Forging pressure is applied differently in a forging press compared to a drop hammer due to the distinct mechanisms and principles of operation. A forging press applies continuous and controlled pressure, often using hydraulic or mechanical systems, to shape the metal. This method allows for precise control over the force and deformation, making it suitable for complex shapes and high-precision work. In contrast, a drop hammer relies on the kinetic energy of a falling weight to deliver a sudden impact, which is more suitable for simpler shapes and bulk deformation. The key differences lie in the nature of the force application (continuous vs. impact), control over the process, and the types of forging operations each method is best suited for.
Key Points Explained:
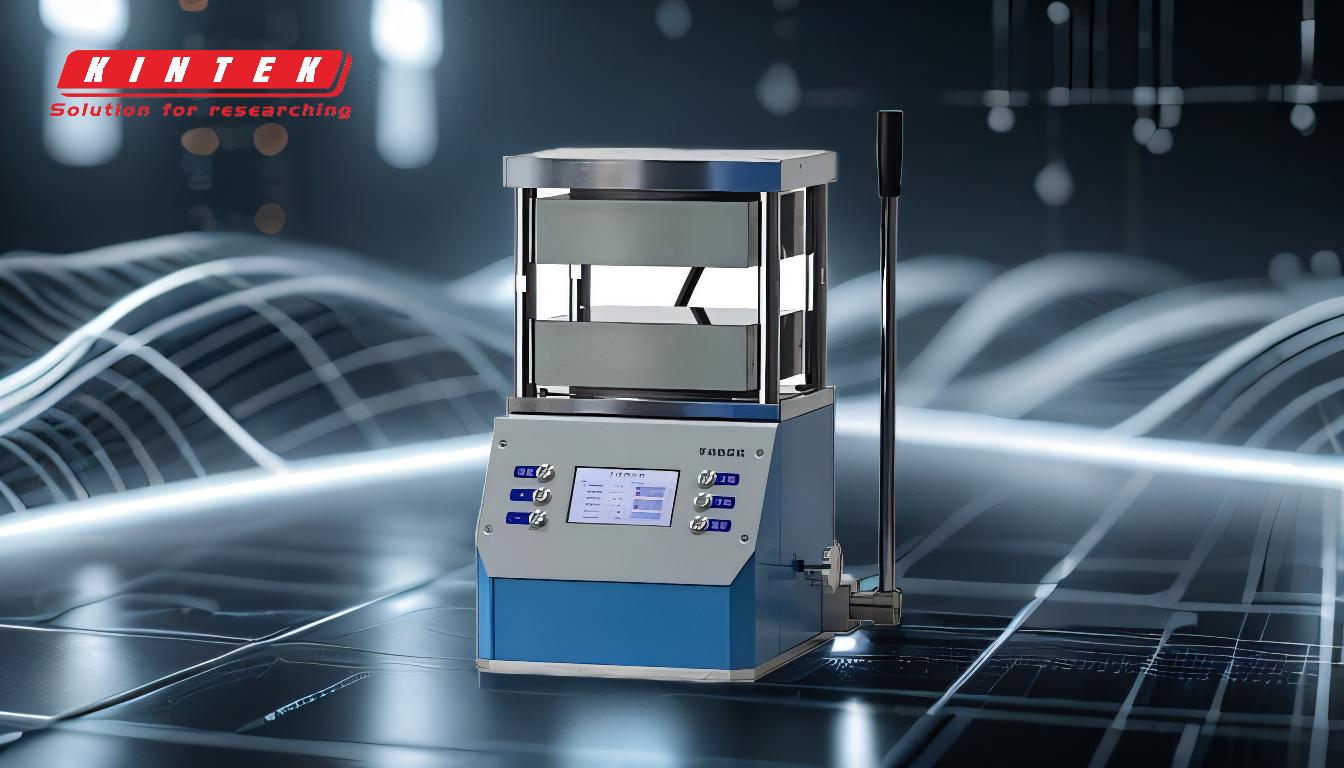
-
Mechanism of Force Application:
- Forging Press: In a forging press, the pressure is applied continuously and gradually. Hydraulic presses use fluid pressure to generate force, while mechanical presses use a screw or crank mechanism. This allows for a steady and controlled application of force, which is ideal for shaping complex geometries and achieving precise dimensions.
- Drop Hammer: A drop hammer applies force through the kinetic energy of a falling weight. The hammer is lifted and then dropped onto the workpiece, delivering a sudden impact. This method is more about delivering a high amount of energy in a short time, which is effective for simpler shapes and bulk deformation.
-
Control and Precision:
- Forging Press: The continuous and controlled nature of the force application in a forging press allows for greater precision. Operators can adjust the pressure and speed to achieve the desired deformation, making it suitable for high-precision work and complex shapes.
- Drop Hammer: The impact nature of a drop hammer means that the force is applied suddenly and with less control. This makes it less suitable for precise work but effective for simpler, bulkier shapes where the primary goal is to deform the metal quickly.
-
Types of Forging Operations:
- Forging Press: Due to its controlled force application, a forging press is often used for operations that require high precision and complex shapes, such as closed-die forging and precision forging. It is also used for materials that require careful handling to avoid cracking or other defects.
- Drop Hammer: The drop hammer is typically used for open-die forging and operations where the goal is to quickly deform the metal into a simpler shape. It is less suitable for complex shapes but effective for bulk deformation and simpler geometries.
-
Energy Efficiency and Speed:
- Forging Press: The continuous application of force in a forging press can be more energy-efficient for certain operations, especially those requiring precision and control. However, the process can be slower compared to a drop hammer.
- Drop Hammer: The drop hammer delivers a high amount of energy in a short time, making it faster for certain types of forging. However, the sudden impact can lead to energy losses and may not be as efficient for precise or complex work.
-
Material Considerations:
- Forging Press: The controlled force application in a forging press is better suited for materials that are sensitive to cracking or require careful handling. It allows for better control over the deformation process, reducing the risk of defects.
- Drop Hammer: The impact nature of a drop hammer is more suitable for materials that can withstand sudden deformation without cracking. It is less suitable for materials that require careful handling or are prone to defects under sudden impact.
In summary, the choice between a forging press and a drop hammer depends on the specific requirements of the forging operation, including the complexity of the shape, the precision required, and the material being forged. Each method has its strengths and is chosen based on the desired outcome of the forging process.
Summary Table:
Aspect | Forging Press | Drop Hammer |
---|---|---|
Force Application | Continuous and controlled pressure (hydraulic/mechanical systems) | Sudden impact from kinetic energy of a falling weight |
Control & Precision | High precision, adjustable pressure and speed, ideal for complex shapes | Less control, sudden force, suitable for simpler shapes and bulk deformation |
Forging Operations | Closed-die forging, precision forging, complex shapes | Open-die forging, bulk deformation, simpler geometries |
Energy Efficiency | More energy-efficient for precision work, slower process | Faster for bulk deformation, but less efficient for precise or complex work |
Material Suitability | Better for sensitive materials requiring careful handling | Suitable for materials that withstand sudden deformation without cracking |
Need help choosing the right forging method for your project? Contact our experts today!