Grain size plays a critical role in determining the mechanical properties of ceramics, particularly hardness and fracture toughness. As grain size increases, hardness tends to decrease due to reduced resistance to deformation. Fracture toughness, however, remains relatively stable for smaller grain sizes (up to 0.40 μm) but increases significantly as grain size grows, reaching higher values (up to 7.8 MPam^0.5) for larger grains (e.g., 1.8 μm). This relationship highlights the importance of controlling grain size during ceramic manufacturing to achieve desired material properties for specific applications.
Key Points Explained:
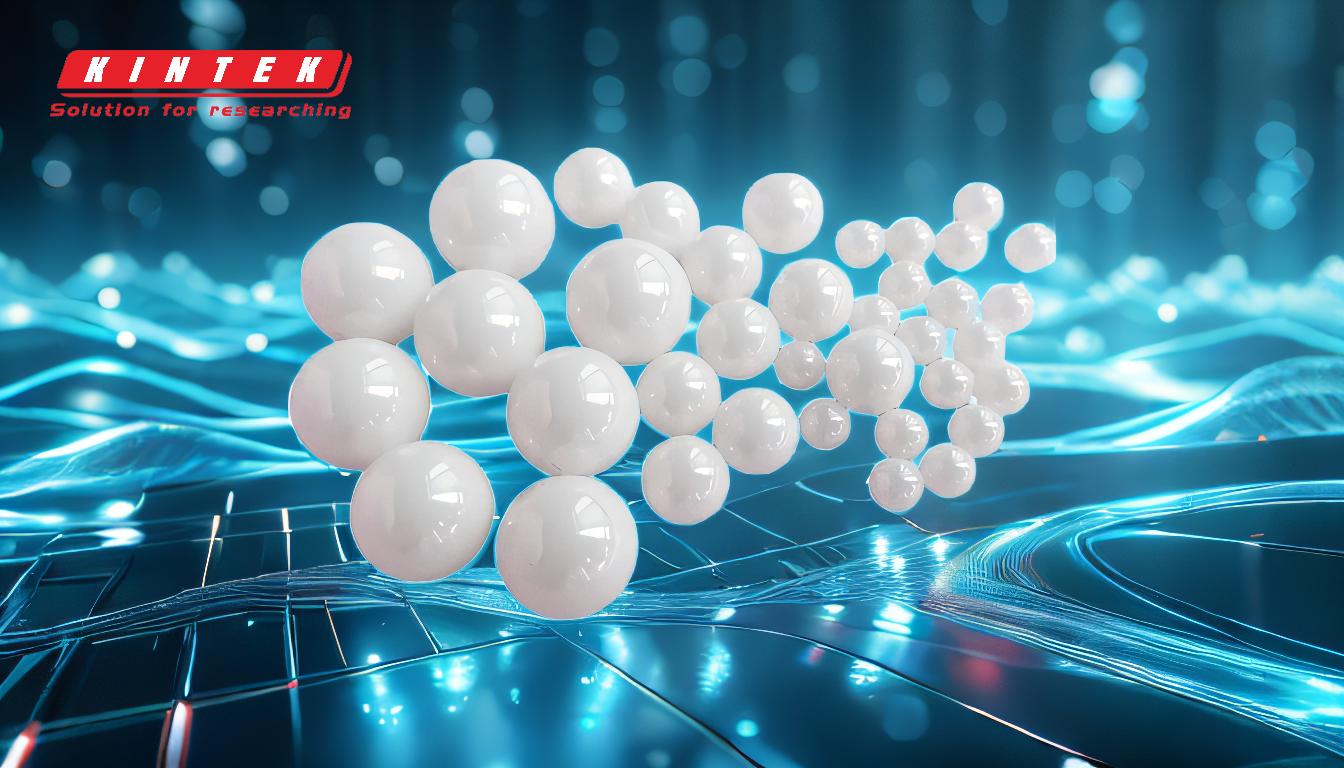
-
Effect of Grain Size on Hardness:
- Observation: Hardness decreases as grain size increases.
- Explanation: Smaller grains create more grain boundaries, which act as barriers to dislocation movement. This increases resistance to deformation, resulting in higher hardness. Larger grains reduce the number of grain boundaries, making the material less resistant to deformation and thus softer.
-
Effect of Grain Size on Fracture Toughness:
- Observation: Fracture toughness remains constant for grain sizes up to 0.40 μm but increases with larger grain sizes, reaching up to 7.8 MPam^0.5 for grain sizes of 1.8 μm.
-
Explanation:
- For small grain sizes, the material's fracture toughness is dominated by the grain boundaries, which can act as crack propagation paths. This keeps toughness relatively stable.
- As grain size increases, the crack propagation path becomes more tortuous, requiring more energy to propagate cracks. This results in higher fracture toughness for larger grains.
-
Implications for Ceramic Manufacturing:
- Hardness vs. Toughness Trade-off: Manufacturers must balance grain size to achieve the desired combination of hardness and toughness. Smaller grains are preferred for high hardness, while larger grains are better for improved toughness.
- Application-Specific Design: For applications requiring wear resistance (e.g., cutting tools), smaller grain sizes are ideal. For applications requiring impact resistance (e.g., armor), larger grain sizes may be more suitable.
-
Practical Considerations:
- Grain Size Control: Achieving the desired grain size requires precise control over sintering conditions, such as temperature, pressure, and sintering time.
- Material Selection: The choice of ceramic material also influences how grain size affects properties. For example, alumina and zirconia may exhibit different grain size-property relationships due to their intrinsic material characteristics.
By understanding these relationships, purchasers and engineers can make informed decisions about ceramic materials based on the specific mechanical properties required for their applications.
Summary Table:
Property | Effect of Grain Size | Key Insights |
---|---|---|
Hardness | Decreases as grain size increases | Smaller grains increase resistance to deformation, resulting in higher hardness. |
Fracture Toughness | Stable for grain sizes ≤ 0.40 μm; increases significantly for larger grains (e.g., 1.8 μm) | Larger grains create tortuous crack paths, enhancing fracture toughness. |
Manufacturing | Requires precise control of sintering conditions | Balance grain size for desired hardness and toughness based on application. |
Applications | Smaller grains for wear resistance; larger grains for impact resistance | Tailor grain size to specific mechanical property requirements. |
Need help selecting the right ceramic material for your application? Contact our experts today for tailored solutions!