Heat treatment is a critical process in metallurgy used to enhance the mechanical properties of metals, such as strength, hardness, and durability. By carefully controlling the heating, holding, and cooling stages, metals can be transformed to meet specific application requirements. Common heat treatment methods include annealing, quenching, tempering, and case hardening, each tailored to achieve distinct material properties. These processes manipulate the metal's microstructure, allowing for improved performance in demanding environments like aerospace and automotive industries. Understanding the principles and techniques of heat treatment is essential for selecting the right method to achieve the desired strength and functionality in metal components.
Key Points Explained:
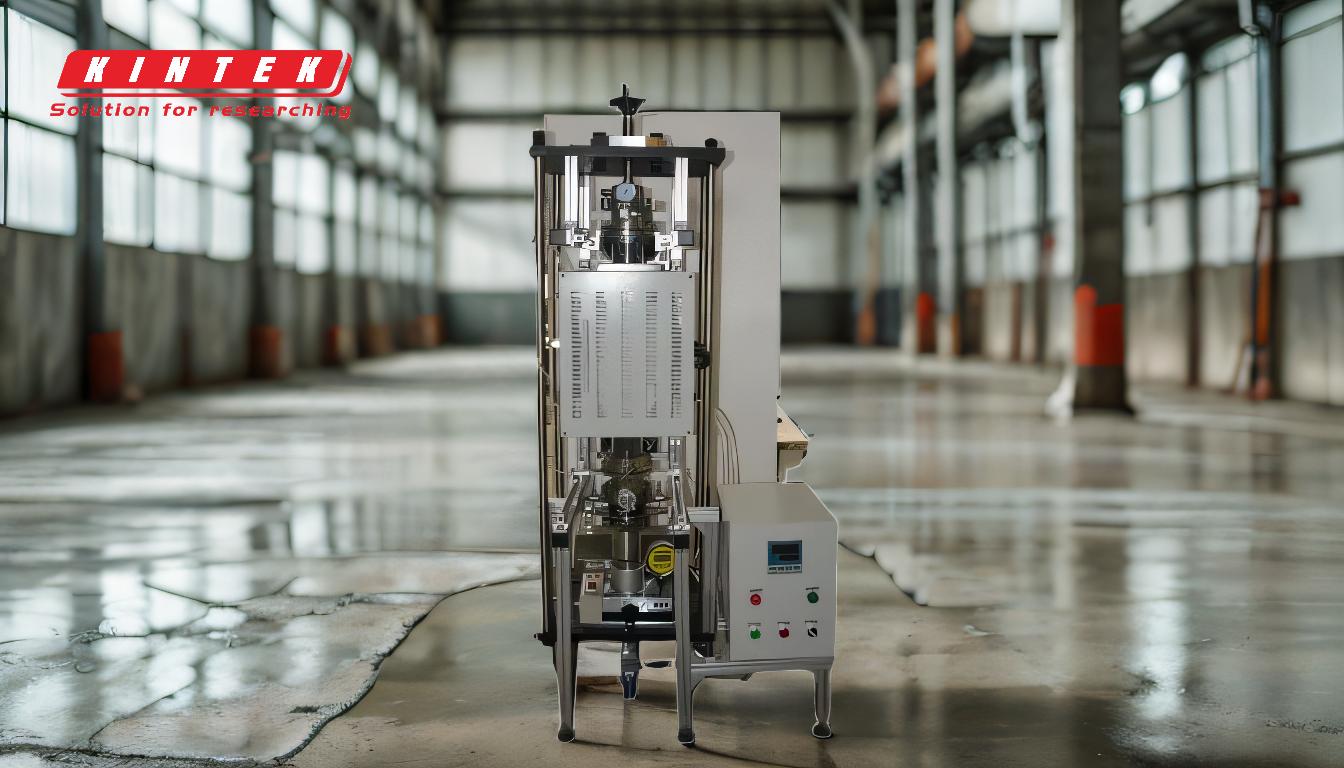
-
Basic Steps of Heat Treatment
- Heat treatment involves three fundamental steps: heating, holding, and cooling.
- Heating: The metal is heated to a specific temperature, which can range up to 2,400°F, depending on the material and desired outcome.
- Holding: The metal is maintained at this temperature for a set period, ranging from seconds to over 60 hours, to allow for structural changes.
- Cooling: The metal is cooled using prescribed methods, such as air cooling, oil quenching, or water quenching, to achieve the desired properties.
- These steps are critical for altering the metal's microstructure and achieving the desired mechanical properties.
- Heat treatment involves three fundamental steps: heating, holding, and cooling.
-
Common Heat Treatment Processes
- Annealing: This process softens the metal, improving ductility and reducing internal stresses. It involves heating the metal to a specific temperature and then slowly cooling it, often in a furnace.
- Quenching: Rapid cooling of the metal, typically in water or oil, to increase hardness and strength. This process can make the metal brittle, so it is often followed by tempering.
- Tempering: After quenching, the metal is reheated to a lower temperature and then cooled to reduce brittleness and improve toughness.
- Case Hardening: A surface treatment that hardens the outer layer of the metal while maintaining a softer, tougher core. Techniques include carburizing and nitriding.
- Precipitation Hardening: A process that strengthens the metal by forming fine particles within the microstructure, enhancing strength and hardness.
-
Impact on Mechanical Properties
- Heat treatment can significantly alter the mechanical properties of metals:
- Hardness: Increased through processes like quenching and case hardening.
- Strength: Enhanced by precipitation hardening and quenching.
- Toughness: Improved by tempering, which balances hardness and ductility.
- Ductility: Increased through annealing, making the metal easier to shape and form.
- Elasticity: Enhanced by processes like austempering, which improves resilience.
- Heat treatment can significantly alter the mechanical properties of metals:
-
Applications of Heat Treatment
- Heat treatment is widely used in industries requiring high-performance materials:
- Aerospace: Components like turbine blades and landing gear require high strength and durability.
- Automotive: Engine parts, gears, and suspension components benefit from improved hardness and wear resistance.
- Manufacturing: Batch production of metal parts often involves heat treatment to ensure consistency and quality.
- Vacuum heat treatment is particularly beneficial for improving corrosion resistance and shear strength, expanding the range of applications for treated metals.
- Heat treatment is widely used in industries requiring high-performance materials:
-
Considerations for Heat Treatment
- Material Selection: Different metals and alloys respond differently to heat treatment, so the process must be tailored to the specific material.
- Cost vs. Quality: Heat treatment must balance cost-effectiveness with the desired quality and performance of the final product.
- Environmental Factors: Processes like vacuum heat treatment minimize oxidation and contamination, making them suitable for high-precision applications.
By understanding and applying these principles, manufacturers can optimize the strength and performance of metal components, ensuring they meet the demands of their intended applications.
Summary Table:
Aspect | Details |
---|---|
Basic Steps | Heating, holding, and cooling to alter microstructure. |
Common Processes | Annealing, quenching, tempering, case hardening, precipitation hardening. |
Impact on Properties | Increases hardness, strength, toughness, ductility, and elasticity. |
Applications | Aerospace, automotive, manufacturing, and high-performance components. |
Key Considerations | Material selection, cost vs. quality, and environmental factors. |
Optimize your metal components with expert heat treatment solutions—contact us today!