Introduction
Table of Contents
In the rubber industry, laboratory presses play a crucial role in the manufacturing process. These presses are used for various purposes, such as rubber vulcanization and testing. Understanding how laboratory presses function is essential for ensuring efficient production and maintaining product quality. In this blog post, we will explore the functionality of laboratory presses in the rubber industry, including their role in the vulcanization process. Additionally, we will compare different types of laboratory presses and discuss their advantages. So, let's dive in and unravel the world of laboratory presses in the rubber industry!
What is Laboratory Press?
A laboratory press is a device used to press different kinds of sample materials, such as rubbers, polymers, and composites. These presses are commonly used in industries such as pharmaceuticals, laminating, rubber and plastic molding for various purposes such as R&D work, testing, short runs, limited production, cell manufacturing, and lean manufacturing.
Explanation of Laboratory Press DW5150A/DW5150B
The Laboratory Press DW5150A/DW5150B is mainly used for vulcanizing flat tape and applying hot plate pressure per unit area. It is known for its reliable equipment operation and low maintenance requirements. This laboratory press is essential for creating compressed pellets out of powdered materials for applications like pharmaceutical development, spectroscopy, and bomb calorimetry. The press can generate a wide range of pressures, from 15 to 200 metric tons, and some models can accommodate different-sized or customized dies.
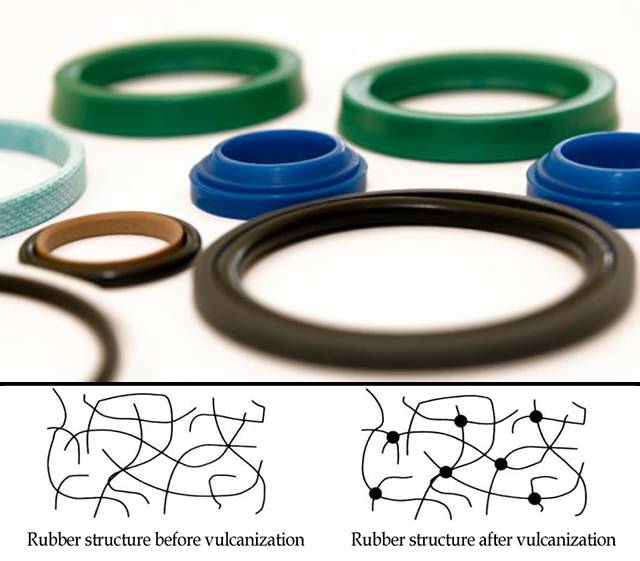
Role of Rubber Vulcanizing Press
Rubber Vulcanizing Press is a type of laboratory press used in the rubber industry. Its main function is to provide the necessary vulcanization pressure and temperature. The hydraulic system generates pressure through a hydraulic cylinder, while the heating medium provides the required temperature. Rubber Vulcanizing Press can be categorized into single and double points based on the working layer number, and the hydraulic system can use oil pressure or water pressure as the working medium.
Comparison between column rubber laboratory Press and frame structure
In the rubber industry, there are two main types of laboratory presses: column rubber laboratory Press and frame structure. The column rubber laboratory Press is an early type of machine, and it was commonly used in China in the past. However, the frame structure is now more widely adopted due to its advantages over the column flat plate vulcanizing machine. The frame flat plate vulcanizing machine offers certain advantages such as reliable equipment operation and low maintenance requirements.
Overall, laboratory presses play a crucial role in research and industrial inquiries by providing precision, durability, and the ability to meet rigorous demands. These heavy-duty machines are essential for testing and compacting materials like rubber, plastic, and laminate materials, and they ensure consistent and long-lasting results in the laboratory.
Working Principle of Laboratory Press
Heat application and structuring process
A laboratory press works by applying heat and pressure to a sample to compress or compact it. The heat is used to size up the hot plate, which then heats the sample. As the sample is heated, the cross-linked rubber molecules and its structure transform from a linear structure to a mesh structure. This results in the sample having a range of physical and mechanical properties. The heat also softens the rubber and causes any moisture and volatile matter within the rubber to gasify. The hydraulic cylinder then applies enough pressure to mold the rubber and prevent the formation of air bubbles. This process creates a fine and close organizational structure in the sample, ensuring its consistency and quality.
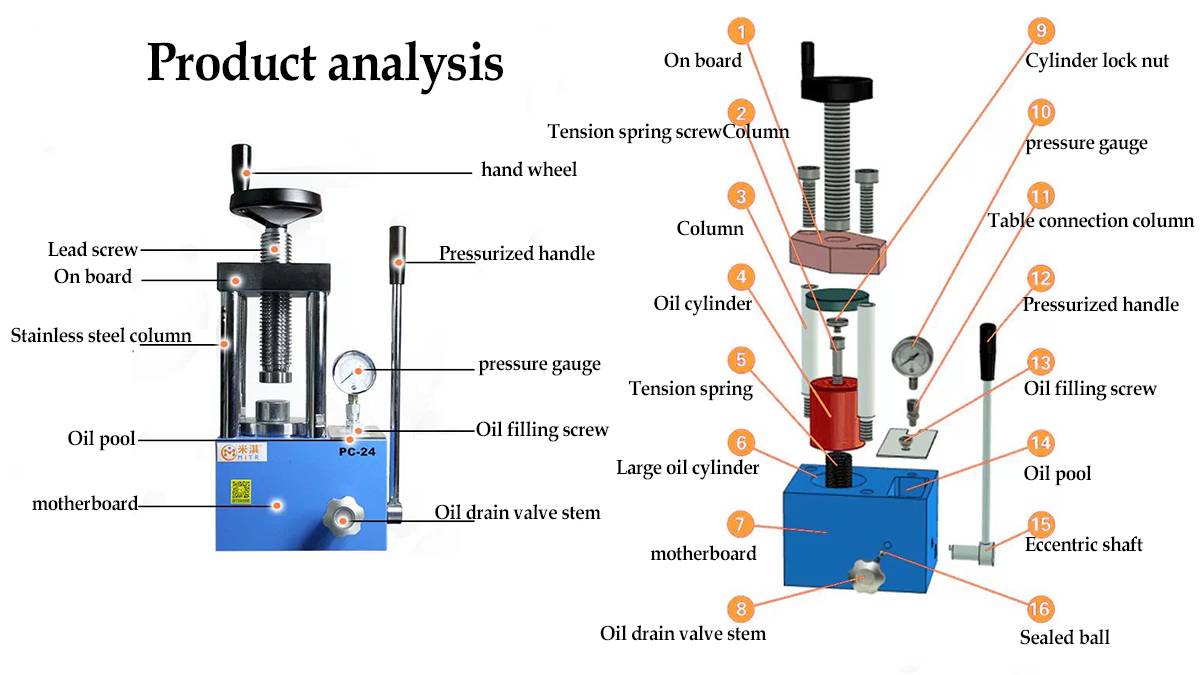
Role of hydraulic cylinder in pressure application
The hydraulic cylinder plays a crucial role in the pressure application of a laboratory press. It is responsible for providing sufficient pressure to the sample to mold it and prevent overflow, lack of glue, or other unwanted phenomena. The hydraulic cylinder works by using Pascal's law, which states that when pressure is applied to a confined fluid, the pressure change occurs throughout the entire fluid. In the case of a laboratory press, the hydraulic cylinder uses oil as the confined fluid and transmits the pressure evenly to the sample. This ensures that the pressure applied to the sample is consistent and results in the desired compression or compaction.
Effects of sufficient pressure
Applying sufficient pressure in a laboratory press is essential for achieving the desired results. Sufficient pressure ensures that the sample is properly molded and that the structure is fine and close. It also prevents overflow at the edges of the mold, lack of glue in patterns, and the formation of air bubbles. By applying enough pressure, the laboratory press can produce samples with reproducible characteristics and consistent thickness.
In conclusion, the working principle of a laboratory press involves the application of heat and pressure to a sample. The heat causes the sample to undergo a structuring process, transforming its molecular structure. The hydraulic cylinder then applies sufficient pressure to mold the sample and prevent any unwanted phenomena. This working principle ensures that laboratory presses can produce high-quality samples with consistent characteristics.
Features of Rubber Laboratory Press
Material and design of pressing plates
- All four pressing plates are made of SKD chromium-molybdenum alloy.
- The surface is treated by high frequency, carburizing, chromium plating, and polishing, with a hardness of up to 60HRC.
- Four high-strength precision guide columns are designed with double layers of high-strength laminate clamping structures.
- The heavy structural steel of the frame can effectively reduce deformation and damage.
- The parallelism between the laminate plates is extremely high.
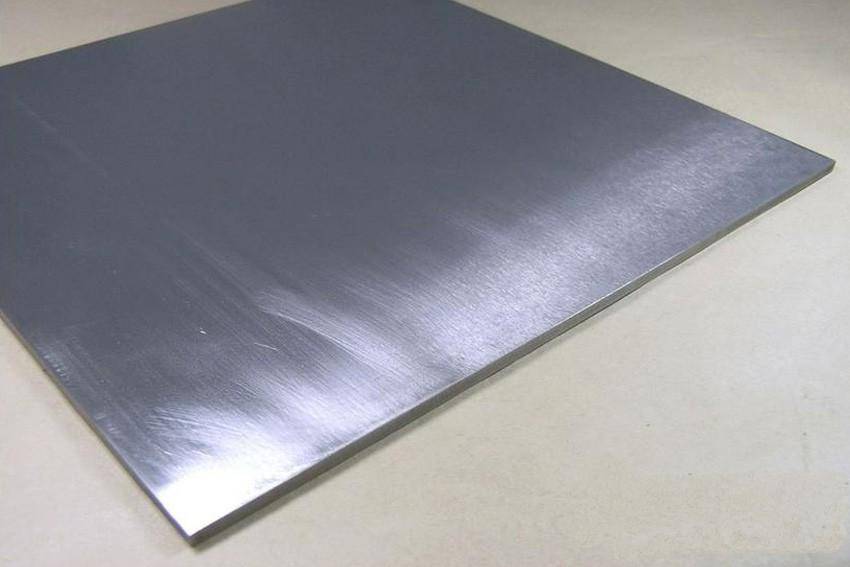
Heating control technology
- The patented heating control technology is equipped with imported high-precision PID digital temperature control display.
- The heat transfer pipe, according to the heat density distribution, can ensure uniform temperature distribution on the heating plate surface.
Molded board division and functionalities
- The laboratory platen press allows for easy switching between different sample types and materials.
- It is used to prepare samples for R&D and quality tests in various industries and material categories such as rubbers, polymers, composites, ceramics, wood, thermoplastic resins, textiles, laminating, and pharmaceutical applications.
Hydraulic system features
- The hydraulic system has a closure force of 25 tons.
- It includes a hydraulic balance device, making the machine movement more stable and quick.
Electrical control system standards
- The control panel is automated and easy to operate, saving labor costs.
- Well-known electronic components are used for stability and long-term use.
Working of Rubber Laboratory Press
Preparation process
Before using a rubber laboratory press, there are some essential preparation steps to be followed:
-
Check hydraulic oil quantity: Verify the hydraulic oil level before use. The oil height should be at least 2/3 of the height of the lower frame. If the oil quantity is low, it needs to be topped up in a timely manner.
-
Inspect lubrication: Ensure proper lubrication between the column shaft and the guide frame. If necessary, apply lubricant to maintain smooth operation.
-
Power supply operation: Switch on the power supply and adjust the position to vertical. Close the oil return port using the operating handles. Press the motor start button to initiate the oil pumping process.
Hydraulic oil
Inspection of hydraulic oil quantity and lubrication
To ensure smooth operation of the rubber laboratory press, it is crucial to regularly inspect the hydraulic oil quantity and lubrication.
-
Hydraulic oil quantity: The hydraulic oil level should be maintained at around 2/3 of the height of the lower frame. Insufficient oil quantity can affect the pressurization process.
-
Lubrication: Check the lubrication between the column shaft and the guide frame. Apply lubricant as needed to maintain proper functioning and prevent friction-related issues.
Operation of power supply
Proper operation of the power supply is essential for the effective working of a rubber laboratory press.
-
Vertical position: Adjust the position of the press to vertical before starting the power supply. This ensures the press operates in a stable and efficient manner.
-
Closing the oil return port: Use the operating handles to close the oil return port. This allows the oil pump to function properly and maintain consistent pressure during the working process.
-
Motor start button: Press the motor start button to initiate the oil pumping process. The oil is pumped from the oil pump into the oil cylinder, causing the plunger to move up and generate pressure.
Hydraulic cylinder
Application of plate vulcanizing machine
The plate vulcanizing machine is a key component of the rubber laboratory press. It plays a crucial role in the vulcanization process.
-
Working principle: The plate vulcanizing machine provides the necessary vulcanization pressure and temperature. The hydraulic system generates pressure through the hydraulic cylinder, while the heating medium controls the temperature. This process allows the rubber to undergo cross-linking, transforming its structure and enhancing its physical and mechanical properties.
-
Advantages of frame structure: The frame structure of the plate vulcanizing machine offers certain advantages over the column structure. It provides better stability and allows for fine and close organizational structures. Additionally, it helps prevent issues such as overflow, lack of glue, and the presence of air bubbles.
By following the proper preparation process, inspecting hydraulic oil quantity and lubrication, ensuring the correct operation of the power supply, and understanding the application of the plate vulcanizing machine, you can ensure the efficient and reliable working of a rubber laboratory press.
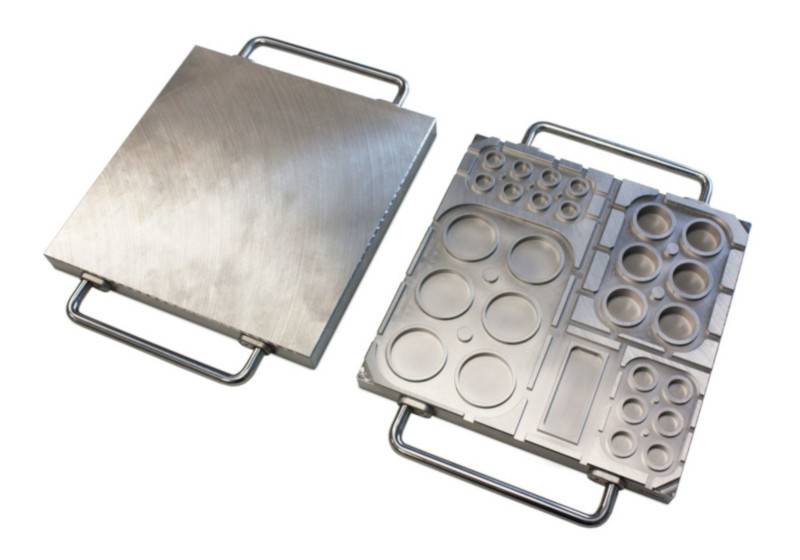
Hydraulic System
Quality of hydraulic oil
The hydraulic oil used in KINTEK presses is specially formulated to have good thermal and chemical stability. It undergoes industry-standard ASTM D 943 TOST test to ensure reliability and cleanliness of the system. The oil minimizes sludge formation and provides excellent performance.
However, it is important to note that the hydraulic oil in the laboratory platen presses is never used at the operating temperature of 60°C. As a result, the degree of moisture increases, leading to increased compressibility and the risk of corrosion. It is recommended to change the hydraulic oil regularly to maintain optimal performance and prevent potential issues.
Importance of cleanliness and lubrication
The hydraulic oil in a hydraulic system plays a crucial role in lubricating the various components, such as the hydraulic pump, motor, manifold, hydraulic cylinder, and pipes. Regular maintenance and lubrication of these components are essential to ensure smooth operation and prevent premature wear and tear.
It is important to check the lubrication between the column shaft and the guide frame regularly and refill as needed to maintain good lubrication operation. Proper lubrication helps reduce friction, noise, and heat generation, extending the lifespan of the hydraulic system.
Temperature control of hot plate
In a hydraulic lab press, the hot plate is responsible for heating the plates used for vulcanization. The temperature control of the hot plate is crucial to achieve the desired curing temperature for different materials. The hydraulic press utilizes electric heating technology with precise temperature control.
The temperature can be adjusted within a range of 20-200 degrees Celsius, and once the set temperature is reached, the circuit automatically maintains a constant temperature. This ensures accurate and consistent curing of the rubber or other materials being processed.
Control of vulcanization motor
The vulcanization motor in a hydraulic press is responsible for applying pressure to the material during the curing process. It is essential to have proper control over the motor to ensure accurate pressure application and prevent motor overload.
The control system of the hydraulic press includes features such as automatic pressure compensation, delay stop, and pressure keeping. It allows for setting multiple pressure levels and displays, as well as customizable exhaust actions. The optimized electro-hydraulic drive combination design reduces energy consumption while improving efficiency.
Overall, the hydraulic system in a lab press plays a critical role in ensuring the quality and efficiency of the vulcanization process. Regular maintenance, including changing the hydraulic oil and proper lubrication, is necessary to extend the lifetime of the hydraulic system and maximize its performance.
Conclusion
In conclusion, understanding the functionality of laboratory press in the rubber industry is crucial for ensuring efficient production processes. The laboratory press, such as the DW5150A/DW5150B models, plays a vital role in the vulcanization of rubber. By applying heat and pressure through the hydraulic cylinder, it facilitates the molding and shaping of rubber products. The features of rubber laboratory press, including the material and design of pressing plates, heating control technology, and hydraulic system features, further enhance its performance. Additionally, proper maintenance of the hydraulic system, including the quality of hydraulic oil, cleanliness, lubrication, and temperature control, is essential for optimal operation. Overall, laboratory press is a valuable tool that contributes to the success of the rubber industry.
If you are interested in this product you can browse our company website:https://kindle-tech.com/product-categories/heated-lab-press, we always insist on the principle of quality first. During the production process, we strictly control every step of the process, using high quality materials and advanced production technology to ensure the stability and durability of our products. to ensure that their performance meets the highest standards. We believe that only by providing customers with excellent quality can we win their trust and long-term cooperation.
CONTACT US FOR A FREE CONSULTATION
KINTEK LAB SOLUTION's products and services have been recognized by customers around the world. Our staff will be happy to assist with any inquiry you might have. Contact us for a free consultation and talk to a product specialist to find the most suitable solution for your application needs!