A two-stage furnace can indeed save money over time, primarily through reduced fuel and power consumption, leading to lower operating costs. These furnaces operate more efficiently by adjusting their output to match the heating demand, which results in more consistent temperatures and less energy waste. Additionally, their design reduces wear and tear, minimizing the likelihood of frequent repairs or premature replacement. While the upfront cost may be higher compared to single-stage furnaces, the long-term savings on energy bills and maintenance can make them a cost-effective choice for homeowners seeking efficiency and comfort.
Key Points Explained:
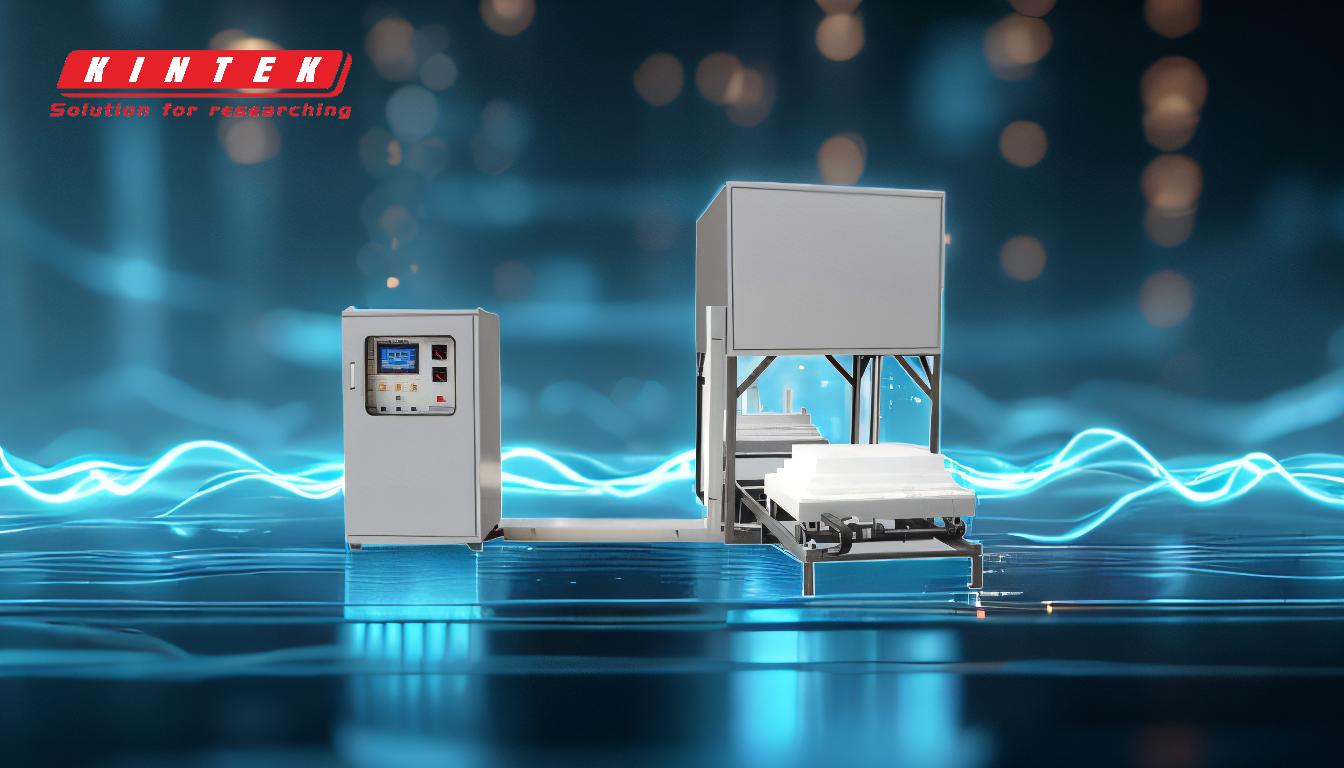
-
Reduced Fuel and Power Consumption:
- Two-stage furnaces operate more efficiently by using less fuel and power. They adjust their output based on the heating needs, running at a lower stage most of the time and only switching to a higher stage when necessary. This adaptability leads to significant energy savings over time.
-
Consistent Home Temperatures:
- Unlike single-stage furnaces that operate at full capacity regardless of the actual heating demand, two-stage furnaces provide more consistent temperatures. This reduces the frequency of on-and-off cycling, which not only enhances comfort but also prevents energy waste.
-
Lower Operating Costs:
- The efficient operation of two-stage furnaces translates into lower monthly energy bills. By consuming less fuel and electricity, these furnaces help homeowners save money on utility costs, offsetting the higher initial investment over the lifespan of the unit.
-
Reduced Wear and Tear:
- Two-stage furnaces experience less mechanical stress because they don't constantly operate at full capacity. This results in fewer breakdowns and a longer lifespan, reducing the need for frequent repairs or replacements.
-
Long-Term Cost Savings:
- While the upfront cost of a two-stage furnace is higher than that of a single-stage model, the long-term savings on energy bills and maintenance can make it a more economical choice. Homeowners can expect to recoup the initial investment through reduced operating expenses over time.
-
Environmental Benefits:
- By consuming less fuel and operating more efficiently, two-stage furnaces contribute to lower greenhouse gas emissions. This makes them an environmentally friendly option for homeowners looking to reduce their carbon footprint.
In summary, a two-stage furnace can save money by operating more efficiently, providing consistent comfort, and reducing long-term maintenance and replacement costs. While the initial investment may be higher, the overall savings and benefits make it a worthwhile consideration for those prioritizing energy efficiency and cost-effectiveness.
Summary Table:
Key Benefits | Details |
---|---|
Reduced Fuel and Power Usage | Adjusts output to match heating needs, saving energy and reducing costs. |
Consistent Home Temperatures | Prevents energy waste and enhances comfort by minimizing on-and-off cycling. |
Lower Operating Costs | Efficient operation leads to reduced monthly energy bills. |
Reduced Wear and Tear | Less mechanical stress means fewer breakdowns and longer lifespan. |
Long-Term Cost Savings | Higher upfront cost offset by lower energy bills and maintenance expenses. |
Environmental Benefits | Lower greenhouse gas emissions due to efficient fuel consumption. |
Ready to save on energy costs and enjoy consistent comfort? Contact us today to learn more about two-stage furnaces!