The sintering process is a critical step in transforming powdered materials, such as zirconia, into dense, durable, and high-performance ceramics. It involves heating the material below its melting point to fuse particles together, reducing porosity and increasing density. This process is influenced by factors like temperature, heating rate, pressure, particle size, and composition. A zirconia sintering furnace plays a vital role in ensuring precise temperature control and consistent material properties. The process occurs in three stages: shaping the powder blend, removing the bonding agent, and fusing particles to achieve the final hardened structure.
Key Points Explained:
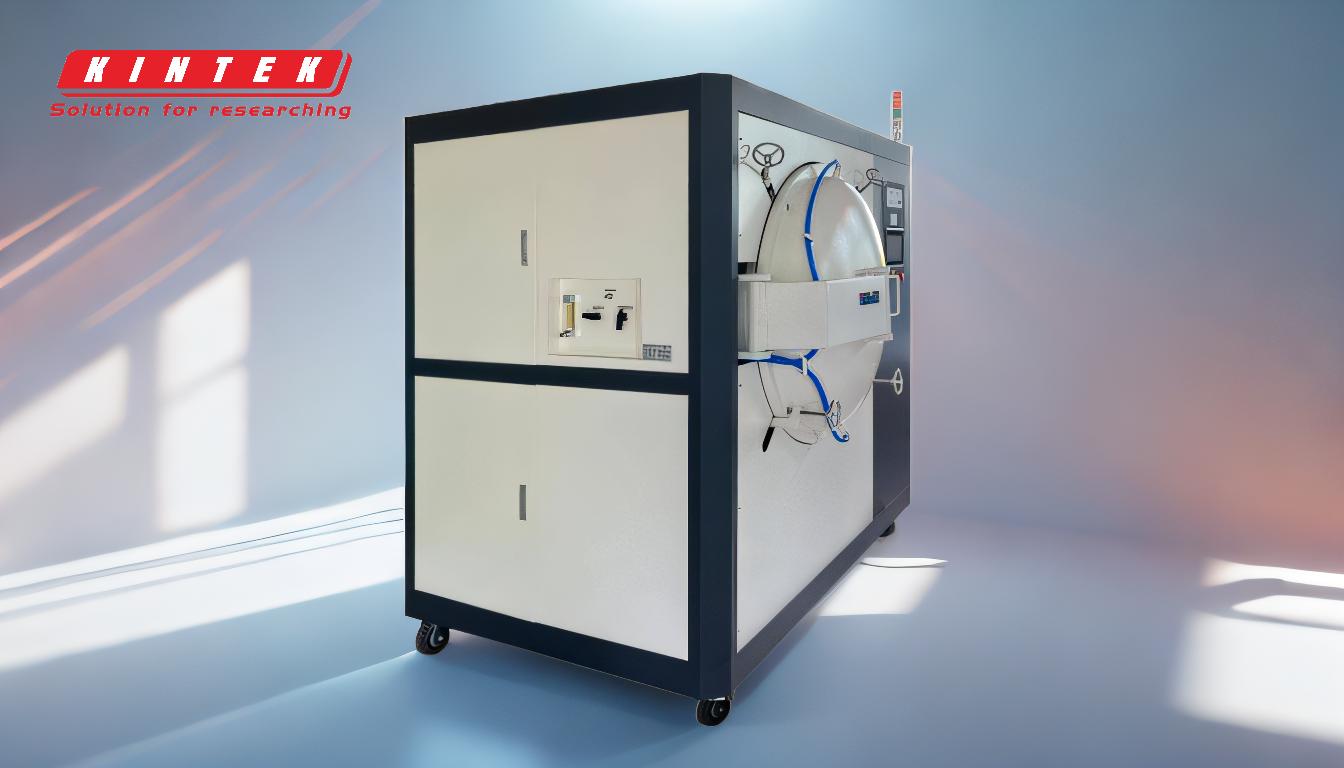
-
Definition and Purpose of Sintering:
- Sintering is a thermal process that fuses powdered materials, such as zirconia, into a solid mass without reaching a liquid state. This process reduces porosity, increases density, and enhances mechanical properties like hardness and strength.
- It is widely used in ceramic production, including zirconia, to create materials with high thermal resistance and durability.
-
Stages of the Sintering Process:
-
Stage 1: Shaping the Powder Blend:
- A primary powder blend, often mixed with a bonding agent (e.g., water, wax, or polymer), is formed into the desired shape. The bonding agent holds the powder particles together temporarily.
-
Stage 2: Removal of the Bonding Agent:
- During heating, the bonding agent evaporates or burns away, leaving behind a porous structure of the primary powder particles.
-
Stage 3: Particle Fusion:
- The temperature is increased to a point where the primary particles begin to melt at their surfaces. This causes them to fuse together, reducing porosity and forming a dense, solid structure.
-
Stage 1: Shaping the Powder Blend:
-
Factors Influencing Sintering:
-
Temperature:
- Determines the sintering kinetics and final material properties. Higher temperatures accelerate particle fusion but must remain below the material’s melting point.
-
Heating Rate:
- Affects densification. A controlled heating rate ensures uniform shrinkage and minimizes defects.
-
Pressure:
- Enhances particle rearrangement and eliminates porosity, especially in pressure-assisted sintering methods.
-
Particle Size and Composition:
- Smaller particles and homogeneous compositions promote better densification and uniformity in the final product.
-
Temperature:
-
Role of a Zirconia Sintering Furnace:
- A zirconia sintering furnace is essential for precise temperature control and uniform heating. Its high-precision controller ensures stable temperatures throughout the process, resulting in consistent material properties and high-quality end products.
- These furnaces use solid-state sintering methods, maintaining temperatures below the powder’s melting point to shape the material without liquefaction.
-
Importance of Sintering in Zirconia Production:
- Sintering significantly impacts the mechanical strength and thermal resistance of zirconia. By fusing particles without melting, the process creates a dense, durable material suitable for applications like dental implants, cutting tools, and industrial components.
-
Applications and Benefits:
- Sintered zirconia is used in industries requiring high-performance ceramics, such as healthcare, aerospace, and manufacturing. The process ensures materials with excellent hardness, wear resistance, and thermal stability.
By understanding the sintering process and the role of advanced equipment like a zirconia sintering furnace, manufacturers can optimize production and achieve superior material properties for various applications.
Summary Table:
Aspect | Details |
---|---|
Definition | Fuses powdered materials without melting, reducing porosity and increasing density. |
Stages | 1. Shaping the powder blend 2. Removing the bonding agent 3. Particle fusion |
Key Factors | Temperature, heating rate, pressure, particle size, and composition. |
Role of Furnace | Ensures precise temperature control and uniform heating for consistent results. |
Applications | Dental implants, cutting tools, industrial components, and more. |
Optimize your sintering process with advanced equipment—contact us today for expert guidance!