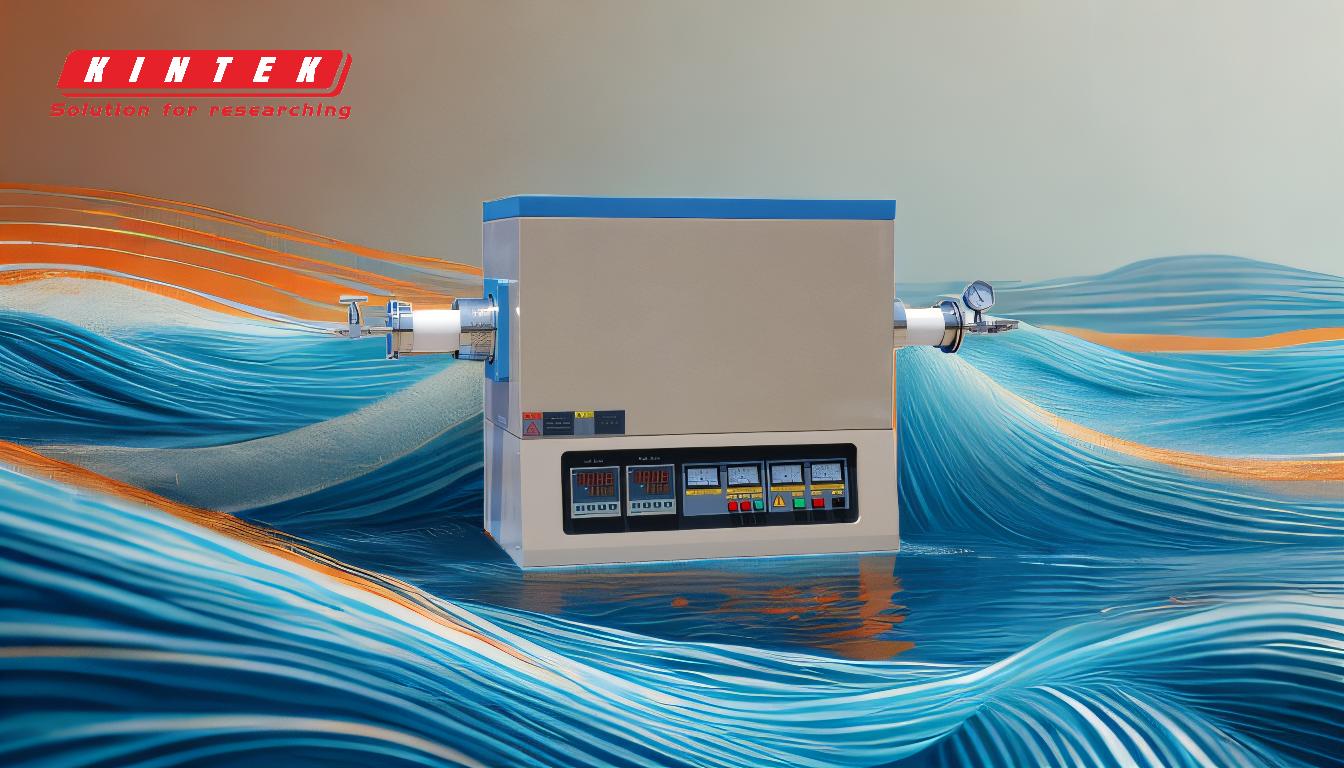
-
Temperature Range in CVD:
- CVD processes operate within a broad temperature range, typically between 200°C and 1200°C.
- The exact temperature depends on the material being deposited, the precursors used, and the substrate's thermal stability.
- For example, silicon-based films often require temperatures above 600°C, while some polymer or organic coatings can be deposited at much lower temperatures.
-
Factors Influencing CVD Temperature:
- Precursor Reactivity: Highly reactive precursors may require lower temperatures, while less reactive ones need higher temperatures to initiate the chemical reaction.
- Substrate Compatibility: Some substrates, such as polymers or certain metals, cannot withstand high temperatures, necessitating lower-temperature CVD processes.
- Film Quality and Crystallinity: Higher temperatures are often necessary to achieve dense, crystalline films with minimal defects.
-
Types of CVD and Their Temperature Requirements:
- Thermal CVD: Operates at high temperatures (600°C–1200°C) and is commonly used for depositing materials like silicon, silicon carbide, and diamond.
- Plasma-Enhanced CVD (PECVD): Uses plasma to lower the required temperature (200°C–400°C), making it suitable for temperature-sensitive substrates.
- Atomic Layer Deposition (ALD): A subset of CVD that operates at relatively low temperatures (100°C–300°C) and provides precise control over film thickness.
-
Challenges of High-Temperature CVD:
- High temperatures can limit the types of substrates that can be used, as some materials may degrade or deform.
- The use of toxic chemicals and high temperatures requires stringent safety measures, including proper ventilation, protective equipment, and waste disposal protocols.
-
Applications and Temperature Considerations:
- Semiconductor Manufacturing: High-temperature CVD is used to deposit silicon dioxide, silicon nitride, and other materials critical for integrated circuits.
- Protective Coatings: Lower-temperature CVD processes are employed to apply wear-resistant or friction-reducing coatings on temperature-sensitive components.
- Optical and Electronic Devices: CVD is used to deposit thin films for solar cells, LEDs, and other optoelectronic devices, with temperature tailored to the specific application.
-
Precursor Selection and Temperature:
- The choice of precursors, such as halides, hydrides, or organometallics, influences the required temperature. For example, silicon tetrachloride (SiCl4) typically requires higher temperatures compared to silane (SiH4).
- Oxygen or other reactive gases may be introduced to facilitate the reaction, further influencing the temperature profile.
-
Temperature Control in CVD Systems:
- Precise temperature control is achieved using advanced heating systems, such as resistive heaters or induction coils, and temperature sensors to monitor and maintain the desired conditions.
- In some systems, a temperature control unit (TCU) circulates liquids like water or oil to regulate the temperature of the reactor walls and extraction chamber.
In summary, the temperature maintained in CVD is a critical parameter that varies widely depending on the application, materials, and equipment. Understanding the interplay between temperature, precursor chemistry, and substrate properties is essential for optimizing the CVD process and achieving high-quality results.
Summary Table:
Aspect | Details |
---|---|
Temperature Range | 200°C to 1200°C, depending on materials, precursors, and substrate stability. |
Key Factors | Precursor reactivity, substrate compatibility, and desired film quality. |
Types of CVD | - Thermal CVD (600°C–1200°C) |
- PECVD (200°C–400°C)
- ALD (100°C–300°C) | | Applications | Semiconductor manufacturing, protective coatings, and optoelectronic devices.| | Temperature Control | Achieved using resistive heaters, induction coils, and temperature sensors. |
Need help optimizing your CVD process? Contact our experts today for tailored solutions!