Heater wires are designed with high resistance to maximize heat production according to Joule's law, which states that heat generated (H) is proportional to the resistance (R) when current (I) and time (t) are constant. High resistance ensures efficient heat generation, which is essential for applications like heating elements in appliances. Additionally, heater wires must have a high melting point to withstand the high temperatures generated without melting. This combination of high resistance and high melting point ensures the wire can produce and sustain the necessary heat for its intended application.
Key Points Explained:
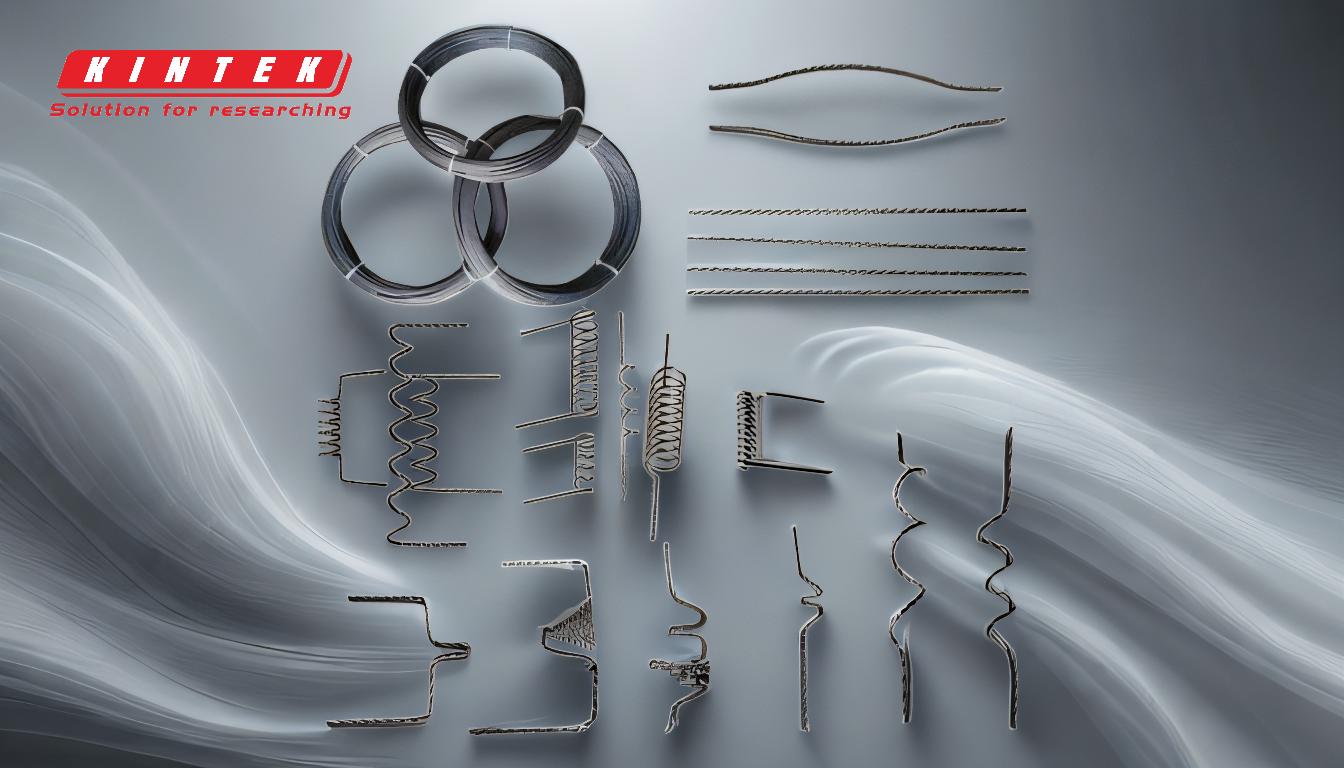
-
High Resistance for Heat Generation:
- Joule's Law: According to Joule's law, the heat produced (H) in a conductor is given by ( H = I^2 R t ), where ( I ) is the current, ( R ) is the resistance, and ( t ) is the time. For a given current and time, increasing the resistance ( R ) increases the heat produced. This is why heater wires are designed with high resistance—to maximize heat output efficiently.
- Series Circuit Principle: In a series circuit, the current remains constant throughout. Therefore, to generate more heat, the resistance of the wire must be high. This ensures that the wire can convert electrical energy into thermal energy effectively.
-
High Melting Point for Durability:
- Thermal Stability: Heater wires must have a high melting point to prevent them from melting or degrading when exposed to high temperatures. The high resistance of the wire leads to significant heat generation, and without a high melting point, the wire could fail under these conditions.
- Material Selection: Materials like nichrome (an alloy of nickel and chromium) are commonly used for heater wires because they combine high resistance with a high melting point. This ensures the wire can operate safely and reliably at elevated temperatures.
-
Controlled Current Flow:
- Temperature Regulation: While the high resistance of the wire ensures heat generation, a separate device (such as a thermostat) is often used to control the current flow. This device senses the temperature and adjusts the current to maintain the desired heat level, preventing overheating and ensuring safety.
- Energy Efficiency: By controlling the current, the system can optimize energy usage, ensuring that the heater wire operates efficiently without wasting electricity.
-
Applications of Heater Wires:
- Household Appliances: Heater wires are used in appliances like electric stoves, toasters, and hair dryers, where controlled heat generation is essential.
- Industrial Heating: In industrial settings, heater wires are used in furnaces, kilns, and other equipment that require consistent and reliable heat sources.
-
Trade-offs in Design:
- Resistance vs. Conductivity: While high resistance is desirable for heat generation, the wire must still conduct electricity effectively. Materials are chosen to balance these properties, ensuring the wire can generate heat without excessive energy loss.
- Safety Considerations: The design of heater wires must also account for safety, ensuring that the wire can handle the generated heat without posing a fire hazard or risk of electrical failure.
In summary, heater wires have high resistance to maximize heat production and a high melting point to ensure durability under high temperatures. These properties, combined with controlled current flow, make heater wires effective and reliable for a wide range of heating applications.
Summary Table:
Key Feature | Purpose |
---|---|
High Resistance | Maximizes heat production according to Joule's law (H = I²Rt). |
High Melting Point | Ensures durability and prevents melting under high temperatures. |
Controlled Current | Regulates temperature and optimizes energy efficiency. |
Material Selection | Uses alloys like nichrome for balanced resistance and conductivity. |
Applications | Used in household appliances (e.g., toasters) and industrial heating systems. |
Need reliable heater wires for your applications? Contact us today for expert solutions!