Heat treatment is a critical process in metallurgy that significantly influences the mechanical properties of metals. By subjecting metals to controlled heating and cooling cycles, heat treatment can enhance properties such as hardness, strength, ductility, and toughness. The process involves altering the microstructure of the metal, which in turn affects its mechanical behavior. Different heat treatment methods, such as annealing, quenching, and tempering, are employed to achieve specific property enhancements. Understanding how heat treatment affects mechanical properties is essential for optimizing the performance of metals in various industrial applications.
Key Points Explained:
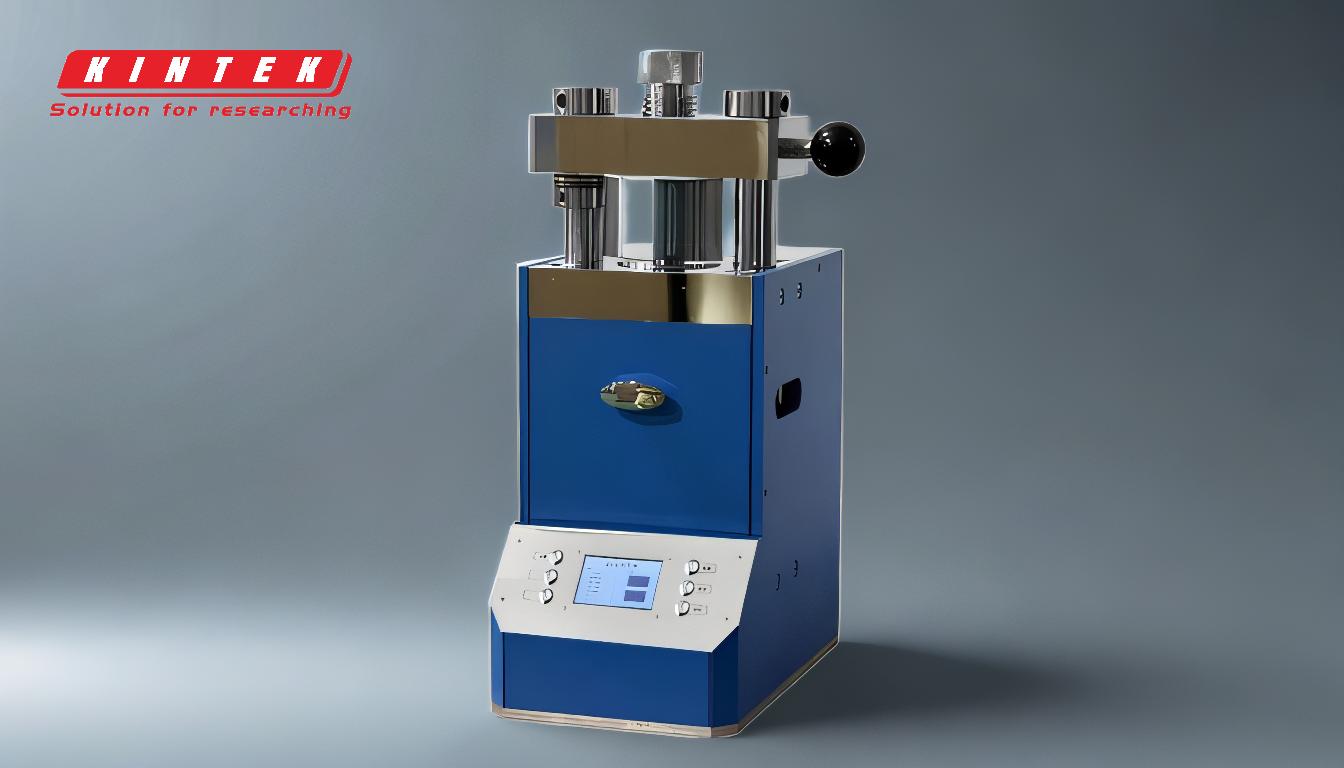
-
Microstructural Changes During Heat Treatment:
- Heat treatment induces changes in the metal's microstructure, which directly impacts its mechanical properties. For instance, heating a metal to a specific temperature can cause phase transformations, such as the conversion of austenite to martensite in steel, which increases hardness and strength.
- The cooling rate after heating is crucial. Rapid cooling (quenching) can lock in a hard microstructure, while slower cooling (annealing) allows for the formation of a softer, more ductile structure.
-
Hardness and Strength Enhancement:
- Heat treatment can significantly increase the hardness and strength of metals. Quenching, for example, creates a hard, brittle structure by rapidly cooling the metal, which is often followed by tempering to reduce brittleness while maintaining strength.
- The formation of fine-grained structures during heat treatment also contributes to increased strength, as smaller grains impede dislocation movement within the metal.
-
Ductility and Toughness Improvement:
- While some heat treatments increase hardness and strength, others are designed to improve ductility and toughness. Annealing, for instance, softens the metal, making it more ductile and easier to work with.
- Tempering, which involves reheating quenched metal to a lower temperature, reduces brittleness and enhances toughness, making the metal more resistant to impact and fatigue.
-
Stress Relief and Dimensional Stability:
- Heat treatment can relieve internal stresses in metals that arise from manufacturing processes like casting, welding, or machining. Stress-relief annealing reduces the risk of distortion or cracking during subsequent use.
- By stabilizing the microstructure, heat treatment also improves dimensional stability, ensuring that the metal retains its shape and size under varying conditions.
-
Application-Specific Heat Treatment:
- The choice of heat treatment method depends on the intended application of the metal. For example, tool steels are often subjected to quenching and tempering to achieve high hardness and wear resistance, while structural steels may undergo normalizing to improve toughness and machinability.
- The properties required for a specific application, such as hardness for cutting tools or ductility for sheet metal forming, guide the selection of the appropriate heat treatment process.
In summary, heat treatment is a versatile and essential process that allows for the precise control of a metal's mechanical properties. By understanding the effects of different heat treatment methods on microstructure and properties, engineers and metallurgists can tailor metals to meet the specific demands of various applications, ensuring optimal performance and longevity.
Summary Table:
Aspect | Effect of Heat Treatment |
---|---|
Microstructural Changes | Alters microstructure, e.g., austenite to martensite, enhancing hardness and strength. |
Hardness & Strength | Increases through quenching and fine-grained structures, tempered to reduce brittleness. |
Ductility & Toughness | Improves via annealing and tempering, making metals more ductile and resistant to fatigue. |
Stress Relief | Reduces internal stresses from manufacturing, preventing distortion or cracking. |
Dimensional Stability | Stabilizes microstructure, ensuring metals retain shape and size under varying conditions. |
Application-Specific | Tailors properties (e.g., hardness for tools, ductility for forming) based on intended use. |
Optimize your metal's performance with tailored heat treatment—contact our experts today!