Introduction
Table of Contents
In the world of metal powders processing, two common methods are used for compaction: hot pressing and cold pressing. These techniques play a crucial role in creating high-quality metal components. Hot pressing involves the merging of discrete powder metallurgical stages into a single chamber, where compaction and sintering occur simultaneously. On the other hand, cold pressing utilizes a different approach by applying pressure without the use of heat. In this blog post, we will delve deeper into the characteristics, benefits, and outcomes of both hot and cold pressing methods, providing insights into their applications and advantages in the metalworking industry.
Hot Pressing Method in Compaction Chamber
Description of hot pressing process
Hot pressing involves pressing and sintering a powder part in a single step. The force of the die compacts the powder, at the same time heat is being applied to the work. Good mechanical properties and dimensional accuracy can be achieved with this manufacturing process. A controlled atmosphere should be maintained for hot pressing. Mold materials must be capable of holding integrity under the conditions of extreme temperature and pressure that this process requires.

Process of merging discrete powder metallurgical stages
Two of the discrete powder metallurgical stages can be combined. This is hot pressing, with the compaction work and sintering operation done in one chamber. First, the die creates the Green part, which is still a mass of individual metal particles. Next, the grains "neck" and sinter. The elevated temperature is held just below the critical melting point of the selected alloy, so the particles combine. There's no liquidizing, no melting metals flowing. Again, two separate sources of energy are utilized inside a single chamber. Immense pressures give the powder its geometry, then the applied thermal energy encourages the compacted powder to coalesce.
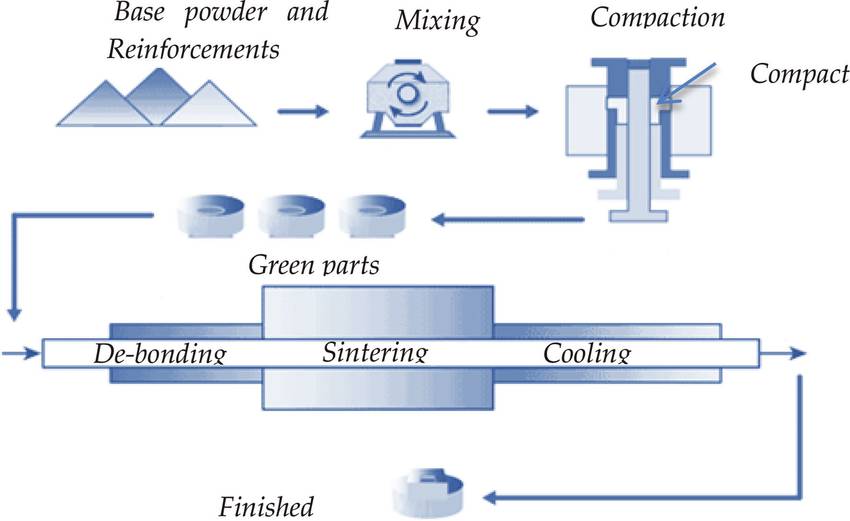
Mechanism of compaction and sintering in a single chamber
Hot press compaction/sintering chambers are used to produce densified tools. Pressed into heat-distributing graphite dies, the thermal energy and compaction process improves the sintering characteristics of metal powders that would otherwise resist the process. By combining the two stages, low-porosity, densified carbide cutting tools can be produced in quantity within a machine form that wasn't originally intended for such purposes. Alternatively, when it comes to cold pressing, the two discrete forming stages produce geometrically detailed products, which exhibit a calculated porosity quotient, plus some kind of an internally stored fluid/wax. Lubricating oils are popularly stored inside self-lubricating bearings in this manner.
Hot Pressing vs. Cold Pressing of Metal Powders: What's the Difference?
Back at the compaction chamber, two alternative pressing systems are available. In the hot pressing method, elevated temperatures are used. It's a dual-process operation, with the powdered metal compacting, then it sinters. Almost solid, just slightly porous, the combined processing approach yields tool quality results. Alternatively, cold pressing is done without heat. That latter phase of the process is left until the compacted product reaches the sintering stage.
Cold Pressing Method in Compaction Chamber
Description of cold pressing process
Cold pressing is a method used in compaction chambers to produce geometrically detailed products with a calculated porosity quotient. Unlike hot pressing, cold pressing does not involve the application of heat to transform the green compact into a solid mass. Instead, high pressures are applied in the compaction chamber, where upper die sections and their lower components come together. A core element and a feeder shoe complete the die architecture. The compaction chamber may undergo a low-temperature bake to burn off the pressing lubricant.
Contrast with hot pressing in terms of heat application
Hot pressing, on the other hand, utilizes elevated temperatures in a dual-process operation. The powdered metal is first compacted and then sinters. The heat encourages the compacted powder to coalesce, resulting in a nearly solid and slightly porous product. The combination of compaction and sintering in one chamber yields tool-quality results. In contrast, cold pressing does not involve any heating elements and the sintering process is carried out separately after compaction.
Differences in die architecture between hot and cold pressing
The die architecture also differs between hot and cold pressing. In hot pressing, graphite cores are used to replace the hardened steel variants found in cold pressing. This difference in die architecture is necessary to accommodate the heat application in hot pressing, as graphite is a better conductor of heat compared to steel.
Overall, both hot and cold pressing methods have their own benefits and applications. Hot pressing is suitable for producing densified tools with improved sintering characteristics, while cold pressing is ideal for producing geometrically detailed products with a calculated porosity quotient. Additionally, cold pressing can be combined with other processes such as cold isostatic pressing, which applies pressure uniformly over the entire surface of the mold and results in more uniform densities.
Cold pressing method in compaction chambers offers a versatile approach to producing high-quality products using powder metallurgy techniques.
Benefits of Hot and Cold Pressing Methods
Production of densified tools using hot press compaction
Hot press compaction/sintering chambers are used to produce densified tools. This method involves applying compaction pressure and thermal energy to metal powders pressed into heat-distributing graphite dies. The combination of pressure and heat improves the sintering characteristics of the metal powders, resulting in low-porosity, densified carbide cutting tools. This technique allows for the production of high-quality tools in large quantities within a machine form that was not originally intended for such purposes.

Improved sintering characteristics with combined stages
Hot pressing combines the compaction and sintering stages into one chamber. First, the die creates the green part, which is a mass of individual metal particles. Then, the grains "neck" and sinter under elevated temperatures just below the critical melting point of the alloy. This process encourages the particles to combine and coalesce without melting metals flowing. By utilizing two separate sources of energy in a single chamber, hot pressing achieves improved sintering characteristics and the production of products with fine grains and good mechanical and electrical properties.
Special characteristics of products produced through cold pressing
Cold pressing is a technique that does not involve heat during the compaction stage. Instead, the compacted product is sintered separately. This method is used to create finely detailed components with predetermined voids, capillary pathways, and lubricating fluids. The products produced through cold pressing exhibit a calculated porosity quotient and internally stored fluid/wax, such as lubricating oils stored inside self-lubricating bearings. Cold pressing offers the advantages of greater flexibility in shape and size, longer aspect ratios, improved compaction of powder, and the ability to process materials with different characteristics and shapes.
In conclusion, both hot and cold pressing methods have their unique advantages in the production of densified tools and components. Hot press compaction improves sintering characteristics and allows for the production of high-quality tools in large quantities. On the other hand, cold pressing offers greater flexibility in shape and size, as well as the ability to create finely detailed components with predetermined characteristics. Understanding the differences between these two methods is essential for selecting the most appropriate technique for specific manufacturing requirements.
Outcome Comparison between Hot and Cold Pressing Techniques
Strength and density improvements with hot pressing
Hot pressing techniques are known for their ability to remove potential material weaknesses, resulting in stronger and denser parts. As the porosity quotient drops, the finished product becomes more robust. This makes hot pressing a preferred method for creating specialized items such as sintered carbide tools. The process involves using a single chamber that applies compaction pressure and thermal energy to achieve the desired outcome.

Creation of specialized items with single chamber technique
Hot pressing techniques, performed in a single chamber, offer the advantage of creating specialized items with improved strength and density. This method is commonly used for manufacturing sintered carbide tools and other specialized components. By applying compaction pressure and thermal energy in a controlled environment, hot pressing ensures the production of high-quality components.
Production of finely detailed components through cold pressing
Cold pressing techniques are used to create finely detailed components with predetermined voids, capillary pathways, and lubricating fluids. The components produced through cold pressing may appear solid but possess these unique properties. This method is widely used in various industries such as mobile phone manufacturing, touch screen manufacturing, computer manufacturing, printer manufacturing, and membrane switch manufacturing.

Unique properties of components produced through cold pressing
Components produced through cold pressing have several unique properties. They possess predetermined voids, capillary pathways, and lubricating fluids, even though they may appear solid. This allows for greater flexibility in the shape and size of the finished product. Cold pressing also enables the production of components with longer aspect ratios, making it possible to create long and thin pellets. Additionally, cold pressing allows for improved compaction of the powder, leading to better densification of the final product. This method also offers the ability to process materials with different characteristics and shapes, resulting in components with enhanced properties.
In summary, both hot pressing and cold pressing techniques have their own advantages and are used for different purposes. Hot pressing is favored for its strength and density improvements, while cold pressing is preferred for creating finely detailed components with unique properties. The choice between the two techniques depends on the specific goals of the project and the characteristics of the materials involved.
Conclusion
In conclusion, both hot pressing and cold pressing methods have their own advantages and applications in metal powders processing. Hot pressing offers the benefits of producing densified tools, improved sintering characteristics, and the ability to merge compaction and sintering stages in a single chamber. On the other hand, cold pressing allows for the production of finely detailed components and offers unique properties in the final products. Choosing between the two techniques depends on the desired outcome and specific requirements of the project. Understanding the differences and capabilities of each method is essential for achieving optimal results in metal powders processing.
CONTACT US FOR A FREE CONSULTATION
KINTEK LAB SOLUTION's products and services have been recognized by customers around the world. Our staff will be happy to assist with any inquiry you might have. Contact us for a free consultation and talk to a product specialist to find the most suitable solution for your application needs!