Tempering is a heat treatment process used to reduce the hardness of a material, typically after it has been hardened through processes like quenching. While hardening increases hardness and strength, it often makes the material brittle. Tempering addresses this by reheating the hardened material to a specific temperature below its critical point, allowing for controlled structural changes. This process reduces internal stresses, improves toughness, and balances hardness with ductility. The result is a material that retains sufficient hardness while being less prone to cracking or failure under stress.
Key Points Explained:
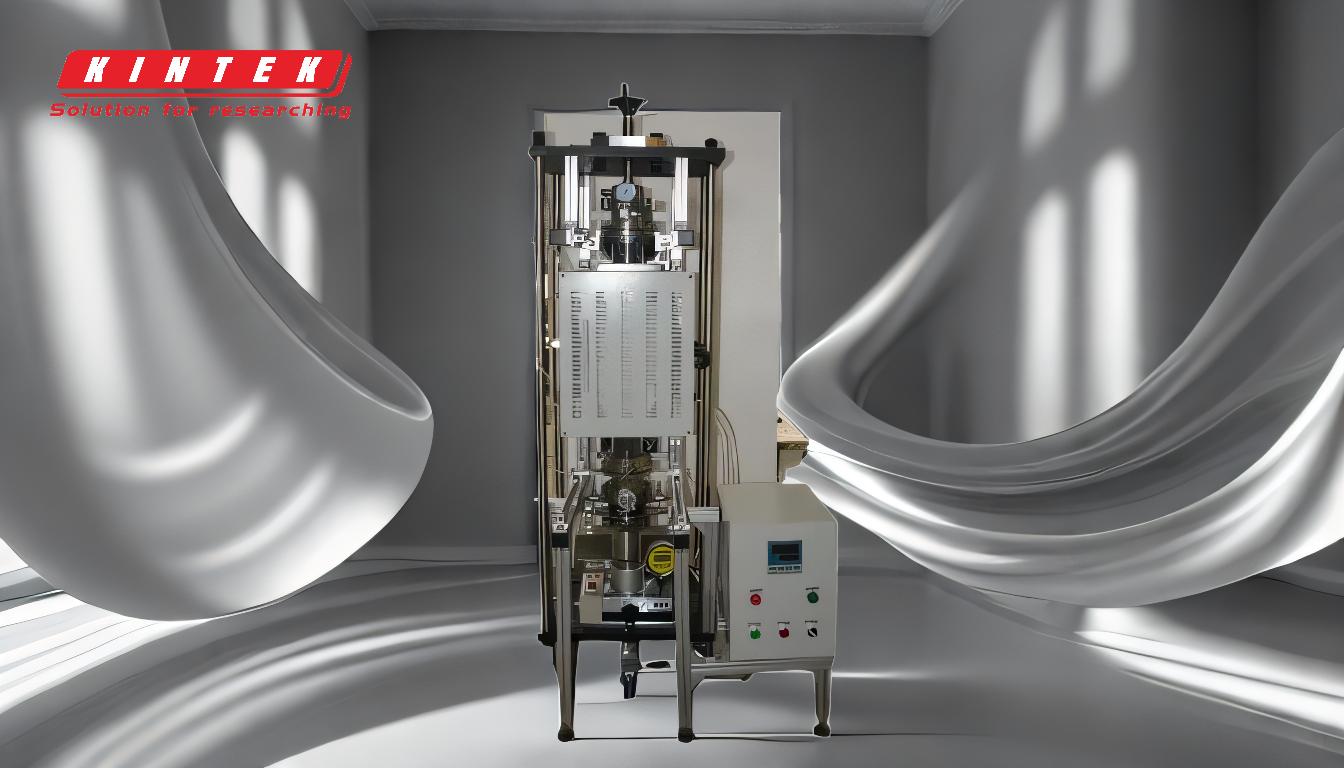
-
Purpose of Tempering:
- Tempering is primarily used to reduce the brittleness of hardened materials.
- It balances hardness with toughness, making the material more suitable for practical applications.
- By reducing internal stresses, tempering minimizes the risk of cracking or failure.
-
Mechanism of Hardness Reduction:
- During hardening (e.g., quenching), the material's microstructure transforms into a hard but brittle phase, such as martensite in steel.
- Tempering reheats the material to a temperature below its critical point, allowing the martensite to partially decompose into softer phases like ferrite and cementite.
- This decomposition reduces hardness but increases ductility and toughness.
-
Temperature and Time Control:
- The tempering temperature determines the extent of hardness reduction. Higher temperatures result in greater softening.
- The duration of tempering also affects the final properties. Longer tempering times allow more complete structural changes.
- Precise control of temperature and time ensures the material achieves the desired balance of hardness and toughness.
-
Impact on Material Properties:
- Hardness: Tempering reduces hardness by transforming brittle martensite into softer microstructures.
- Toughness: The material becomes more resistant to impact and less prone to cracking.
- Ductility: Tempering improves the material's ability to deform without breaking, making it more workable.
-
Applications of Tempered Materials:
- Tempered materials are widely used in applications requiring a balance of strength and durability, such as automotive components, tools, and construction materials.
- The process ensures that parts can withstand mechanical stress without failing due to brittleness.
-
Comparison with Hardening:
- Hardening increases hardness but often at the expense of toughness.
- Tempering complements hardening by addressing its limitations, resulting in a material that is both strong and durable.
By carefully controlling the tempering process, manufacturers can tailor the mechanical properties of materials to meet specific application requirements, ensuring optimal performance and longevity.
Summary Table:
Aspect | Details |
---|---|
Purpose | Reduces brittleness, balances hardness and toughness, minimizes cracking. |
Mechanism | Reheats hardened material to decompose brittle phases into softer ones. |
Temperature & Time | Higher temps = greater softening; longer times = more structural changes. |
Impact on Properties | Reduces hardness, improves toughness and ductility. |
Applications | Automotive parts, tools, construction materials. |
Comparison to Hardening | Hardening increases hardness; tempering improves toughness. |
Optimize your materials with precise tempering—contact our experts today for tailored solutions!