Physical vapor deposition (PVD) is conducted in a high vacuum to ensure the purity, quality, and precision of the deposited thin films. The high vacuum environment eliminates residual gases and contaminants that could interfere with the deposition process, ensuring that the material reaches the substrate with minimal obstruction. This environment also allows for a longer mean free path of the particles, reducing collisions and ensuring a more uniform and adherent film. Additionally, the vacuum minimizes contamination, provides a controlled and repeatable process, and is essential for applications requiring extremely clean environments, such as microchip manufacturing.
Key Points Explained:
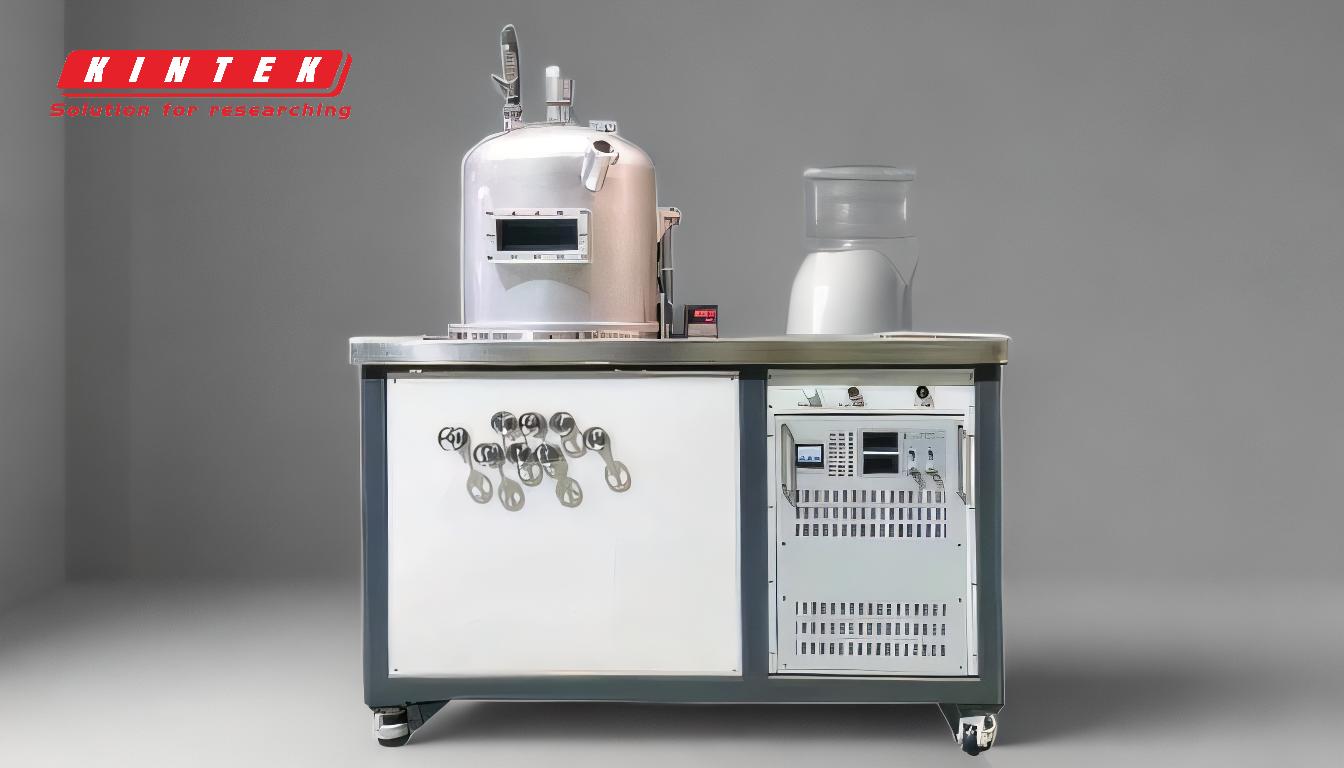
-
Elimination of Residual Gases and Contaminants:
- A high vacuum environment removes residual gases like oxygen, nitrogen, and carbon dioxide, which can interfere with the deposition process.
- These gases can obstruct the movement of film particles, weaken film adhesiveness, or cause unwanted chemical reactions.
- By reducing the presence of contaminants, a high vacuum ensures the formation of high-purity thin films.
-
Longer Mean Free Path:
- In a high vacuum, the mean free path of particles (the average distance a particle travels before colliding with another) is significantly increased.
- This reduces the likelihood of collisions between particles, allowing them to travel directly to the substrate without scattering.
- A longer mean free path is crucial for ensuring uniform and high-quality film deposition.
-
Enhanced Adhesion and Film Quality:
- The vacuum environment ensures that the material reaches the substrate with more energy, leading to stronger adhesion.
- Without air or other fluids to slow down the particles, they can bond more firmly to the substrate.
- This results in thin films with better mechanical and chemical properties.
-
Controlled and Repeatable Process:
- A high vacuum provides a controlled environment where variables like pressure and gas composition can be precisely managed.
- This repeatability is essential for industrial applications where consistency and quality are critical.
- It also allows for better mass flow control and the creation of low-pressure plasma environments, which are often used in PVD processes.
-
Reduction of Gaseous Contamination:
- The vacuum minimizes the density of undesirable atoms and molecules, reducing the risk of contamination.
- This is particularly important for applications like microchip manufacturing, where even trace amounts of contaminants can cause defects.
- A clean environment ensures the production of high-performance electronic components.
-
Thermal Evaporation Efficiency:
- In thermal evaporation PVD, a high vacuum ensures that the mean free path of evaporated atoms is much longer than the distance from the source to the target.
- This prevents scattering by residual gas molecules, ensuring that the atoms arrive at the substrate without losing energy.
- It also helps maintain clean surfaces, as evaporated atoms can stick more effectively to the substrate.
-
Applications Requiring Ultra-Clean Environments:
- Industries such as semiconductor manufacturing, optical coatings, and data storage (e.g., CDs and DVDs) require extremely clean environments.
- A high vacuum ensures that even the smallest particles are removed, preventing defects and ensuring the reliability of the final product.
By conducting PVD in a high vacuum, manufacturers can achieve thin films with superior purity, adhesion, and consistency, making it an essential process for advanced technological applications.
Summary Table:
Key Benefit | Description |
---|---|
Elimination of Residual Gases | Removes gases like oxygen and nitrogen, ensuring high-purity thin films. |
Longer Mean Free Path | Reduces particle collisions, ensuring uniform and high-quality deposition. |
Enhanced Adhesion and Film Quality | Particles bond firmly to the substrate, improving mechanical and chemical properties. |
Controlled and Repeatable Process | Ensures consistency and precision in industrial applications. |
Reduction of Gaseous Contamination | Minimizes contamination, critical for microchip manufacturing. |
Thermal Evaporation Efficiency | Prevents scattering, ensuring atoms reach the substrate without losing energy. |
Ultra-Clean Environments | Essential for semiconductor manufacturing, optical coatings, and data storage. |
Learn how high-vacuum PVD can enhance your manufacturing process—contact our experts today!