Short path distillation is a specialized technique used to separate and purify compounds, particularly those that are heat-sensitive or have high boiling points. The process leverages vacuum technology to lower the boiling points of substances, enabling efficient separation at reduced temperatures. This method is particularly advantageous for distilling heavier molecules and maintaining the integrity of sensitive materials. The process involves heating the material in a feed vessel, creating a vacuum to reduce pressure, and then condensing the vapors in fractionating tubing. The result is a highly efficient and cost-effective distillation process that is ideal for small-scale operations or those with limited space.
Key Points Explained:
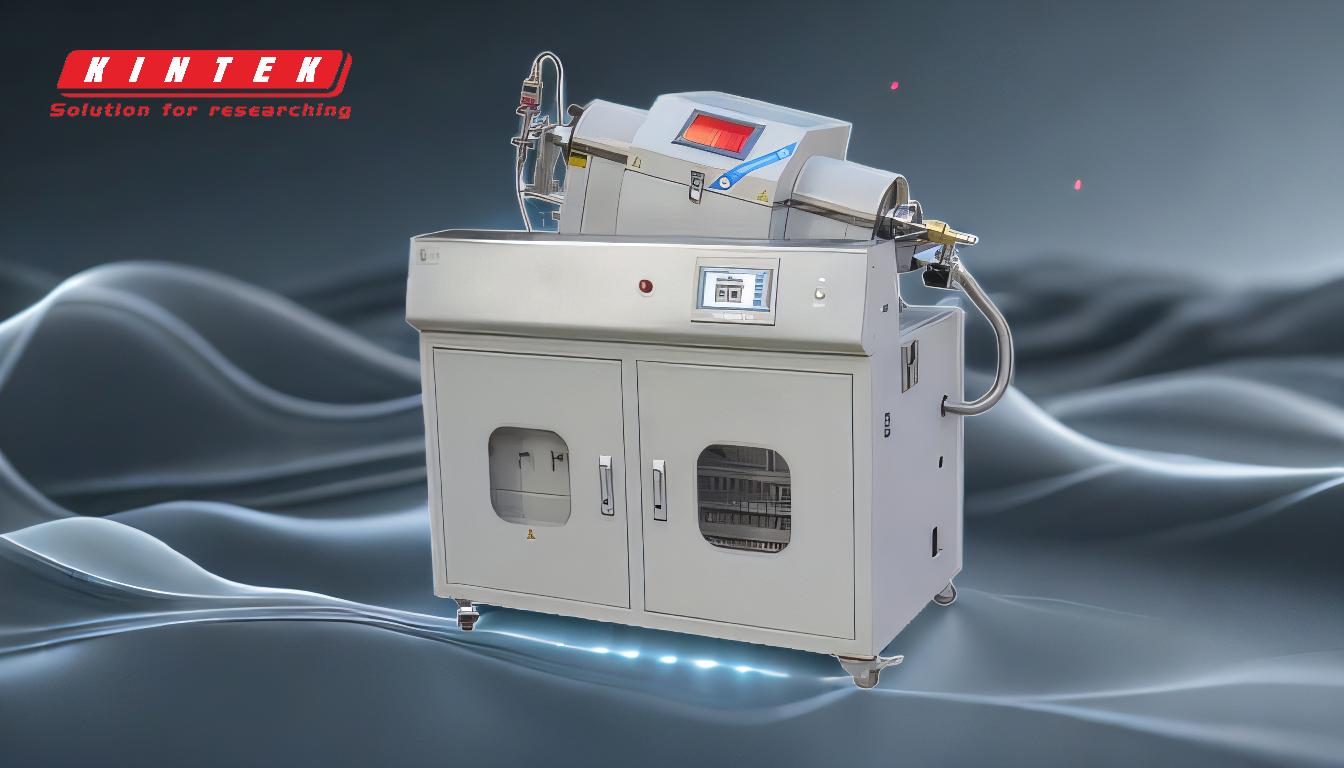
-
Principle of Short Path Distillation:
- Short path distillation works by reducing the pressure within the distillation equipment, which lowers the boiling points of substances. This is achieved through the use of a vacuum, which decreases atmospheric pressure and allows for evaporation at lower temperatures.
- The process begins with the material being placed in a feed vessel and heated gradually. The vacuum draws the vapors into fractionating tubing, where they cool, condense, and re-vaporize, enriching the vapors in a specific component.
-
Role of Vacuum in Short Path Distillation:
- The vacuum is crucial as it reduces the boiling temperature needed for distillation, making it easier to separate components. This is particularly beneficial for distilling heavier molecules and heat-sensitive materials.
- The vacuum can be controlled manually or automatically using a Vacuum Controller, which is typically connected to a vacuum source such as a laboratory pump or an in-house vacuum line.
-
Advantages of Short Path Distillation:
- Cost and Space Efficiency: Short path distillation is ideal for those with limited budgets or space, as it does not require large distillation equipment. Despite its compact size, it maintains high product quality.
- Efficiency for Heavier Molecules: The reduced boiling points under vacuum conditions make short path distillation more efficient for separating heavier molecules compared to traditional methods.
- Heat-Sensitive Materials: The ability to operate at lower temperatures is crucial for the distillation of heat-sensitive materials, preserving their integrity and quality.
-
Process Steps in Short Path Distillation:
- Diffusion: Molecules diffuse from the liquid phase to the evaporation surface.
- Evaporation: Free evaporation of molecules occurs on the liquid surface.
- Transport: Molecules fly from the evaporation surface to the condensation surface.
- Condensation: The condensed solvents are collected in the receiving flask.
- Vacuum Environment: A vacuum pump provides the necessary vacuum environment, and the condensing part turns gas-phase solvents into liquid-phase solvents.
-
Applications and Benefits:
- Continuous Separation: Vacuum technology allows for a continuous separation process with very short residence times, typically tens of seconds, compared to hours required by conventional methods.
- High-Quality Output: The process ensures high-quality output by minimizing thermal degradation and preserving the chemical structure of the distilled materials.
In summary, short path distillation is a highly efficient and versatile method for separating and purifying compounds, particularly those that are heat-sensitive or have high boiling points. The use of vacuum technology plays a pivotal role in reducing boiling temperatures, making the process faster, more efficient, and suitable for a wide range of applications.
Summary Table:
Aspect | Details |
---|---|
Principle | Chemical reactions deposit thin films on substrates under controlled conditions. |
Process Steps | 1. Precursor introduction 2. Chemical reaction 3. Film deposition 4. Byproduct removal. |
Key Advantages | High purity, uniform coatings, and scalability for industrial applications. |
Applications | Semiconductor manufacturing, solar panels, and protective coatings. |
Discover how CVD can enhance your manufacturing process—contact our experts today!