Calcination is a thermal process used to heat materials, typically metal ores or inorganic compounds, to high temperatures below their melting points in the presence of limited air or oxygen. The primary purpose of calcination is to remove volatile impurities, such as water, carbon dioxide, or sulfur dioxide, and to chemically dissociate compounds into simpler forms. This process is widely used in industries like metallurgy, ceramics, and chemical manufacturing to purify materials, create inorganic compounds, and prepare substances for further processing. Calcination furnaces are essential tools for achieving these objectives, making the process critical in material science and industrial applications.
Key Points Explained:
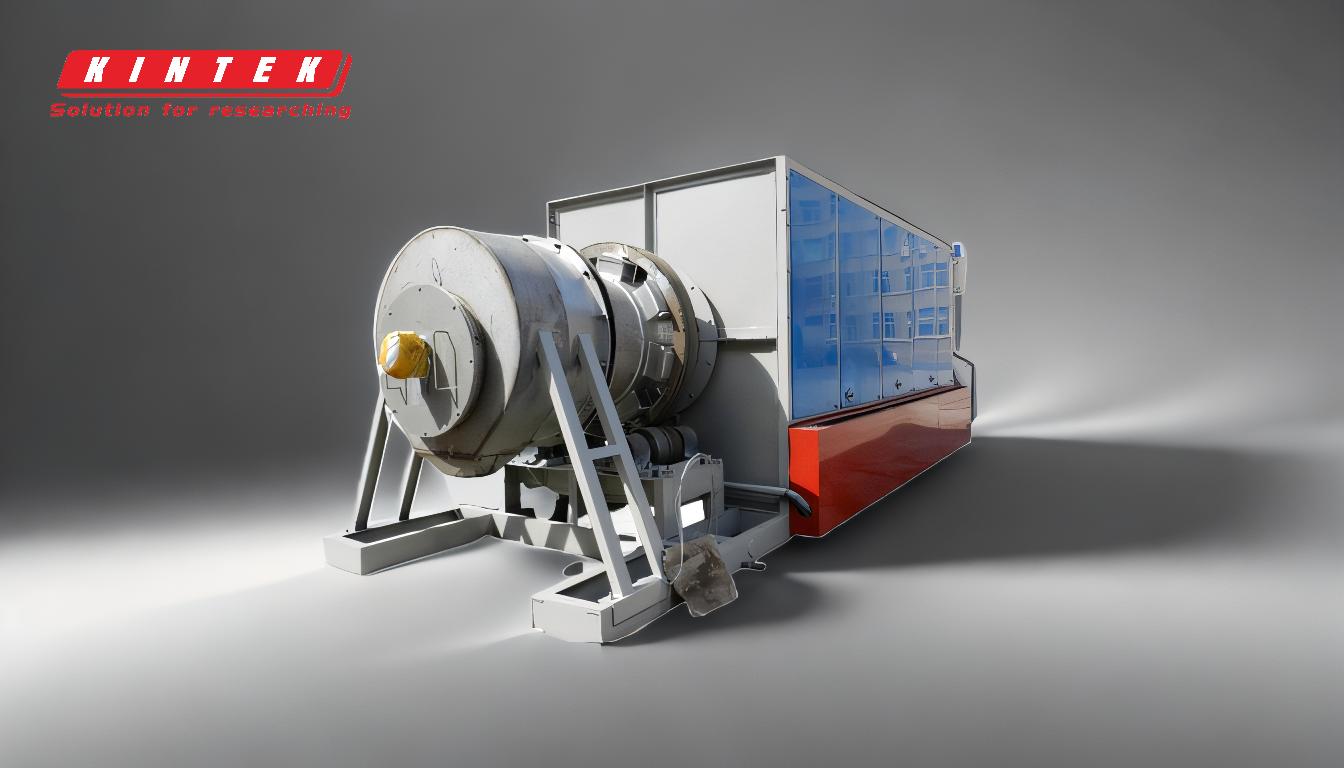
-
Definition and Purpose of Calcination:
- Calcination is a pyrometallurgical process that involves heating materials, such as metal ores or inorganic compounds, to high temperatures below their melting points in a controlled environment with limited air or oxygen.
- The primary purpose is to remove volatile impurities, such as water, carbon dioxide, sulfur dioxide, or other unwanted constituents, from the material.
- It is also used to chemically dissociate compounds, such as breaking down calcium carbonate (CaCO₃) into calcium oxide (CaO) and carbon dioxide (CO₂).
-
Applications of Calcination:
- Removal of Volatile Impurities: Calcination is used to eliminate absorbed moisture, carbon dioxide, sulfur dioxide, and other volatile components from materials.
- Chemical Dissociation: It helps break down complex compounds into simpler forms, such as converting calcium carbonate to calcium oxide, which is essential in cement production.
- Oxidation: Calcination can oxidize part or all of a substance, altering its chemical properties for specific industrial applications.
- Mineralization: In laboratories, calcination in muffle furnaces is used for the mineralization of plant samples, preparing them for analysis.
-
Industries and Materials Benefiting from Calcination:
- Metallurgy: Calcination is used to purify metal ores by removing volatile impurities, making the ores suitable for further processing.
- Ceramics and Cement Production: The dissociation of calcium carbonate into calcium oxide is a critical step in cement manufacturing.
- Chemical Manufacturing: Calcination is used to produce inorganic materials and remove bound moisture from compounds like borax.
- Laboratory Applications: Calcination is employed in sample preparation, such as mineralization of plant materials for analytical purposes.
-
Role of Calcination Furnaces:
- Calcination furnaces are specialized equipment designed to provide controlled heating environments for the calcination process.
- They ensure precise temperature control and limited oxygen exposure, which are critical for achieving the desired chemical and physical transformations.
- These furnaces are used across industries, including metallurgy, ceramics, and chemical manufacturing, to perform calcination efficiently.
-
Advantages of Calcination:
- Purification: It effectively removes impurities, making materials suitable for industrial use.
- Chemical Transformation: Calcination enables the dissociation of compounds, creating new materials with specific properties.
- Versatility: The process is applicable to a wide range of materials, including ores, inorganic compounds, and organic samples.
- Preparation for Further Processing: Calcination prepares materials for subsequent steps in manufacturing or analysis, such as smelting or chemical reactions.
-
Examples of Calcination in Practice:
- Cement Production: Heating limestone (calcium carbonate) to produce lime (calcium oxide) and carbon dioxide.
- Metallurgical Processing: Removing sulfur and other impurities from metal ores before smelting.
- Laboratory Analysis: Mineralizing plant samples to prepare them for elemental analysis.
In summary, calcination is a versatile and essential process in various industries, enabling the purification, chemical transformation, and preparation of materials for further use. Its applications range from metallurgy and cement production to laboratory analysis, making it a cornerstone of material science and industrial processes.
Summary Table:
Aspect | Details |
---|---|
Purpose | Remove volatile impurities and chemically dissociate compounds. |
Applications | Purification, chemical dissociation, oxidation, and mineralization. |
Industries | Metallurgy, ceramics, cement production, chemical manufacturing, and labs. |
Key Benefits | Purification, chemical transformation, versatility, and preparation. |
Examples | Cement production, metallurgical processing, and laboratory analysis. |
Learn how calcination can optimize your industrial processes—contact our experts today!