Heat treatment time is a critical factor in ensuring the desired mechanical properties of a workpiece. It depends on several variables, including the size and shape of the workpiece, the amount of furnace charging, the placement form of the workpiece, and the heating temperature. Calculating the heat treatment time involves understanding these factors and applying specific formulas or guidelines tailored to the material and process requirements. Below, we break down the key considerations and steps to calculate heat treatment time effectively.
Key Points Explained:
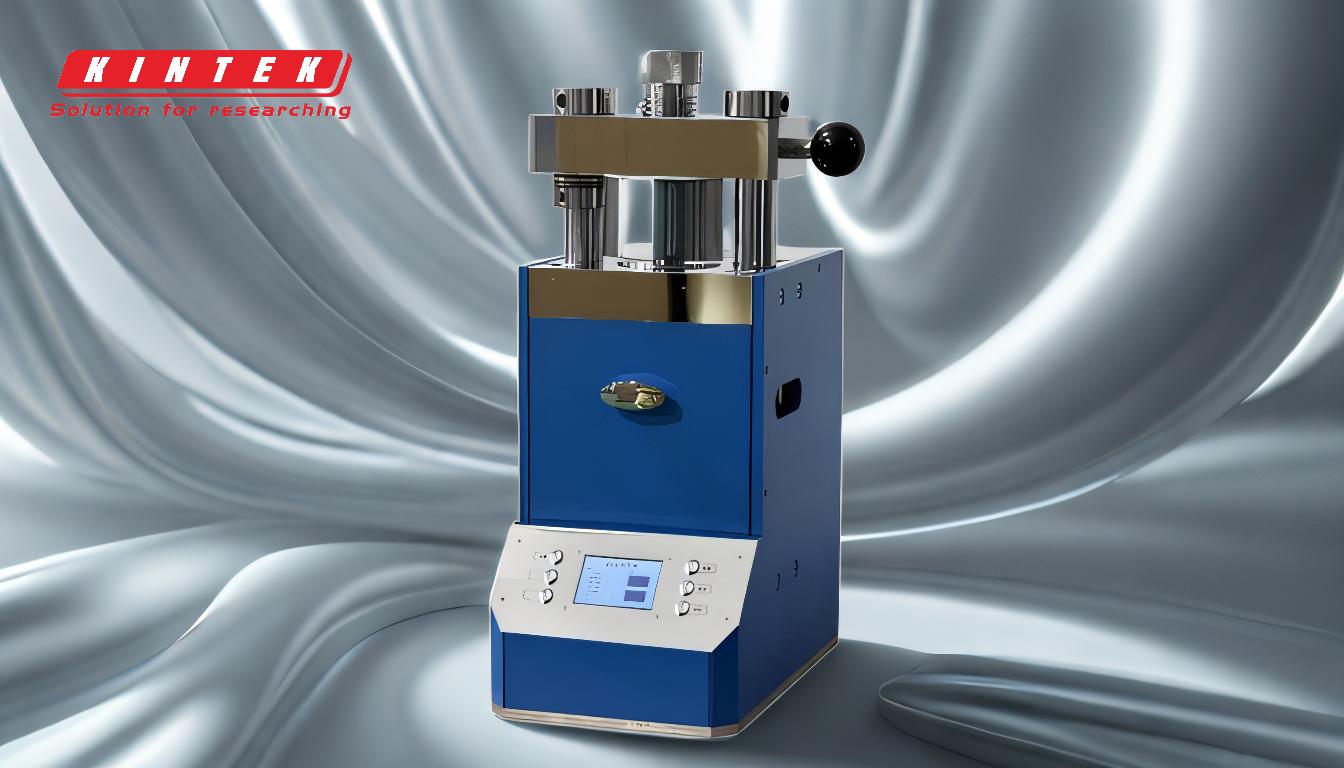
-
Understanding the Factors Affecting Heat Treatment Time
- Size and Shape of the Workpiece: Larger or more complex shapes require longer heat treatment times to ensure uniform heating and cooling.
- Amount of Furnace Charging: Overloading the furnace can lead to uneven heat distribution, requiring adjustments in holding time.
- Workpiece Placement Form: Proper spacing and orientation of workpieces in the furnace are essential for consistent heat treatment.
- Heating Temperature: Higher temperatures may reduce the required holding time, but this depends on the material and desired properties.
-
General Formula for Heat Treatment Time
- The holding time (t) can be estimated using the formula:
[ t = k \times \frac{V}{A} ]
Where:- ( t ) = holding time (minutes or hours)
- ( k ) = a constant dependent on the material and process (e.g., 1.5 for steel)
- ( V ) = volume of the workpiece
- ( A ) = surface area of the workpiece
- This formula ensures that the heat penetrates uniformly throughout the workpiece.
- The holding time (t) can be estimated using the formula:
-
Material-Specific Considerations
- Different materials (e.g., steel, aluminum, titanium) have unique thermal properties, affecting the required heat treatment time.
- For example, steel typically requires longer holding times compared to aluminum due to its lower thermal conductivity.
-
Furnace Charging and Load Density
- The number of workpieces and their arrangement in the furnace impact heat distribution.
- A higher load density may require longer holding times to compensate for reduced heat transfer efficiency.
-
Heating and Cooling Rates
- The rate at which the workpiece is heated and cooled affects the overall heat treatment time.
- Rapid heating may reduce the holding time but risks thermal stress and uneven properties.
-
Practical Guidelines for Calculation
- Refer to material-specific heat treatment charts or standards (e.g., ASM Handbook) for recommended holding times.
- Use simulation software or empirical data to refine calculations for complex geometries or large batches.
-
Validation and Testing
- After calculating the heat treatment time, validate the results through metallurgical testing (e.g., hardness testing, microstructure analysis).
- Adjust the holding time based on test results to achieve the desired properties.
By carefully considering these factors and applying the appropriate formulas or guidelines, you can accurately calculate the heat treatment time for any workpiece. This ensures optimal mechanical properties and minimizes the risk of defects.
Summary Table:
Factor | Impact on Heat Treatment Time |
---|---|
Size and Shape of Workpiece | Larger or complex shapes require longer times for uniform heating and cooling. |
Amount of Furnace Charging | Overloading leads to uneven heat distribution, requiring longer holding times. |
Workpiece Placement Form | Proper spacing and orientation ensure consistent heat treatment. |
Heating Temperature | Higher temps may reduce holding time, but material properties must be considered. |
Material Type | Steel requires longer times than aluminum due to lower thermal conductivity. |
Furnace Load Density | Higher density reduces heat transfer efficiency, increasing holding time. |
Heating and Cooling Rates | Rapid heating may reduce time but risks thermal stress and uneven properties. |
Need help calculating heat treatment time for your project? Contact our experts today for tailored guidance!