Spark plasma sintering (SPS) is an advanced sintering technique that leverages electric current and rapid heating rates to achieve high-density material consolidation. This method is particularly effective for sintering a wide range of materials, including ceramics, metals, and composites, at lower temperatures and shorter times compared to traditional sintering methods. The process involves the application of a pulsed direct current that passes through the material and the die, enabling both internal and external heating. This results in enhanced densification mechanisms such as surface oxide removal, electromigration, and electroplasticity. SPS is also capable of producing materials with superior mechanical and optical properties, making it a valuable technique for advanced material fabrication.
Key Points Explained:
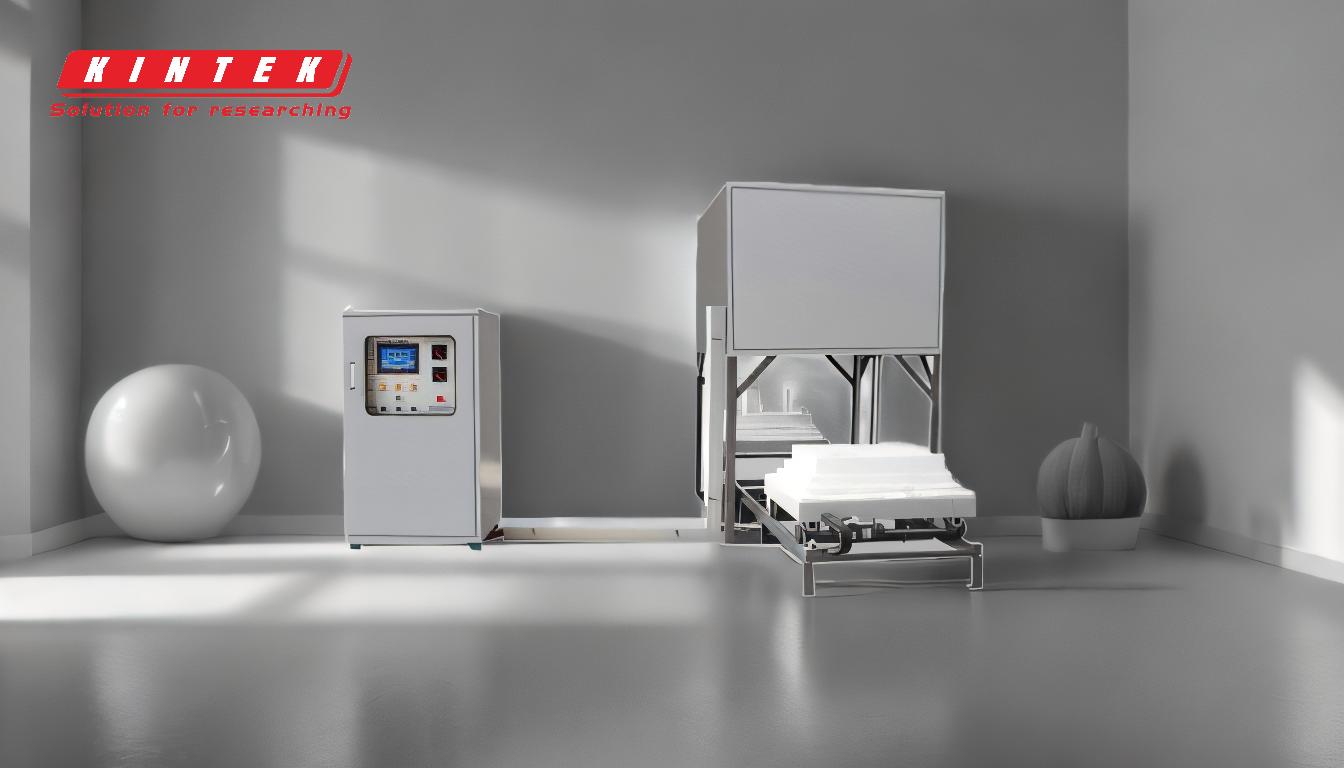
-
Application of Electric Current:
- In SPS, a pulsed direct current is applied, which passes through the conducting pressure die (typically made of graphite) and, if the material is conductive, through the material itself. This dual heating mechanism (internal and external) significantly enhances the sintering process by activating various mechanisms such as surface oxide removal, electromigration, and electroplasticity. These mechanisms contribute to the rapid densification of the material.
-
High Heating Rate:
- One of the standout features of SPS is its ability to achieve extremely high heating rates, up to 1000°C/min. This rapid heating allows for the consolidation of materials at lower temperatures and in shorter times compared to conventional sintering methods. The high heating rate is particularly beneficial for preserving the refined microstructure of materials, especially those processed through techniques like cryogenic milling.
-
Steps in the Sintering Process:
- Composition: The process begins with the addition and mixing of primary materials and coupling agents. This step ensures that the powder is well-prepared for the subsequent stages.
- Compression: The mixed powder is then pressed into the required shape using a die. This step is crucial for achieving the desired geometry and initial density of the material.
- Heat: The shaped powder is subjected to high temperatures, which remove the coupling agent and fuse the primary material into a low-porosity whole. The rapid heating rate in SPS ensures that this step is completed efficiently, resulting in a dense and well-consolidated material.
-
Die as a Heat Source:
- In SPS, the die not only serves as a mold for shaping the material but also acts as a heat source. The electrical current passes through the graphite die, and if the material is conductive, it also passes through the material itself. This results in uniform heating and rapid sintering, which are key advantages of the SPS method.
-
Advantages of SPS:
- Simple Operation: SPS is relatively straightforward to operate, requiring less complex equipment compared to traditional sintering methods.
- Low Technical Requirements: The process does not demand highly specialized skills, making it accessible for a wide range of applications.
- Fast Sintering Speed: The rapid heating and cooling rates significantly reduce the overall sintering time, enhancing productivity and efficiency.
-
Preparation of Amorphous Materials:
- SPS is particularly effective for preparing amorphous materials, such as glass. The technique achieves order-disorder transitions at temperatures far below the melting point of glass, resulting in materials with higher hardness, fracture toughness, and superior optical properties (near-infrared and ultraviolet transmittance) compared to those produced by traditional melting-cooling processes.
-
Uniform Heating and High Sintering Temperature:
- The SPS method ensures uniform heating throughout the material, which is crucial for achieving consistent material properties. The high sintering temperature capability of SPS allows for the rapid sintering of dense sintered bodies, making it suitable for a wide range of advanced material applications.
In summary, spark plasma sintering is a versatile and efficient technique that leverages electric current and rapid heating to achieve high-density material consolidation. Its ability to operate at lower temperatures and shorter times, along with its capacity to produce materials with superior properties, makes it an invaluable tool in the field of advanced material fabrication.
Summary Table:
Key Aspect | Description |
---|---|
Electric Current | Pulsed direct current passes through the die and material, enabling dual heating. |
High Heating Rate | Up to 1000°C/min, allowing lower temperatures and shorter sintering times. |
Sintering Steps | Composition, compression, and heat application for rapid densification. |
Die as Heat Source | Graphite die conducts current, ensuring uniform heating and rapid sintering. |
Advantages | Simple operation, low technical requirements, and fast sintering speed. |
Amorphous Materials | Produces materials with superior hardness, toughness, and optical properties. |
Uniform Heating | Ensures consistent material properties and high sintering temperatures. |
Unlock the potential of advanced materials with spark plasma sintering—contact us today to learn more!