Heat treatment primarily affects the mechanical and physical properties of metals, such as hardness, strength, and ductility, by altering their microstructure. However, it does not typically change the chemical composition of the material. The process involves controlled heating and cooling to achieve desired properties without modifying the elemental makeup of the alloy. While heat treatment can influence the distribution of elements within the microstructure (e.g., through diffusion), the overall chemical composition remains unchanged.
Key Points Explained:
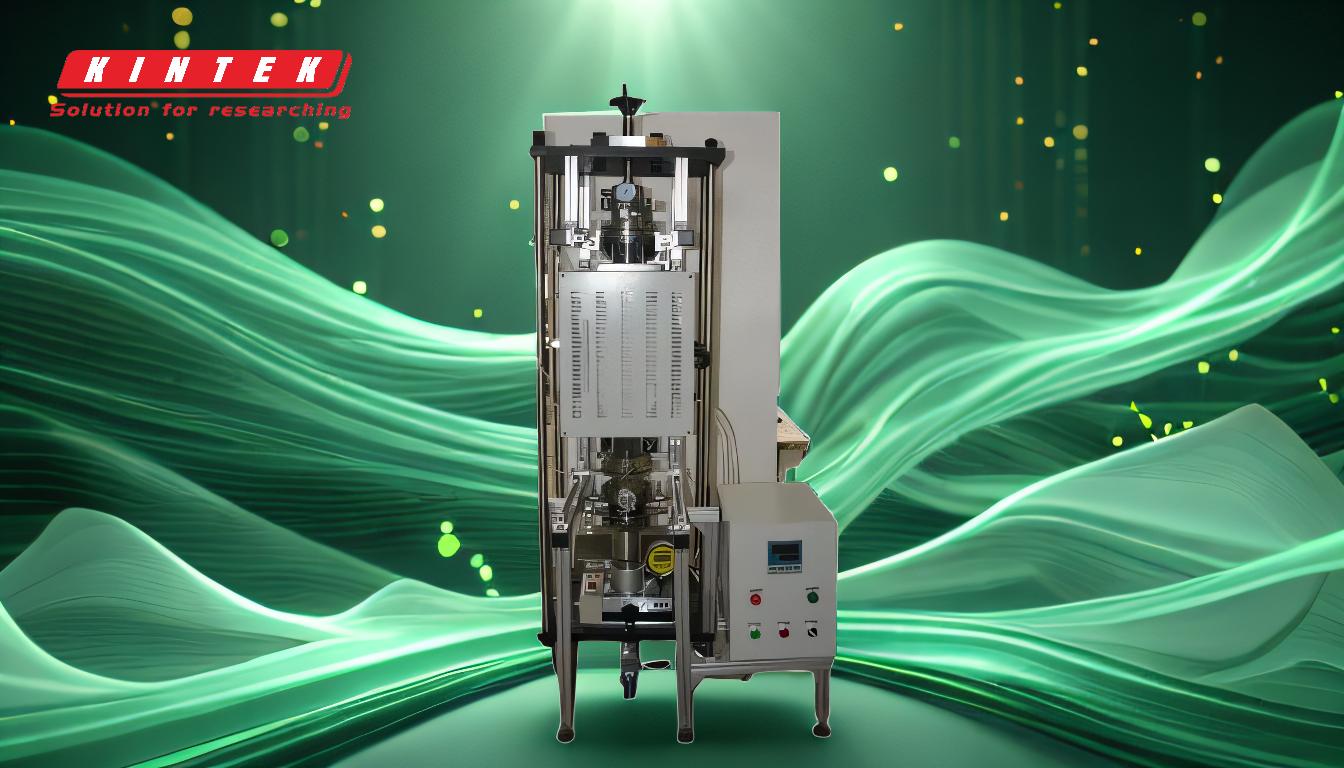
-
Definition and Purpose of Heat Treatment:
- Heat treatment is a process used to alter the physical and mechanical properties of metals and alloys.
- It involves heating the material to a specific temperature, holding it at that temperature, and then cooling it at a controlled rate.
- The primary goal is to achieve desired properties such as increased hardness, improved strength, or enhanced ductility.
-
Microstructural Changes vs. Chemical Composition:
- Heat treatment primarily affects the microstructure of the material, which includes the arrangement and distribution of grains, phases, and defects.
- While the microstructure changes, the chemical composition (the types and proportions of elements in the alloy) remains unchanged.
- For example, in steel, heat treatment can transform austenite into martensite, but the iron and carbon content remains the same.
-
Role of Diffusion in Heat Treatment:
- Diffusion refers to the movement of atoms within the material, which can be influenced by heat treatment.
- During heat treatment, atoms may redistribute within the microstructure, but this does not alter the overall chemical composition.
- For instance, in case hardening, carbon atoms diffuse into the surface of steel, but the bulk chemical composition of the steel remains unchanged.
-
Examples of Heat Treatment Processes:
- Annealing: Softens the material by heating and slow cooling, reducing internal stresses without changing the chemical composition.
- Quenching: Rapid cooling to increase hardness, which alters the microstructure but not the chemical makeup.
- Tempering: Reheating quenched material to reduce brittleness while maintaining the same chemical composition.
-
Exceptions and Special Cases:
- In some processes, such as surface treatments (e.g., carburizing or nitriding), elements like carbon or nitrogen are introduced into the surface layer, altering the surface chemistry.
- However, these are specialized processes and not representative of standard heat treatment.
-
Practical Implications for Equipment and Consumable Purchasers:
- Understanding that heat treatment does not change chemical composition is crucial for selecting materials with the right properties for specific applications.
- For example, if a component requires high strength and toughness, heat-treated steel with the appropriate microstructure can be chosen without worrying about changes in its chemical composition.
In summary, heat treatment is a powerful tool for modifying the mechanical properties of metals and alloys without altering their chemical composition. This makes it a versatile and widely used process in industries ranging from automotive to aerospace.
Summary Table:
Aspect | Details |
---|---|
Purpose | Alters mechanical properties (hardness, strength, ductility) |
Microstructure | Changes grain arrangement, phases, and defects |
Chemical Composition | Remains unchanged during standard heat treatment |
Key Processes | Annealing, Quenching, Tempering |
Exceptions | Surface treatments (e.g., carburizing, nitriding) alter surface chemistry |
Need help selecting the right heat-treated materials for your application? Contact our experts today!