Nitrogen is extensively used in furnaces due to its inert properties, cost-effectiveness, and ability to create a controlled atmosphere that prevents oxidation and other unwanted chemical reactions. It serves as a protective gas in processes like annealing, sintering, and heat treatment, ensuring the integrity and quality of materials such as metals, semiconductors, and steel products. Nitrogen's high diffusion rate and faster cooling capabilities make it a preferred choice over other gases like argon. Additionally, it is widely used in vacuum furnaces as a cooling medium due to its safety, affordability, and cleanliness. Overall, nitrogen plays a critical role in maintaining process efficiency and product quality in high-temperature furnace applications.
Key Points Explained:
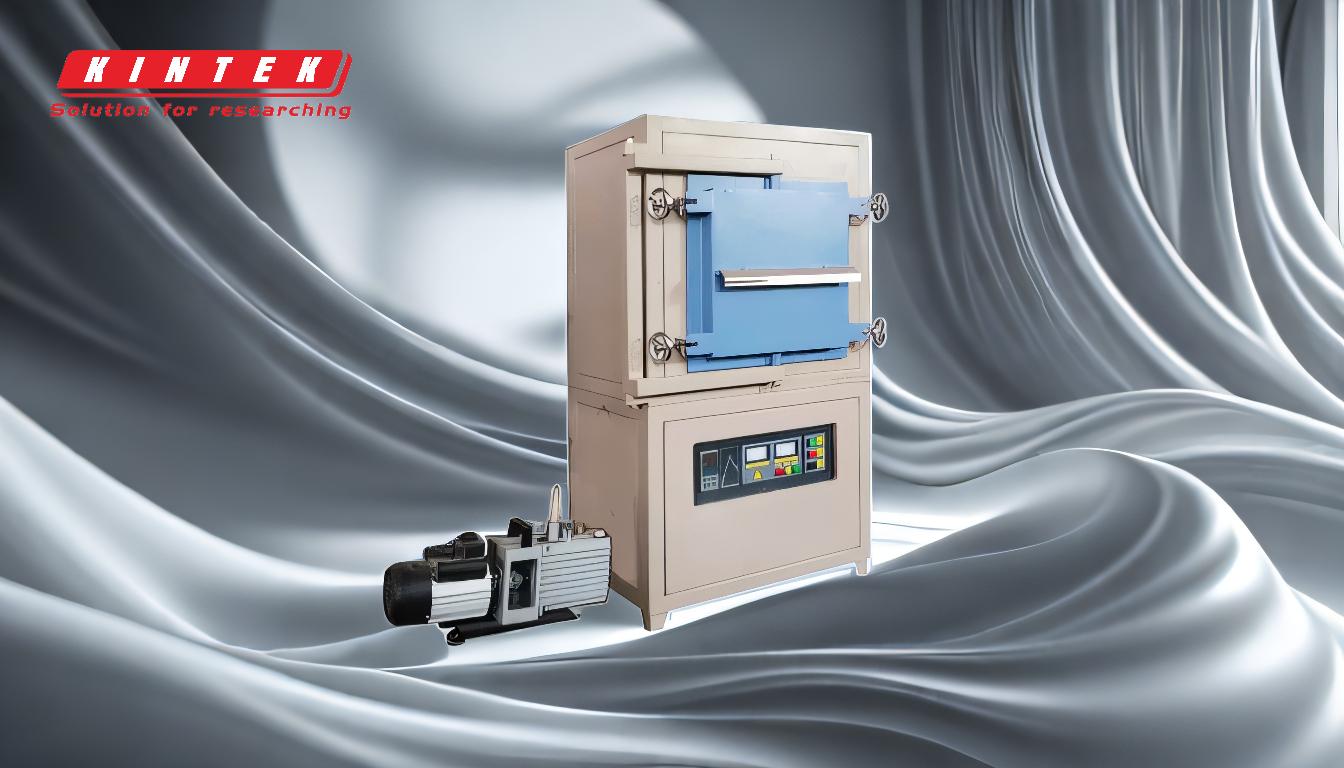
-
Prevention of Oxidation
- Nitrogen is an inert gas, meaning it does not readily react with other substances, particularly metals.
- In high-temperature furnaces, oxidation of materials like ferrous metals can degrade their quality. Nitrogen creates a protective barrier, isolating oxygen from the metals and preventing oxidation reactions.
- This is especially important in processes like annealing, sintering, and heat treatment, where maintaining material integrity is crucial.
-
Cost-Effectiveness
- Nitrogen is significantly cheaper than other inert gases like argon, making it a cost-effective choice for industrial applications.
- The use of nitrogen generators further reduces costs by providing a continuous supply of nitrogen at a lower expense compared to purchasing bottled gas.
- Its affordability makes it accessible for large-scale industrial processes without compromising performance.
-
Faster Cooling Rates
- Nitrogen has a cooling rate approximately four times faster than argon, making it highly effective for cooling applications in furnaces.
- This property is particularly useful in vacuum furnaces, where rapid cooling is often required to achieve desired material properties.
- The faster cooling rate also improves process efficiency, reducing cycle times and energy consumption.
-
Inert Atmosphere Creation
- Nitrogen is widely used to create an inert atmosphere in furnaces, reducing reaction rates and oxidation potentials.
- This is achieved through a process called nitrogen blanketing, where nitrogen is introduced into the furnace chamber via gas inlets like flowmeters, and spent gas is expelled through an exhaust port.
- Electronic monitoring systems are often employed to maintain precise nitrogen levels, ensuring optimal conditions for the process.
-
Applications in Various Industries
- Nitrogen is used in a wide range of industries, including metal heat treatment, powder metallurgy, magnetic materials, copper processing, and semiconductor manufacturing.
- In reflow ovens, nitrogen improves the wettability of welding surfaces and reduces oxidation, enhancing the quality of solder joints.
- Its versatility and effectiveness make it a staple in high-temperature processing environments.
-
Safety and Cleanliness
- Nitrogen is a relatively safe gas to handle, with minimal risks of combustion or toxicity.
- It is also sufficiently clean for use in sensitive processes, with permissible impurity levels as low as 2 ppm of oxygen and 5-10 ppm of water by volume.
- This ensures that the materials being processed are not contaminated, maintaining high standards of quality and consistency.
-
Decarburization Prevention
- In steel processing, nitrogen blanketing can prevent decarburization, a process where carbon is lost from the surface of steel, weakening its structure.
- By maintaining a nitrogen-rich environment, the carbon content of steel products is preserved, ensuring their strength and durability.
-
Process Efficiency and Control
- The use of nitrogen allows for precise control over furnace atmospheres, enabling manufacturers to achieve consistent results.
- Its high diffusion rate ensures even distribution within the furnace chamber, minimizing hotspots and ensuring uniform treatment of materials.
- This level of control is essential for meeting stringent quality standards in industries like aerospace, automotive, and electronics.
By leveraging nitrogen's unique properties, industries can optimize their furnace processes, reduce costs, and enhance the quality of their products. Its role in preventing oxidation, enabling rapid cooling, and creating inert atmospheres makes it an indispensable tool in modern manufacturing and material processing.
Summary Table:
Key Benefit | Description |
---|---|
Prevention of Oxidation | Creates a protective barrier to prevent oxidation in metals and other materials. |
Cost-Effectiveness | Cheaper than argon; nitrogen generators reduce operational costs. |
Faster Cooling Rates | Cools materials 4x faster than argon, improving efficiency. |
Inert Atmosphere Creation | Reduces reaction rates and oxidation potentials in furnace processes. |
Applications in Industries | Used in metal heat treatment, semiconductors, and more. |
Safety and Cleanliness | Safe, non-toxic, and clean for sensitive processes. |
Decarburization Prevention | Preserves carbon content in steel, ensuring strength and durability. |
Process Efficiency | Enables precise control and uniform treatment of materials. |
Optimize your furnace processes with nitrogen—contact our experts today to learn more!