A graphite heater operates by utilizing graphite rods enclosed within a graphite chamber to create a controlled hot zone. This setup efficiently manages heat distribution and conserves electrical energy. The system is integrated with a Distributed Control System (DCS) to monitor and regulate electrical power, gas flows, water flows, temperature, and pressure, ensuring precise control over the heating process.
Key Points Explained:
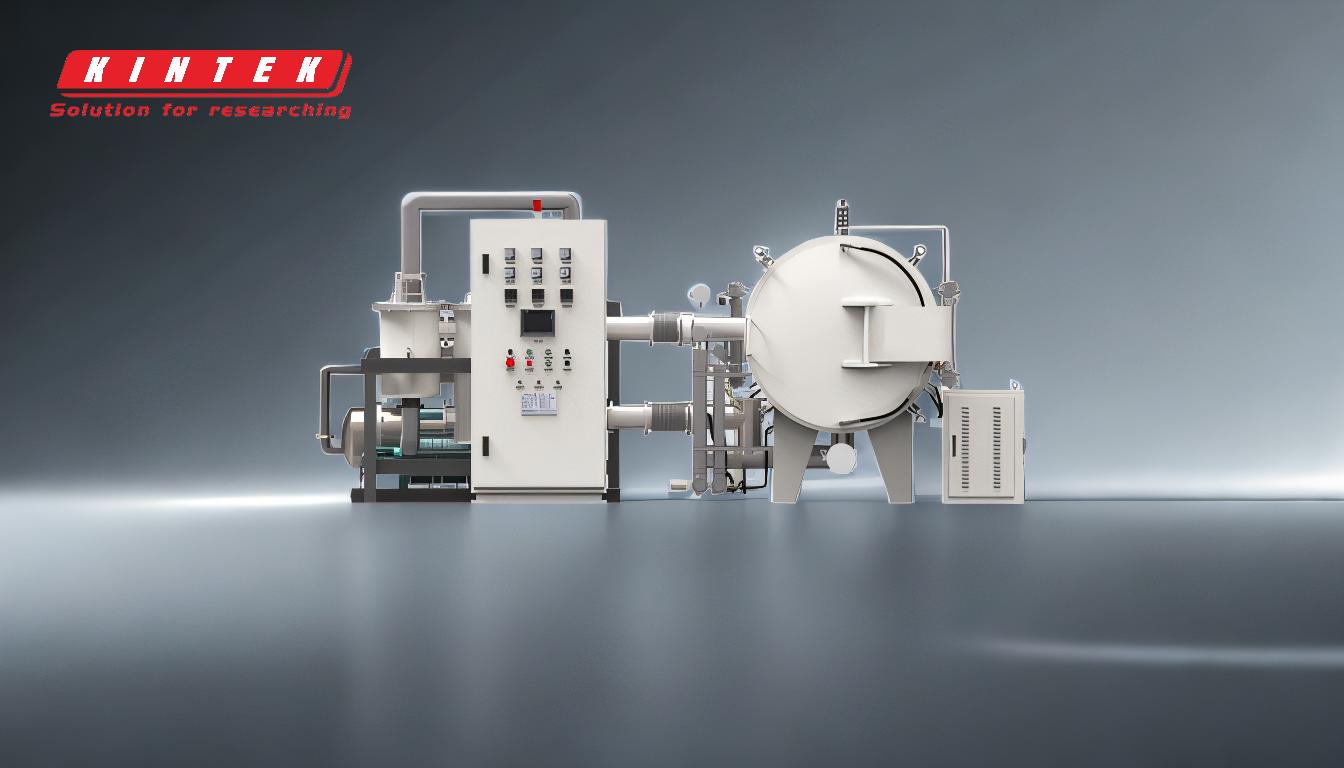
-
Graphite Rods and Chamber:
- Graphite Rods: These are the primary heating elements in the system. Graphite is chosen for its excellent thermal conductivity and high melting point, making it ideal for high-temperature applications.
- Graphite Chamber: The rods are enclosed within a graphite chamber, which helps in creating a controlled hot zone. The chamber's design ensures that heat is evenly distributed and contained within the desired area, enhancing efficiency.
-
Hot Zone Creation:
- The graphite rods generate heat when an electrical current is passed through them. This heat is then transferred to the surrounding environment within the graphite chamber.
- The chamber's insulation properties help in maintaining a consistent temperature within the hot zone, reducing heat loss and conserving energy.
-
Energy Conservation:
- The use of graphite materials and the chamber's design contribute to energy efficiency. Graphite's high thermal conductivity allows for rapid heat transfer, reducing the time and energy required to reach the desired temperature.
- The controlled environment minimizes heat dissipation, ensuring that the energy is used effectively to maintain the hot zone.
-
Control and Monitoring:
- Distributed Control System (DCS): This system plays a crucial role in managing the heater's operations. It continuously monitors and adjusts various parameters to ensure optimal performance.
- Electrical Power: The DCS regulates the electrical current supplied to the graphite rods, controlling the amount of heat generated.
- Gas and Water Flows: These flows are managed to maintain the desired atmosphere and cooling within the system, respectively.
- Temperature and Pressure: The DCS ensures that the temperature and pressure within the chamber remain within the specified range, preventing overheating or pressure build-up.
-
Applications:
- Graphite heaters are commonly used in industries requiring high-temperature processes, such as semiconductor manufacturing, metallurgy, and chemical processing.
- The precise control offered by the DCS makes these heaters suitable for applications where consistent and accurate temperature management is critical.
In summary, a graphite heater works by leveraging the thermal properties of graphite to create a controlled hot zone. The integration with a DCS ensures efficient and precise management of the heating process, making it an energy-efficient solution for high-temperature applications.
Summary Table:
Key Components | Function |
---|---|
Graphite Rods | Primary heating elements with high thermal conductivity and melting point. |
Graphite Chamber | Encloses rods to create a controlled hot zone, ensuring even heat distribution. |
Distributed Control System (DCS) | Monitors and regulates power, gas/water flows, temperature, and pressure. |
Applications | Used in semiconductor manufacturing, metallurgy, and chemical processing. |
Discover how a graphite heater can optimize your high-temperature processes—contact our experts today!