A forging press is a machine used to shape metal by applying compressive force. It operates through either mechanical or hydraulic mechanisms. Mechanical forging presses use a motor, clutch, and crankshaft to drive a ram with a constant stroke length, achieving maximum force at the bottom of the stroke. Hydraulic forging presses, on the other hand, rely on high-pressure fluid to generate immense force, capable of producing up to 75,000 tons of pressure. Both types of presses are essential in manufacturing processes, particularly in hot forging, where the metal is heated to improve malleability. The presses ensure precise shaping, reduced deformation, and high-quality outputs through automated processes like ejection and demolding.
Key Points Explained:
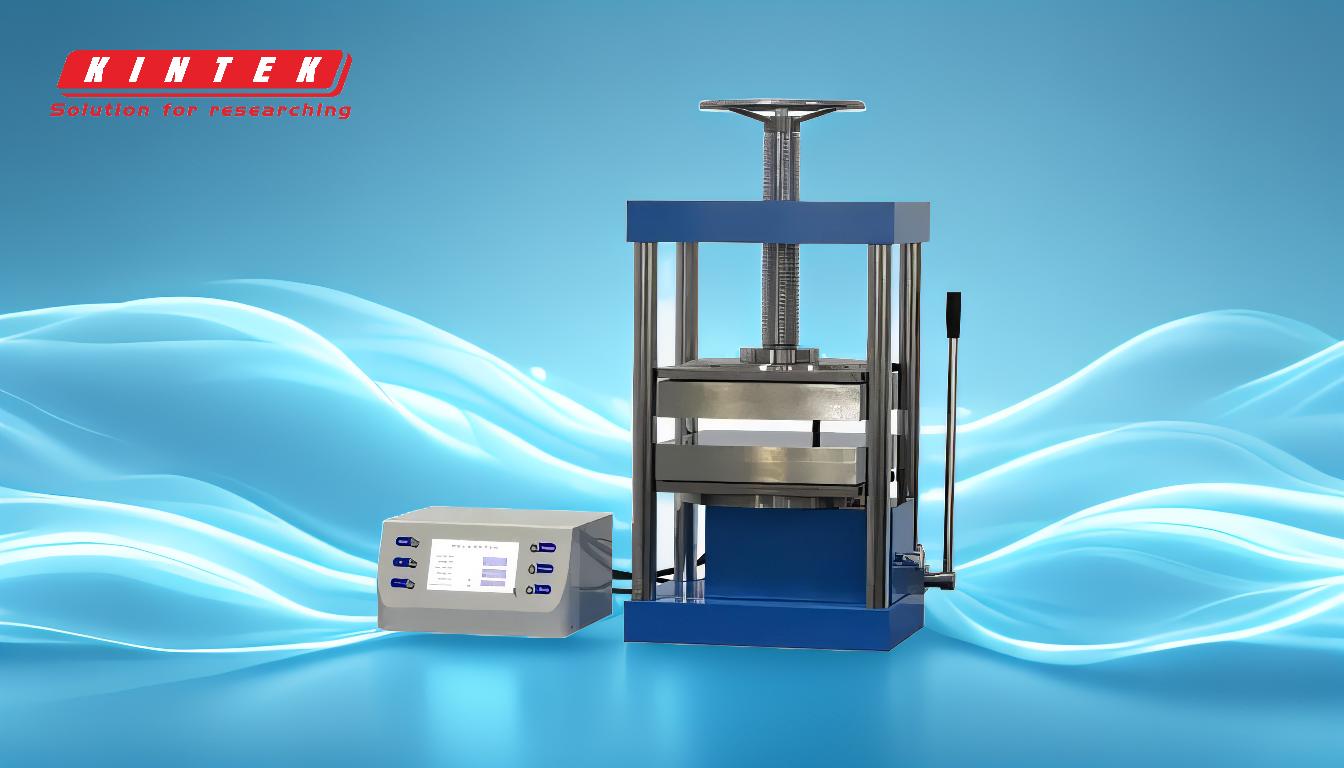
-
Mechanical Forging Press Mechanism:
- A mechanical forging press is powered by a motor and controller, which drive a clutch and crankshaft.
- The crankshaft converts rotational motion into linear motion, moving the ram with a constant stroke length.
- The ram's speed is highest at the center of the stroke, while maximum force is exerted at the bottom of the stroke.
- Knockout or liftout pins are used to automatically eject the forged part from the die, ensuring efficiency and consistency.
-
Hydraulic Forging Press Mechanism:
- Hydraulic forging presses utilize high-pressure fluid to generate force.
- These presses are capable of producing extremely high forces, up to 75,000 tons, making them suitable for large-scale forging operations.
- The hydraulic system allows for precise control over the force and speed, which is critical for maintaining product quality and reducing material waste.
-
Hot Press Machine Working Principle:
- Hot press machines operate by applying positive pressure based on negative pressure, often using special glue to bond materials.
- They function under high pressure and low temperature, with short film pressure times to minimize workpiece deformation.
- These machines are automated and can perform multiple processes, including table feeding, heating, vacuuming, forming, and demolding, driven by oil pressure and compressed air.
-
Applications and Benefits:
- Forging presses are widely used in industries such as automotive, aerospace, and manufacturing for producing high-strength metal components.
- The precise control over force and speed ensures high-quality outputs with minimal defects.
- Automated features like ejection and demolding enhance productivity and reduce labor costs.
-
Comparison Between Mechanical and Hydraulic Presses:
- Mechanical presses are generally faster and more suitable for high-volume production due to their constant stroke length.
- Hydraulic presses offer greater flexibility and control, making them ideal for complex shapes and large-scale forging operations.
- The choice between mechanical and hydraulic presses depends on the specific requirements of the manufacturing process, including the type of material, desired output, and production volume.
By understanding these key points, a purchaser can make informed decisions about the type of forging press that best meets their operational needs, ensuring optimal performance and cost-efficiency.
Summary Table:
Aspect | Mechanical Forging Press | Hydraulic Forging Press |
---|---|---|
Mechanism | Motor, clutch, crankshaft drive ram | High-pressure fluid generates force |
Force | Maximum force at bottom of stroke | Up to 75,000 tons of pressure |
Speed | Faster, constant stroke length | Slower, precise control |
Applications | High-volume production | Complex shapes, large-scale operations |
Benefits | Efficiency, consistency | Flexibility, reduced material waste |
Discover the right forging press for your needs—contact our experts today!