A hydraulic press operates based on Pascal's principle, which states that pressure applied to a confined fluid is transmitted equally in all directions. The machine consists of interconnected cylinders filled with hydraulic fluid. When a small force is applied to the smaller cylinder (plunger), it creates pressure in the fluid, which is then transmitted to the larger cylinder (ram), resulting in a much larger force. This process is utilized in various industrial applications, such as molding, forging, and pressing materials. The hydraulic press is composed of three main components: the mainframe, power system, and hydraulic control instruments, which work together to ensure precise and efficient operation.
Key Points Explained:
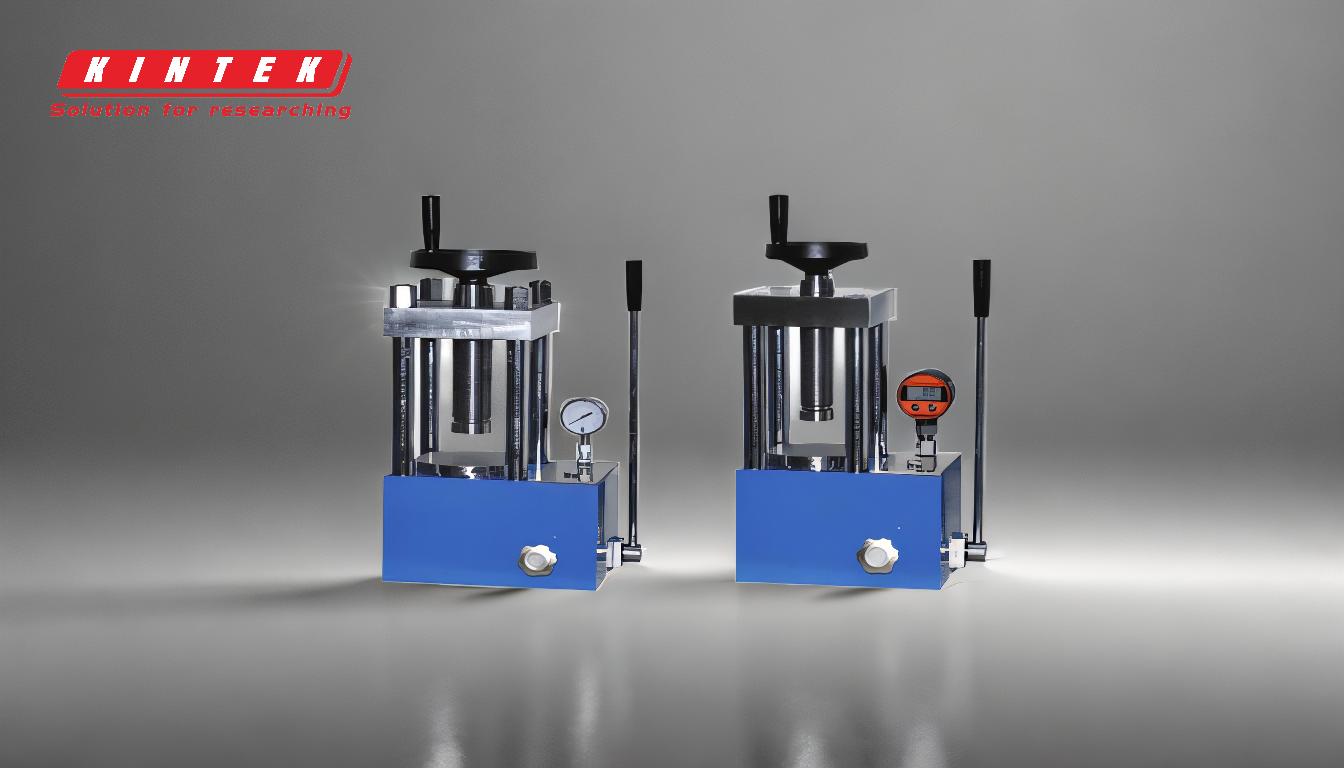
-
Pascal's Principle and Hydraulic Force Multiplication:
- The hydraulic press operates on Pascal's principle, which states that pressure applied to a confined fluid is transmitted equally in all directions. This principle allows a small force applied to a smaller piston (plunger) to generate a much larger force on a larger piston (ram). The force multiplication is achieved due to the difference in the surface areas of the two pistons.
-
Components of a Hydraulic Press:
- Mainframe: The structural framework that holds the components together and provides stability during operation.
- Power System: Typically an electric motor that drives a hydraulic pump, generating the necessary fluid pressure.
- Hydraulic Control Instruments: These include valves, gauges, and control systems that regulate the flow and pressure of the hydraulic fluid, ensuring precise operation.
-
Hydraulic Cylinders and Pistons:
- The hydraulic press consists of two interconnected cylinders: the smaller plunger and the larger ram. The plunger applies a small force to the hydraulic fluid, creating pressure. This pressure is transmitted to the ram, which then applies a much larger force to the workpiece.
-
Operation Steps:
- Step 1: The operator initiates the hydraulic pump, which starts to pressurize the hydraulic fluid.
- Step 2: The pressurized fluid is directed to the smaller plunger, creating a force.
- Step 3: The pressure is transmitted through the fluid to the larger ram, resulting in a magnified force.
- Step 4: The ram applies this force to the workpiece, performing the desired operation such as pressing, molding, or forging.
- Step 5: After the operation, the fluid pressure is released, and the ram retracts to its original position.
-
Applications of Hydraulic Presses:
- Hydraulic presses are used in a wide range of industrial applications, including:
- Metal Forming: Forging, stamping, and bending metal sheets.
- Molding: Compressing materials into specific shapes, such as plastic or composite materials.
- Assembly: Press-fitting components together.
- Testing: Applying controlled forces to test the strength and durability of materials.
- Hydraulic presses are used in a wide range of industrial applications, including:
-
Advantages of Hydraulic Presses:
- High Force Output: Capable of generating extremely high forces, making them suitable for heavy-duty applications.
- Precision Control: Hydraulic systems allow for precise control over force, speed, and position, ensuring accurate results.
- Versatility: Can be used for a wide range of applications by adjusting pressure and tooling.
- Safety: Equipped with safety features such as pressure relief valves and emergency stop buttons to prevent accidents.
-
Hydraulic Hot Press Machine:
- A hydraulic hot press machine combines hydraulic pressing with heat application, making it ideal for processes that require both pressure and temperature control, such as laminating, curing, and bonding materials. The machine features precise temperature control, multi-stage pressure settings, and advanced safety mechanisms, ensuring efficient and safe operation.
By understanding these key points, one can appreciate the efficiency and versatility of hydraulic presses in various industrial applications. The integration of hydraulic systems with advanced control technologies ensures that these machines can perform complex tasks with precision and reliability.
Summary Table:
Step | Description |
---|---|
Step 1 | Operator initiates the hydraulic pump, pressurizing the fluid. |
Step 2 | Pressurized fluid creates force on the smaller plunger. |
Step 3 | Pressure is transmitted to the larger ram, magnifying the force. |
Step 4 | Ram applies the force to the workpiece for pressing, molding, or forging. |
Step 5 | Fluid pressure is released, and the ram retracts. |
Discover how a hydraulic press can transform your industrial processes—contact our experts today for more information!