Heat treatment furnaces are essential in various industrial and laboratory settings for processes like annealing, hardening, sintering, and tempering. The choice of furnace depends on factors such as the material being treated, the required temperature, and the specific heat treatment process. Common types of furnaces used for heat treatment include electric arc furnaces, combustion furnaces, electric resistance furnaces, vacuum furnaces, and chamber furnaces. Each type has unique advantages, such as precise temperature control, uniform heating, and the ability to handle different quenching media. Understanding the operating processes and benefits of each furnace type ensures optimal heat treatment results, reduced failure rates, and extended equipment lifespan.
Key Points Explained:
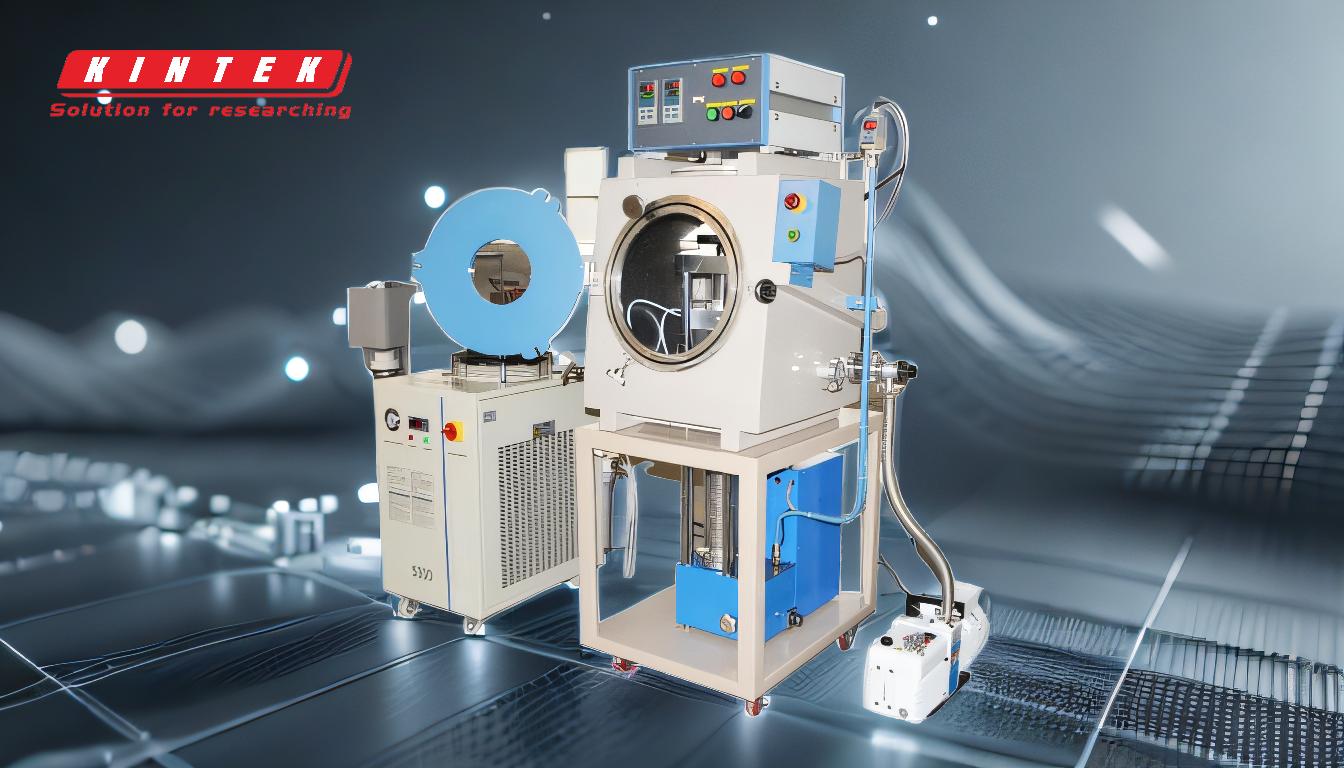
-
Types of Heat Treatment Furnaces:
- Electric Arc Furnaces: Utilize electric arcs to generate high temperatures, ideal for melting and refining metals.
- Combustion Furnaces: Use natural gas or propane as fuel, suitable for high-temperature applications.
- Electric Resistance Furnaces: Offer precise temperature control and uniform heating, commonly used in laboratories and industrial settings.
- Vacuum Furnaces: Provide a controlled atmosphere, reducing oxidation and contamination, crucial for high-precision heat treatment processes.
- Chamber Furnaces: Designed for intermittent heating processes, suitable for batch processing of small parts or large workpieces.
-
Heat Treatment Processes:
- Annealing: Softens materials, improves machinability, and relieves internal stresses.
- Hardening: Increases material hardness and strength through rapid cooling or quenching.
- Sintering: Bonds powdered materials by heating below the melting point, used in powder metallurgy.
- Tempering: Reduces brittleness in hardened materials by reheating to a lower temperature.
-
Quenching Media:
- Water and Brine: Commonly used for rapid cooling, suitable for carbon steels.
- Oils: Provide slower cooling rates, reducing the risk of cracking in alloy steels.
- Polymer Solutions: Offer controlled cooling rates, minimizing distortion and stress.
- Molten Salts and Metals: Used for specialized applications requiring precise cooling rates.
- Gases: Inert gases like nitrogen or argon are used in vacuum furnaces to prevent oxidation.
-
Benefits of Electric Furnaces:
- Uniform Temperature Distribution: Ensures consistent heat treatment results.
- Precise Temperature Control: Allows for accurate regulation of heating and cooling rates.
- High Heat Utilization Efficiency: Reduces energy consumption and operational costs.
- Pollution-Free Operation: Maintains a clean working environment, free from emissions.
- Convenience: Easy to start, stop, and switch between different heat treatment processes.
-
Operating Considerations:
- Vacuum Furnace Operation: Mastering the correct operating process is crucial to achieve the desired heat treatment effect, reduce failure rates, and extend the furnace's service life.
- Cooling Methods: Some materials require slow cooling in the furnace, while others need rapid quenching to achieve the desired properties.
By understanding the various types of furnaces, heat treatment processes, and operating considerations, you can select the most appropriate furnace for your specific heat treatment needs, ensuring optimal results and efficiency.
Summary Table:
Furnace Type | Key Features | Best For |
---|---|---|
Electric Arc Furnace | High temperatures, ideal for melting and refining metals | Metal refining and high-temperature processes |
Combustion Furnace | Uses natural gas or propane, suitable for high-temperature applications | High-temperature industrial processes |
Electric Resistance Furnace | Precise temperature control, uniform heating | Laboratories and industrial settings |
Vacuum Furnace | Controlled atmosphere, reduces oxidation and contamination | High-precision heat treatment processes |
Chamber Furnace | Intermittent heating, batch processing of small or large workpieces | Batch processing and versatile applications |
Need help choosing the right furnace for your heat treatment needs? Contact our experts today!