Heating elements do lose power over time due to several factors, including oxidation, elongation, and changes in resistance. These factors are influenced by operating conditions such as temperature, atmosphere, watt density, and usage patterns. Over time, the resistance of the heating element increases, leading to a reduction in power output and eventual failure. This is a natural part of the element's lifecycle, and manufacturers account for these variables when designing and warranting their products.
Key Points Explained:
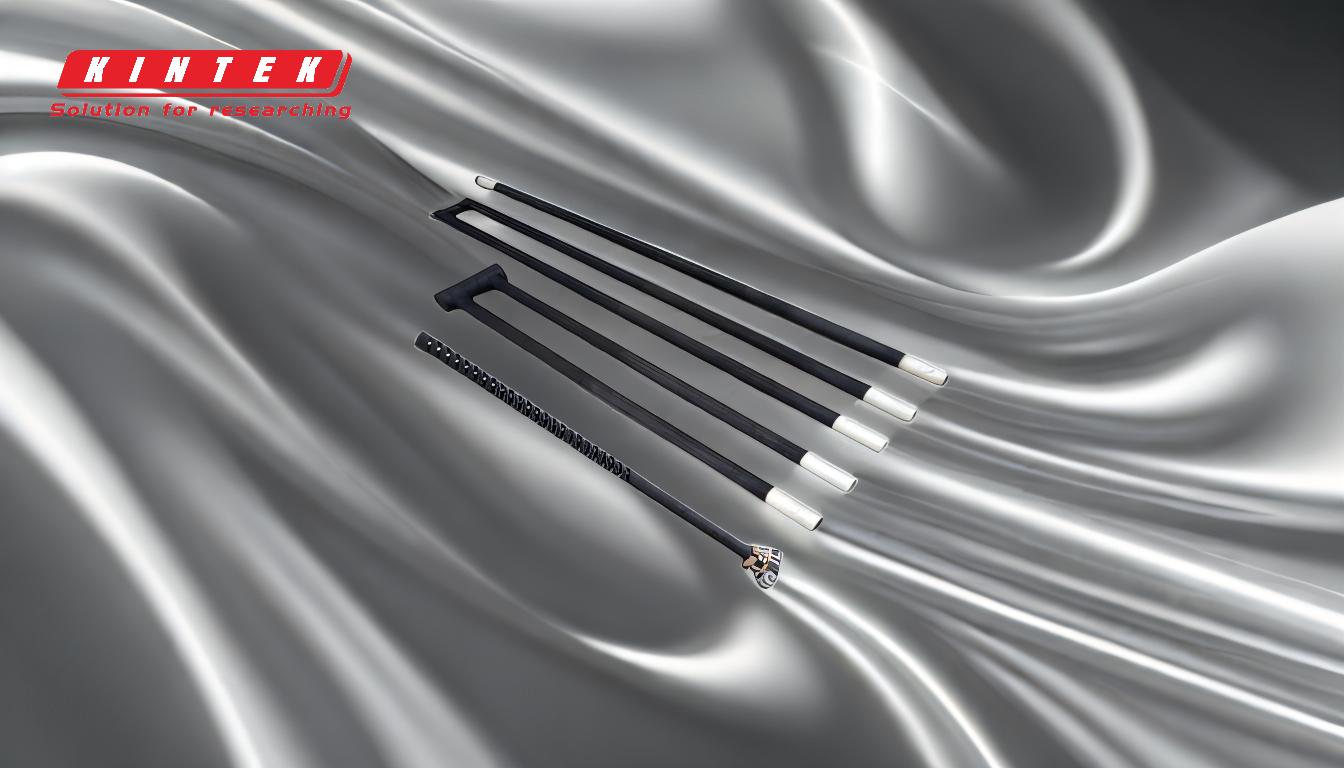
-
Resistance Increases Over Time:
- As heating elements age, their resistance increases due to oxidation, which reduces the cross-sectional area of the element. This oxidation process is inevitable and occurs faster in certain environments, such as high-temperature or reducing atmospheres.
- Additionally, elongation of the heating element loops contributes to increased resistance. This elongation happens as the material expands and contracts during heating and cooling cycles.
-
Impact on Power Output:
- The increase in resistance directly affects the power output of the heating element. According to Ohm's Law (P = V²/R), as resistance (R) increases, the power (P) delivered to the furnace decreases for a given voltage (V).
- This reduction in power can lead to inefficient heating and longer cycle times, ultimately affecting the performance of the furnace or heating system.
-
Factors Influencing Element Life:
- Furnace Atmosphere: Elements operating in reducing atmospheres or environments with high levels of oxygen or other reactive gases tend to oxidize faster, shortening their lifespan.
- Watt Density: Higher watt densities place more stress on the heating element, accelerating wear and tear.
- Operating Temperature: Higher temperatures increase the rate of oxidation and material degradation.
- Usage Patterns: Continuous service or frequent heating and cooling cycles can lead to faster degradation compared to intermittent use.
- Maintenance: Regular maintenance, such as cleaning and inspecting the elements, can help extend their life by identifying and addressing issues early.
-
Material-Specific Considerations:
- Silicon Carbide Elements: These elements are particularly sensitive to furnace atmosphere and watt density. Their life expectancy is influenced by the operating environment and the frequency of thermal cycling.
- Ceramic Elements: The properties of ceramic heating elements are affected by alloy composition, dimensions, watt loading, and device architecture. These factors determine how the element responds to thermal and mechanical stresses over time.
-
Normal Lifecycle and Failure:
- The gradual increase in resistance and eventual failure of heating elements is considered a normal part of their lifecycle. Manufacturers design elements with these factors in mind and provide warranties that cover manufacturing defects but not wear and tear due to operational conditions.
- When an element fails, it is typically due to a combination of factors, including oxidation, elongation, and increased resistance, which collectively reduce its power output to a point where it can no longer function effectively.
-
Mitigation Strategies:
- To prolong the life of heating elements, users can:
- Operate the furnace or heating system within recommended temperature and watt density limits.
- Minimize rapid heating and cooling cycles.
- Use protective atmospheres or coatings to reduce oxidation.
- Perform regular maintenance to identify and address issues before they lead to failure.
- To prolong the life of heating elements, users can:
In summary, heating elements do lose power over time due to increased resistance caused by oxidation, elongation, and other operational factors. Understanding these factors and implementing strategies to mitigate their effects can help extend the life of heating elements and maintain efficient furnace operation.
Summary Table:
Key Factors | Impact on Heating Elements |
---|---|
Resistance Increase | Oxidation and elongation reduce cross-sectional area, increasing resistance and lowering power. |
Furnace Atmosphere | High oxygen or reactive gases accelerate oxidation, shortening lifespan. |
Watt Density | Higher watt densities stress elements, leading to faster wear and tear. |
Operating Temperature | Higher temperatures increase oxidation and material degradation rates. |
Usage Patterns | Frequent heating/cooling cycles degrade elements faster than intermittent use. |
Maintenance | Regular cleaning and inspection can identify issues early, extending element life. |
Need help maintaining or replacing your heating elements? Contact our experts today for tailored solutions!