The cost of carburizing depends on several factors, including the type of material, the desired case depth, the carburizing method (atmosphere or vacuum), and the scale of production. While exact costs are not provided in the references, the process is influenced by time, temperature, and the specific requirements of the application. Atmosphere and vacuum carburizing each have unique advantages, and the choice between them depends on the product's performance needs and manufacturing constraints. Below, we explore the key factors affecting carburizing costs and how they influence the overall pricing.
Key Points Explained:
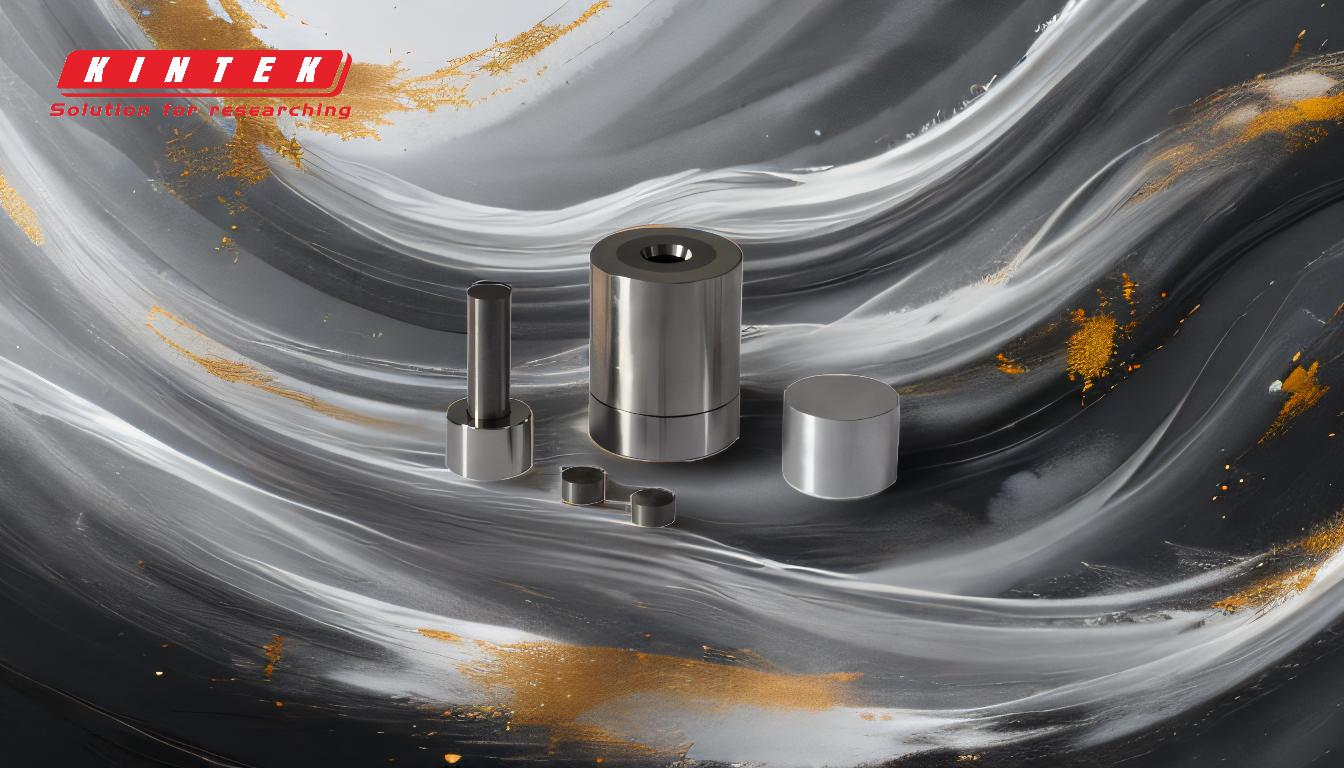
-
Factors Influencing Carburizing Costs
- Material Type: The cost varies depending on the type of material being carburized. Different alloys and metals require specific conditions, which can affect the overall expense.
- Case Depth Requirements: Deeper case depths require longer exposure times and higher temperatures, increasing energy consumption and process time.
- Carburizing Method: Atmosphere carburizing is generally less expensive than vacuum carburizing, but the latter offers advantages like reduced distortion and better control over the process, which may justify the higher cost for certain applications.
-
Time and Temperature
- The carburizing process is heavily dependent on time and temperature. Higher temperatures and longer times result in greater case thickness but also increase energy costs and equipment wear.
- For example, achieving a case depth of 0.5 mm might take 4 hours at 925°C, while a deeper case depth of 1.5 mm could require 12 hours or more. This directly impacts labor and operational costs.
-
Carburizing Methods
- Atmosphere Carburizing: This method uses a carbon-rich atmosphere to diffuse carbon into the metal surface. It is cost-effective for large-scale production but may require additional post-processing to clean the parts.
- Vacuum Carburizing: This method uses a vacuum environment to introduce carbon, offering better control and reducing oxidation. While more expensive, it is ideal for high-precision components and can reduce post-processing costs.
-
Production Scale
- Larger production runs benefit from economies of scale, reducing the per-unit cost of carburizing.
- Small batches or custom orders may incur higher costs due to setup times and less efficient use of resources.
-
Additional Costs
- Energy Consumption: Higher temperatures and longer processing times increase energy usage, which is a significant cost factor.
- Equipment Maintenance: Frequent use at high temperatures can lead to wear and tear, requiring regular maintenance and replacement of parts.
- Post-Processing: Depending on the application, additional steps like quenching, tempering, or cleaning may be necessary, adding to the overall cost.
-
Estimating Costs
- While exact pricing is not provided in the references, a rough estimate for atmosphere carburizing might range from $1 to $5 per pound of material, depending on the factors mentioned above.
- Vacuum carburizing could cost 20-50% more due to the specialized equipment and process control required.
-
Choosing the Right Method
- The choice between atmosphere and vacuum carburizing should be based on the specific needs of the product. For example, vacuum carburizing is ideal for high-performance components where precision and reduced distortion are critical, even if it comes at a higher cost.
By understanding these key points, purchasers can make informed decisions about carburizing processes, balancing cost with performance requirements to achieve the best value for their specific application.
Summary Table:
Factor | Impact on Cost |
---|---|
Material Type | Different alloys and metals require specific conditions, affecting overall expense. |
Case Depth | Deeper case depths increase energy consumption and processing time. |
Carburizing Method | Vacuum carburizing is more expensive but offers precision and reduced distortion. |
Production Scale | Larger runs reduce per-unit costs; small batches may incur higher expenses. |
Time & Temperature | Higher temperatures and longer times increase energy and labor costs. |
Additional Costs | Includes energy consumption, equipment maintenance, and post-processing. |
Need help choosing the right carburizing method for your project? Contact our experts today for tailored advice!